Thermal evaporation is a widely used physical vapor deposition (PVD) technique for creating thin films of materials that remain stable in a vapor state. The process involves heating a target material in a high-vacuum environment until it evaporates. The vaporized material then travels through the vacuum and condenses onto a substrate, forming a thin film. The heating can be achieved through resistive heating (using a refractory metal boat or coil) or electron beam evaporation (using a focused beam of high-energy electrons). This method is favored for its ability to produce high-purity films with excellent adhesion to substrates, making it suitable for applications in electronics, optics, and coatings.
Key Points Explained:
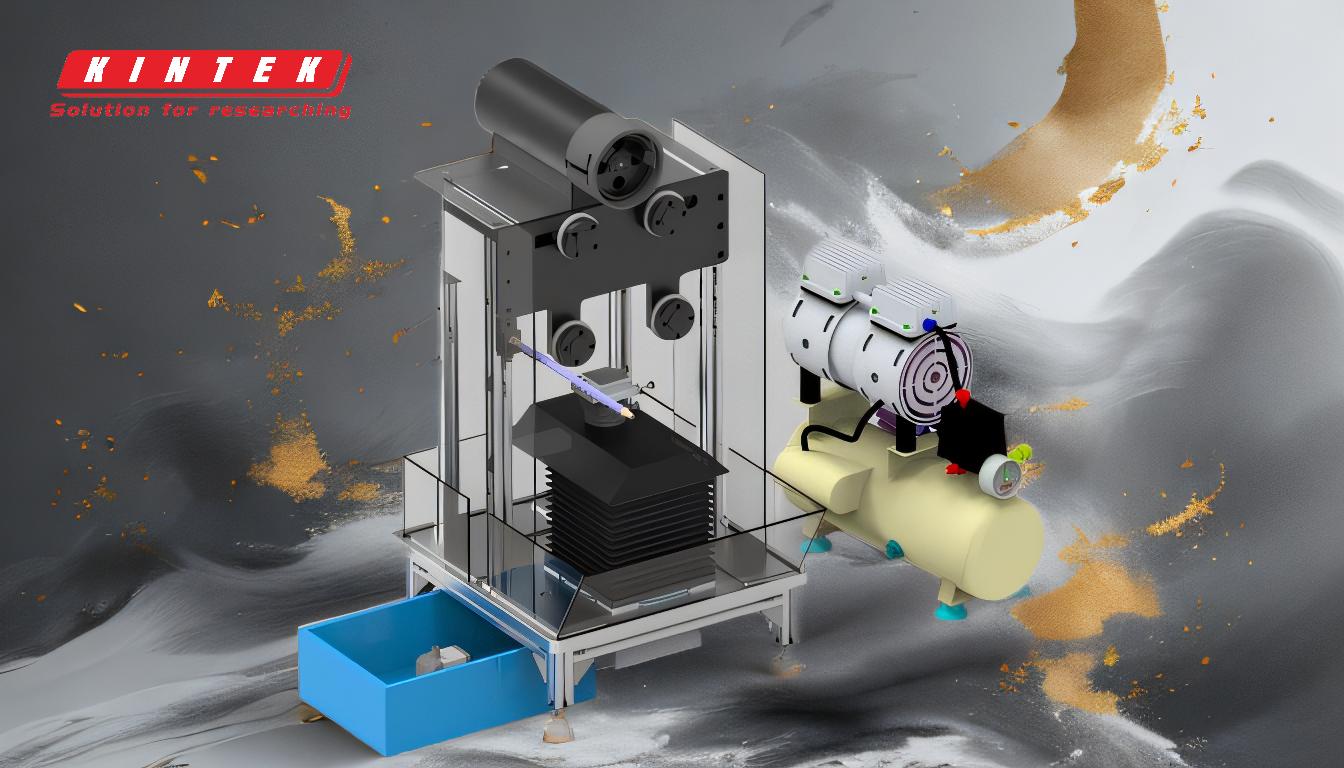
-
High-Vacuum Environment:
- Thermal evaporation is conducted in a high-vacuum chamber to ensure that the vaporized material can travel unimpeded to the substrate.
- A vacuum pump maintains the low-pressure environment, reducing the likelihood of contamination from residual gases and ensuring a free path for the vaporized particles.
- The high vacuum also minimizes scattering of the vaporized atoms, leading to more uniform and high-quality thin films.
-
Heating Mechanisms:
-
Resistive Heating (Joule Heating):
- A refractory metal boat or coil is used to hold the target material. Electric current is passed through the boat or coil, generating heat due to electrical resistance.
- The material is heated to its evaporation point, where it transitions from solid to vapor.
- This method is simple and cost-effective, making it suitable for materials with lower melting points.
-
Electron Beam Evaporation:
- A focused beam of high-energy electrons is directed at the target material, providing localized heating.
- This method is ideal for materials with high melting points, as it allows for precise control of the heating process and minimizes contamination from the heating element.
-
Resistive Heating (Joule Heating):
-
Evaporation and Condensation:
- The target material is heated until it reaches its evaporation point, releasing vapor particles into the chamber.
- These vapor particles travel through the vacuum and deposit onto the substrate, forming a thin film through condensation.
- The process ensures high purity and excellent adhesion of the film to the substrate, as the vaporized material is free from impurities and reacts minimally with the environment.
-
Evaporation Sources:
-
Boats and Coils:
- These are commonly used in resistive heating setups. The material is placed in a dimple or on a ribbon, and the electric current heats the structure to evaporate the material.
-
Crucibles:
- Used in both resistive and electron beam evaporation, crucibles hold the material and are heated to high temperatures to induce vaporization.
-
Baskets:
- Similar to boats and coils, baskets are used to hold the material and are heated to achieve evaporation.
-
Boats and Coils:
-
Material Considerations:
- Only materials with a much higher vapor pressure than the heating element can be deposited without contamination.
- The process is suitable for metals, alloys, and other materials that remain stable in a vapor state.
- The choice of material and heating method depends on the desired film properties, such as purity, thickness, and adhesion.
-
Applications:
-
Electronics:
- Used to deposit thin films of metals and alloys for semiconductor devices, conductive layers, and interconnects.
-
Optics:
- Applied in the fabrication of optical coatings, mirrors, and filters.
-
Coatings:
- Used for protective and decorative coatings on various substrates, including glass, plastics, and metals.
-
Electronics:
-
Advantages:
- High-purity films with excellent adhesion.
- Simple and cost-effective for materials with lower melting points.
- Precise control over film thickness and uniformity.
-
Limitations:
- Requires a high-vacuum environment, which can be expensive to maintain.
- Limited to materials that can be vaporized without decomposing.
- Electron beam evaporation can be complex and costly compared to resistive heating.
By understanding these key points, a purchaser can make informed decisions about the equipment and materials needed for thermal evaporation processes, ensuring optimal results for their specific applications.
Summary Table:
Aspect | Details |
---|---|
Environment | High-vacuum chamber to ensure unimpeded vapor travel and minimal scattering. |
Heating Mechanisms | Resistive heating (simple, cost-effective) or electron beam evaporation (precise, high melting points). |
Evaporation Sources | Boats, coils, crucibles, and baskets for holding and heating materials. |
Material Considerations | Metals, alloys, and stable vapor-state materials with high vapor pressure. |
Applications | Electronics, optics, and protective/decorative coatings. |
Advantages | High-purity films, excellent adhesion, precise thickness control. |
Limitations | High-vacuum costs, limited to vaporizable materials, complex electron beam setups. |
Ready to enhance your thin film processes? Contact us today for expert guidance and solutions!