Tire pyrolysis is a thermal decomposition process that converts waste tires into valuable products such as fuel oil, carbon black, steel wire, and uncondensable gas. The process involves feeding waste tires into a pyrolysis reactor, heating them in an oxygen-free environment to break down the rubber into smaller molecules, and then condensing the resulting vapors to collect liquid oil. The solid residues, including carbon black and steel wire, are separated and collected. The process is highly efficient and environmentally friendly, as it recycles waste tires into reusable resources. Key factors influencing the process include temperature, pyrolysis method, and reactor design.
Key Points Explained:
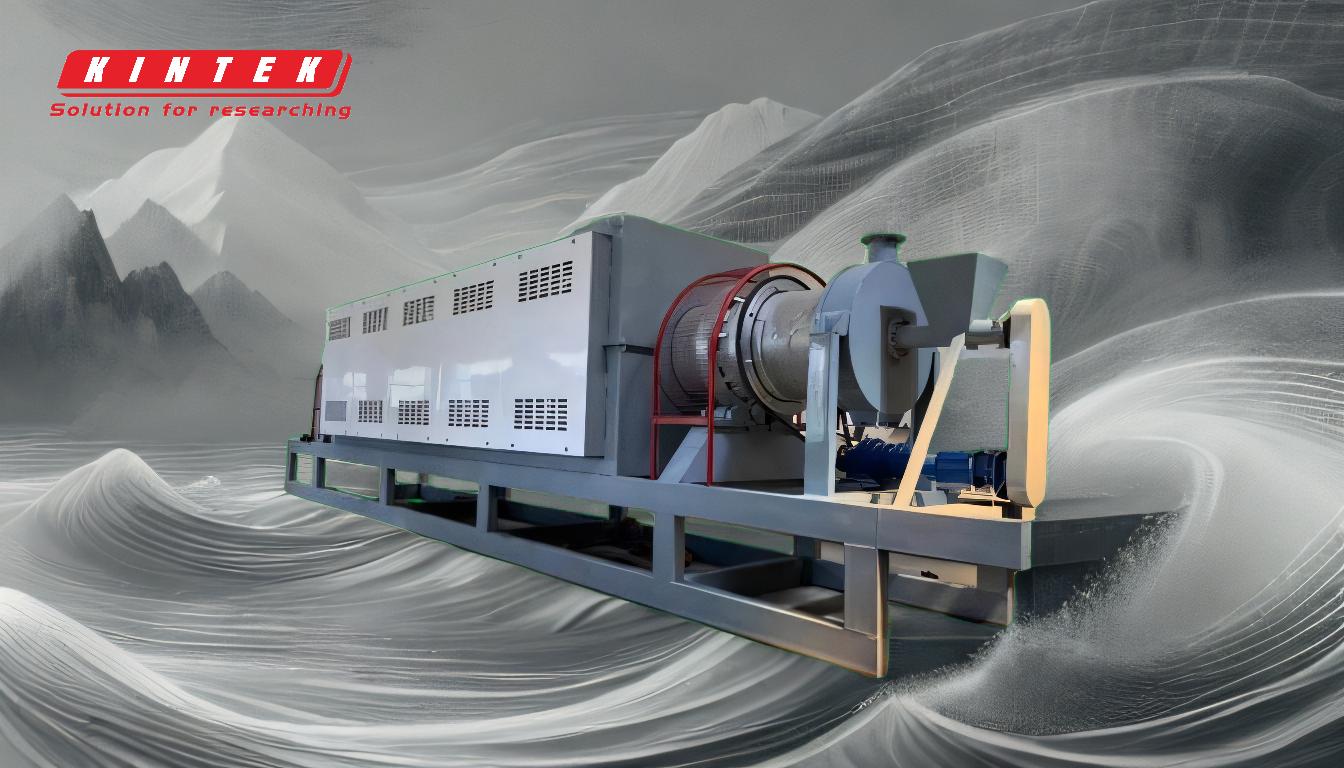
-
Feeding Waste Tires into the Reactor:
- The process begins by feeding whole or shredded waste tires into a pyrolysis reactor. The tires are typically un-shredded, although some processes may involve shredding to increase efficiency.
- The reactor is designed to handle the high temperatures required for pyrolysis and is sealed to prevent oxygen from entering, which could lead to combustion.
-
Heating the Reactor:
- Once the tires are inside the reactor, the heating process begins. The reactor is placed inside a furnace, and the temperature is gradually increased to melt and vaporize the rubber.
- The heating process is carefully controlled to ensure that the rubber's main chain cracks into monomers, biopolymers, and fragments. This thermal decomposition occurs in the absence of oxygen, a condition known as anaerobic pyrolysis.
-
Depolymerization and Degassing:
- The depolymerization process runs for 3-5 hours, during which the rubber breaks down into smaller molecules. This process generates gas by-products, which are a mixture of condensable and non-condensable gases.
- The gases flow through a heat exchanger, where the condensable hydrocarbons are separated from the non-condensable gases. The condensable hydrocarbons are collected as pyrolysis oil, while the non-condensable gases are desulfurized and cleaned before being stored in a gas pressure tank.
-
Condensation and Collection of Pyrolysis Oil:
- The condensable hydrocarbons are cooled in a heat exchanger, causing them to condense into liquid pyrolysis oil. This oil can be used for various purposes, including heating, power generation, or even hydrogen production.
- The quality and composition of the pyrolysis oil depend on factors such as the pyrolysis temperature and the type of tires used.
-
Separation of Solid Residues:
- After the pyrolysis process is complete, the solid residues, including carbon black and steel wire, are separated from the reactor. Carbon black is a valuable material used in various industries, including rubber manufacturing and ink production.
- The steel wire, which is typically embedded in the tires, is also recovered and can be recycled for use in other applications.
-
Environmental and Economic Benefits:
- Tire pyrolysis is an environmentally friendly process that helps reduce the volume of waste tires in landfills. By converting waste tires into valuable products, the process contributes to resource conservation and reduces the need for virgin materials.
- The process also offers economic benefits, as the products generated (fuel oil, carbon black, steel wire, and gas) can be sold or used in various industrial applications.
-
Factors Influencing the Process:
- The efficiency and output of the tire pyrolysis process depend on several factors, including the pyrolysis method, temperature, and reactor design. Higher temperatures generally lead to a higher yield of gas and oil, while lower temperatures favor the production of carbon black.
- The type of tires used also affects the composition of the end products. For example, tires with a higher rubber content will produce more oil, while those with more steel will yield more steel wire.
-
Continuous vs. Batch Processing:
- Some pyrolysis systems operate in a continuous mode, where tires are continuously fed into the reactor, and products are continuously collected. This method is more efficient and suitable for large-scale operations.
- Other systems use a batch process, where a set amount of tires is processed at a time. After each batch, the reactor is emptied, and a new batch is loaded. This method is simpler but may be less efficient for large-scale operations.
In summary, tire pyrolysis is a complex but highly efficient process that converts waste tires into valuable resources. The process involves several key steps, including feeding, heating, depolymerization, condensation, and separation, each of which is carefully controlled to maximize the yield and quality of the end products. The process not only helps reduce environmental pollution but also offers significant economic benefits by turning waste into valuable commodities.
Summary Table:
Step | Description |
---|---|
Feeding Waste Tires | Whole or shredded tires are fed into a sealed pyrolysis reactor. |
Heating the Reactor | Rubber is melted and vaporized in an oxygen-free environment. |
Depolymerization | Rubber breaks into smaller molecules, producing condensable and non-condensable gases. |
Condensation | Condensable hydrocarbons are cooled into pyrolysis oil. |
Separation | Carbon black and steel wire are separated and collected. |
Benefits | Reduces landfill waste, conserves resources, and generates valuable products. |
Factors | Temperature, pyrolysis method, and reactor design influence efficiency. |
Processing Modes | Continuous or batch processing options available. |
Transform waste tires into valuable resources with tire pyrolysis—contact us today to learn more!