The process of tyre pyrolysis oil refining involves converting waste tire-derived pyrolysis oil into usable fuel products through distillation and upgrading. The raw pyrolysis oil is pumped into a distillation reactor, heated to vaporize the oil, and then condensed to separate it into different fractions. Non-condensable gases are recycled for heating, while pollutants are treated to ensure environmental compliance. The refined oil can be further upgraded by removing impurities like oxygen or nitrogen, and processes like decolorization and deodorization can transform it into non-standard diesel. This multi-step process ensures efficient resource utilization and minimizes environmental impact.
Key Points Explained:
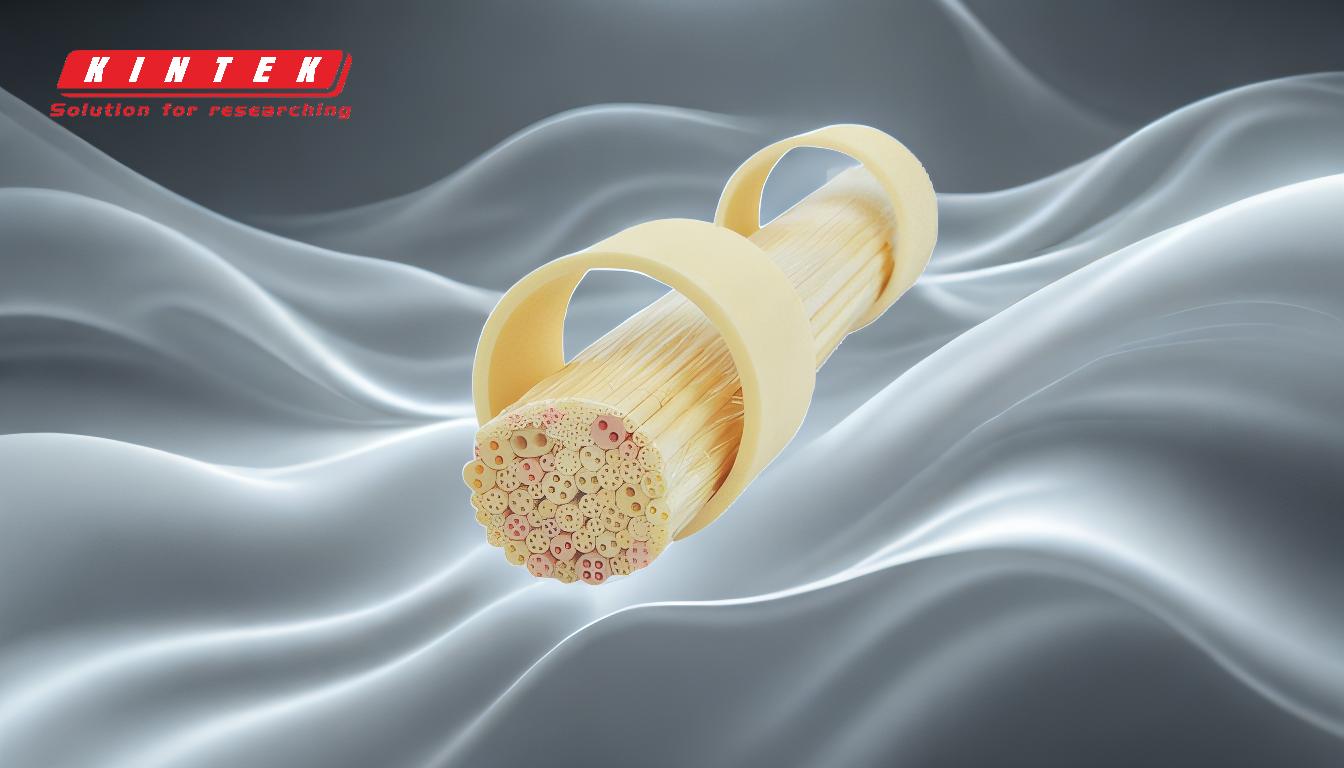
-
Feeding and Heating the Reactor:
- Waste tire pyrolysis oil is pumped into a distillation reactor.
- The reactor is heated using energy sources such as coal, wood, natural gas, fuel oil, or electricity.
- The heat causes the liquid oil to vaporize, forming oil gas.
-
Distillation Process:
- The oil gas is passed through cooling pipes and condensers to liquefy it into fuel oil.
- Distillation relies on the difference in boiling points of the components in the oil mixture.
- The process involves multiple steps of vaporization and condensation to achieve separation.
-
Recycling Non-Liquefiable Gases:
- Gases such as methane, ethane, propane, and butane, which cannot be liquefied, are recycled back into the system.
- These gases are used to heat the reactor, improving energy efficiency and reducing external energy requirements.
-
Pollution Control:
- Smoke generated during the process is treated using a dedusting system to remove particulate matter.
- Exhaust gases are processed to ensure they meet environmental standards before being released into the atmosphere.
-
Upgrading the Refined Oil:
- The distilled oil can be further upgraded by removing oxygen (in the case of bio-oil) or nitrogen (in the case of algal bio-oil).
- This improves the quality of the oil, making it more suitable for use as a fuel.
-
Decolorization and Deodorization:
- Heavy oil extracted from waste tires can undergo decolorization and deodorization processes.
- These processes refine the fuel oil into non-standard diesel, which can be used in various industrial applications.
-
Final Product Collection:
- The end products of the refining process include fuel oil, carbon black, and steel wire.
- These materials are collected and can be used or sold for further applications, ensuring minimal waste.
By following these steps, tyre pyrolysis oil refining transforms waste into valuable resources while adhering to environmental and efficiency standards.
Summary Table:
Step | Process | Outcome |
---|---|---|
Feeding and Heating | Pyrolysis oil is pumped into a reactor and heated using various energy sources. | Oil vaporizes into gas for further processing. |
Distillation | Oil gas is cooled and condensed into fuel oil based on boiling point differences. | Separation of fuel oil fractions for refining. |
Recycling Non-Liquefiable Gases | Non-condensable gases like methane are recycled to heat the reactor. | Improved energy efficiency and reduced external energy needs. |
Pollution Control | Smoke and exhaust gases are treated to meet environmental standards. | Minimized environmental impact and compliance with regulations. |
Upgrading Refined Oil | Impurities like oxygen or nitrogen are removed to improve oil quality. | High-quality fuel suitable for industrial use. |
Decolorization & Deodorization | Heavy oil is refined into non-standard diesel through decolorization and deodorization. | Enhanced usability and marketability of the fuel. |
Final Product Collection | Fuel oil, carbon black, and steel wire are collected for reuse or sale. | Zero waste and maximum resource utilization. |
Discover how tyre pyrolysis oil refining can transform waste into valuable fuel—contact us today to learn more!