Physical vapor deposition (PVD) is a versatile and widely used process for creating thin films and coatings on various substrates. Over the past century, PVD has evolved significantly, with advancements like plasma-assisted PVD (PAPVD) introducing various power source technologies. These technologies, including DC diode, triode, RF, pulsed plasma, and ion beam-assisted coatings, have expanded the applications and precision of PVD. The products of PVD are high-quality, durable coatings that enhance the performance, durability, and functionality of materials in industries such as electronics, optics, automotive, and aerospace.
Key Points Explained:
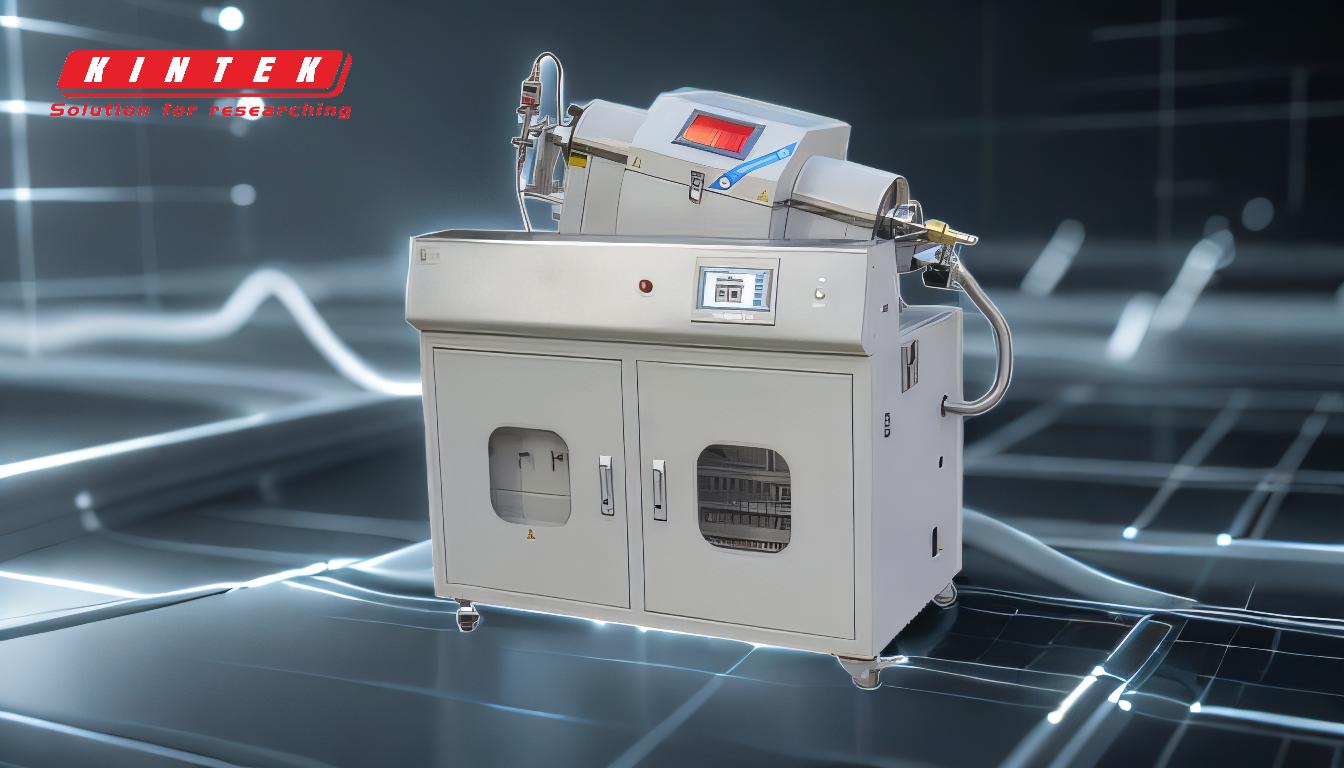
-
Definition of Physical Vapor Deposition (PVD):
- PVD is a vacuum coating process where materials are vaporized from a solid source and then deposited onto a substrate to form a thin film. This process is used to create coatings with specific properties such as hardness, wear resistance, and corrosion resistance.
-
Types of PVD Technologies:
- DC Diode: Uses a direct current to generate a plasma that assists in the deposition process. It is commonly used for metallic coatings.
- Triode: Incorporates an additional electrode to control the plasma density, allowing for more precise coatings.
- Radio-Frequency (RF): Utilizes RF energy to create a plasma, which is effective for depositing insulating materials.
- Pulsed Plasma: Involves pulsing the power to the plasma, which can reduce stress in the coatings and improve adhesion.
- Ion Beam-Assisted Coatings: Uses an ion beam to enhance the properties of the deposited film, such as increasing density and improving adhesion.
-
Applications of PVD Coatings:
- Electronics: PVD is used to deposit thin films on semiconductors, solar panels, and display screens to enhance conductivity, durability, and optical properties.
- Optics: Coatings on lenses and mirrors to improve reflectivity, reduce glare, and protect against environmental damage.
- Automotive: PVD coatings on engine components, decorative trim, and tools to improve wear resistance, reduce friction, and enhance aesthetic appeal.
- Aerospace: Protective coatings on turbine blades, structural components, and other critical parts to withstand extreme temperatures and corrosive environments.
-
Advantages of PVD Coatings:
- Durability: PVD coatings are highly durable and resistant to wear, corrosion, and high temperatures.
- Precision: The process allows for precise control over the thickness and composition of the coatings.
- Versatility: PVD can be used on a wide range of materials, including metals, ceramics, and polymers.
- Environmental Friendliness: PVD is a clean process that produces minimal waste and does not involve harmful chemicals.
-
Challenges and Considerations:
- Cost: The equipment and process can be expensive, making it less accessible for small-scale applications.
- Complexity: The process requires specialized knowledge and equipment, which can be a barrier to entry.
- Uniformity: Achieving uniform coatings on complex geometries can be challenging and may require advanced techniques.
In summary, physical vapor deposition (PVD) is a sophisticated and highly effective method for creating thin films and coatings with superior properties. The evolution of PVD technologies, such as plasma-assisted PVD, has further enhanced its capabilities, making it indispensable in various high-tech industries. Despite some challenges, the benefits of PVD coatings in terms of durability, precision, and versatility make it a preferred choice for many applications.
Summary Table:
Aspect | Details |
---|---|
Product | Thin films and coatings with enhanced durability, precision, and versatility. |
Technologies | DC Diode, Triode, RF, Pulsed Plasma, Ion Beam-Assisted Coatings. |
Applications | Electronics, Optics, Automotive, Aerospace. |
Advantages | Durability, Precision, Versatility, Environmental Friendliness. |
Challenges | High cost, Complexity, Uniformity on complex geometries. |
Interested in leveraging PVD coatings for your industry? Contact us today to learn more!