The purpose of a vacuum in a heat exchanger primarily revolves around optimizing heat transfer efficiency, preventing operational issues, and ensuring the longevity of the equipment. In steam-to-water heat exchangers, a vacuum can help manage condensate buildup, which, if not properly handled, can lead to water hammer and tube damage. Additionally, in heat treatment processes, a vacuum removes air from the chamber, allowing for precise temperature control and preventing unwanted chemical reactions. This ensures consistent performance and extends the lifespan of the heat exchanger.
Key Points Explained:
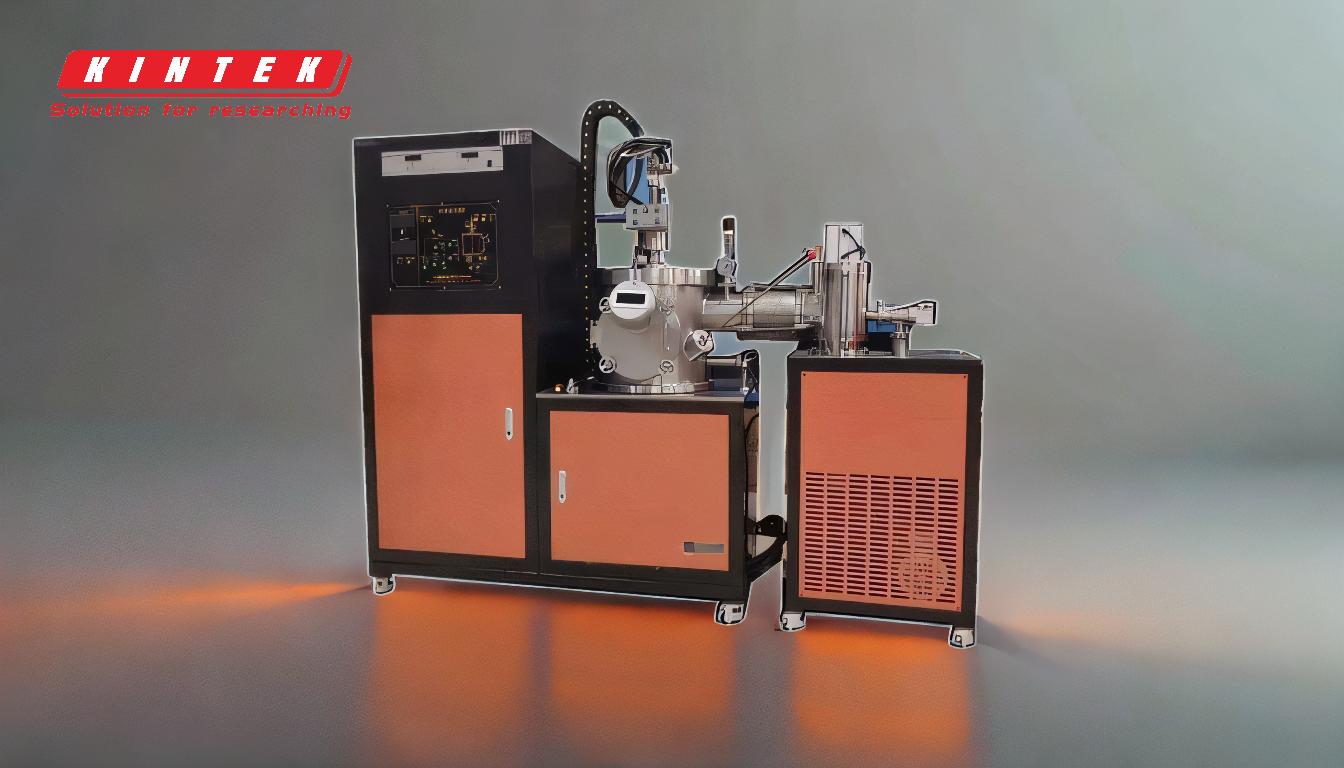
-
Preventing Condensate Buildup and Water Hammer:
- In steam-to-water heat exchangers, steam condenses into water inside the shell. If this condensate is not effectively removed, it can accumulate and cause operational issues.
- Water hammer, a phenomenon caused by the sudden impact of condensate against the tubes, can lead to significant damage. A vacuum helps evacuate the condensate, preventing such issues and ensuring smooth operation.
-
Enhancing Heat Transfer Efficiency:
- A vacuum reduces the presence of non-condensable gases (like air) within the heat exchanger. These gases can act as insulators, reducing the efficiency of heat transfer between the steam and the water.
- By maintaining a vacuum, the heat exchanger operates more efficiently, ensuring that the maximum amount of heat is transferred from the steam to the water.
-
Preventing Tube Damage:
- Accumulated condensate and the resulting water hammer can cause physical damage to the tubes within the heat exchanger. This not only affects performance but also increases maintenance costs.
- A vacuum system helps in the timely removal of condensate, thereby protecting the tubes from damage and extending the lifespan of the heat exchanger.
-
Controlling the Thermal Environment in Heat Treatment:
- In heat treatment applications, a vacuum is used to remove air from the chamber. This allows for precise control over the thermal environment, which is crucial for achieving desired material properties.
- By eliminating air, the vacuum prevents oxidation and other unwanted chemical reactions that could alter the material's characteristics.
-
Ensuring Consistent Performance:
- The use of a vacuum in heat exchangers ensures that the system operates under optimal conditions. This consistency is vital for processes that require stable and predictable thermal performance.
- Whether in industrial heating, HVAC systems, or heat treatment, maintaining a vacuum helps achieve reliable and repeatable results.
-
Extending Equipment Lifespan:
- By preventing issues like water hammer and tube damage, and by enhancing overall efficiency, a vacuum system contributes to the longevity of the heat exchanger.
- Regular maintenance and proper operation, including the use of vacuum breakers, ensure that the heat exchanger remains functional and effective over a longer period.
In summary, the vacuum in a heat exchanger serves multiple critical functions, from preventing mechanical damage and enhancing efficiency to ensuring precise thermal control and extending the equipment's lifespan. Understanding and implementing these principles can significantly improve the performance and reliability of heat exchangers in various applications.
Summary Table:
Purpose of Vacuum in Heat Exchangers | Key Benefits |
---|---|
Preventing Condensate Buildup & Water Hammer | Avoids operational issues and tube damage |
Enhancing Heat Transfer Efficiency | Reduces non-condensable gases for better performance |
Preventing Tube Damage | Protects tubes, reduces maintenance costs |
Controlling Thermal Environment | Ensures precise temperature control in heat treatment |
Ensuring Consistent Performance | Delivers stable and predictable thermal results |
Extending Equipment Lifespan | Improves longevity and reliability |
Learn how a vacuum can enhance your heat exchanger's performance—contact our experts today!