Pyrolysis is a thermal decomposition process used in waste management to convert solid waste materials like plastics, tires, and biomass into valuable products such as syngas, bio-oil, and bio-char. This process occurs in the absence of oxygen, preventing combustion and enabling the breakdown of waste into smaller, usable components. Pyrolysis is particularly effective for handling non-recyclable waste, offering a sustainable solution by transforming waste into energy, fuel, and other useful materials. The process involves several steps, including waste preparation, heating in a reactor, and separation of the resulting products. It is widely used in industrial settings due to its ability to reduce waste volume, recover energy, and produce environmentally friendly byproducts.
Key Points Explained:
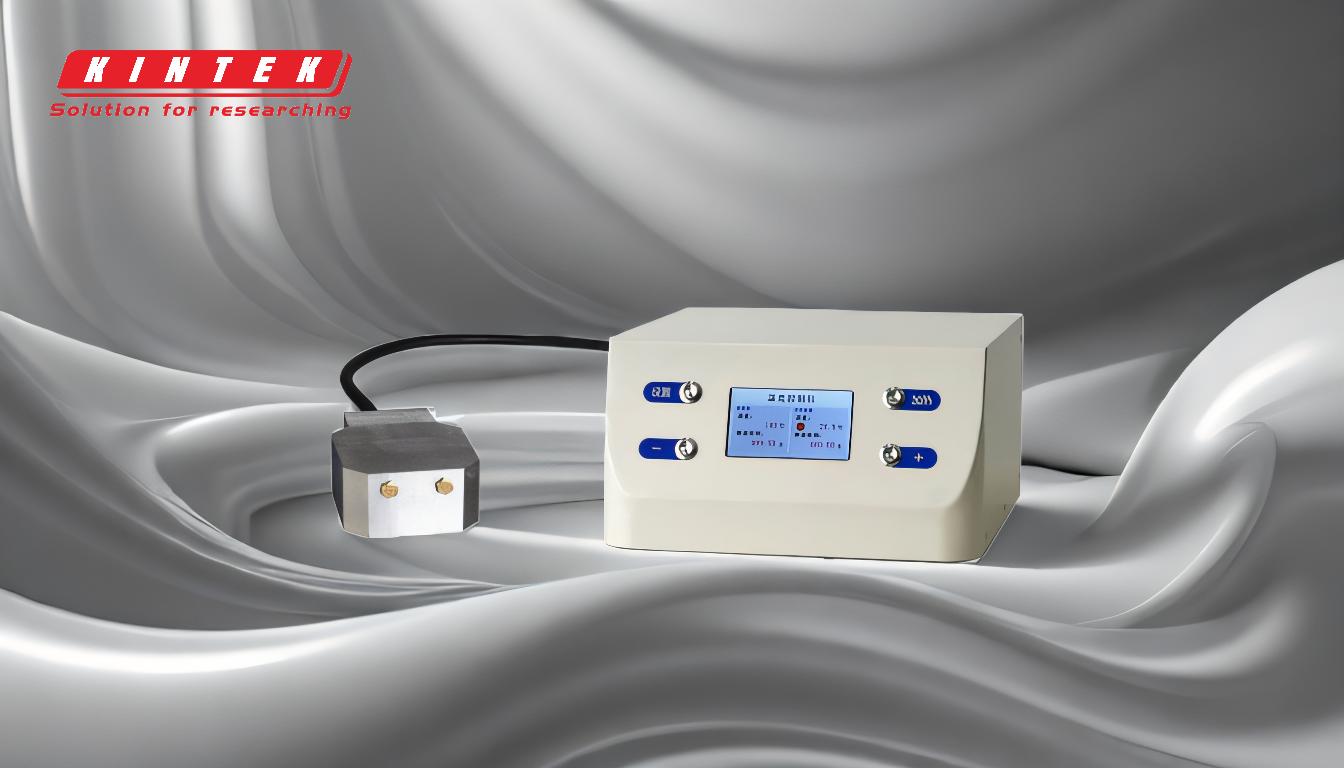
-
Definition and Purpose of Pyrolysis:
- Pyrolysis is a thermal decomposition process that breaks down solid waste materials (e.g., plastics, tires, biomass) in the absence of oxygen.
- The primary purpose is to convert waste into valuable products like syngas, bio-oil, and bio-char, which can be used for energy generation, fuel production, and soil amendment.
-
Key Steps in the Pyrolysis Process:
-
Waste Preparation:
- Waste materials are mechanically prepared and separated to remove non-pyrolyzable components like glass, metals, and inert materials.
- For plastics, this includes shredding, drying, and preprocessing to remove impurities.
-
Pyrolysis Reactor:
- The prepared waste is fed into a pyrolysis reactor, such as a rotary kiln, fluidized bed furnace, or rotary hearth furnace.
- The reactor is heated to temperatures between 400-900°C, causing the waste to decompose into syngas, bio-oil, and bio-char.
-
Product Separation:
- The decomposed materials are separated into gases, liquids, and solids.
- Biochar settles at the bottom, while gases and liquids are condensed into bio-oil and syngas.
-
Product Refinement:
- Bio-oil is distilled and purified for use as fuel or industrial feedstock.
- Syngas is recycled or used as fuel for the pyrolysis process.
-
Waste Preparation:
-
Types of Pyrolysis Reactors:
- Rotary Kilns: Suitable for large-scale operations, these reactors rotate to ensure even heating and decomposition of waste.
- Fluidized Bed Furnaces: Use a bed of hot sand or other materials to evenly distribute heat and improve reaction efficiency.
- Rotary Hearth Furnaces: Ideal for continuous feeding and processing of waste materials.
-
Applications of Pyrolysis Products:
- Syngas: Can be used as a fuel for power generation or further processed into biofuels.
- Bio-oil: Refined for use as transportation fuel or industrial feedstock.
- Bio-char: Used as a soil amendment to improve soil fertility or as a sorbent for environmental remediation.
-
Advantages of Pyrolysis:
- Waste Reduction: Significantly reduces the volume of waste sent to landfills.
- Energy Recovery: Converts waste into usable energy and fuels.
- Environmental Benefits: Reduces greenhouse gas emissions and produces eco-friendly byproducts.
-
Industrial Pyrolysis Process:
- Feed Preparation: Dry biomass or waste is optimally prepared and fed into the reactor.
- Heat Supply: Heat is supplied via a combustion chamber, maintaining low oxygen levels to prevent combustion.
- Product Separation: Biochar settles at the bottom, while gases and liquids are quenched to form bio-oil.
- Gas Recycling: Non-soluble syngas is recycled back to the combustion chamber for energy recovery.
-
Safety and Control Systems:
- Pyrolysis plants are equipped with safety and control systems to ensure efficient and safe operation.
- These systems monitor temperature, pressure, and gas composition to optimize the process and prevent accidents.
-
Environmental Considerations:
- Pyrolysis reduces the environmental impact of waste disposal by converting waste into useful products.
- The process minimizes the release of harmful emissions, especially when compared to traditional incineration methods.
-
Challenges and Limitations:
- High Initial Costs: Setting up pyrolysis plants requires significant capital investment.
- Feedstock Variability: The quality and composition of waste materials can affect the efficiency and output of the process.
- Technical Complexity: Requires skilled operators and advanced control systems to manage the process effectively.
-
Future Prospects:
- Pyrolysis is gaining traction as a sustainable waste management solution, especially for non-recyclable plastics and tires.
- Ongoing research aims to improve the efficiency of pyrolysis reactors and expand the range of usable feedstocks.
In conclusion, pyrolysis is a versatile and environmentally friendly method for disposing of solid waste. By converting waste into valuable products, it addresses both waste management challenges and energy needs, making it a promising solution for a circular economy.
Summary Table:
Aspect | Details |
---|---|
Process | Thermal decomposition of waste in the absence of oxygen. |
Key Products | Syngas, bio-oil, bio-char. |
Applications | Energy generation, fuel production, soil amendment. |
Advantages | Reduces waste volume, recovers energy, minimizes emissions. |
Challenges | High initial costs, feedstock variability, technical complexity. |
Future Prospects | Expanding use for non-recyclable plastics and tires, improving efficiency. |
Discover how pyrolysis can transform your waste management strategy—contact us today to learn more!