Pyrolysis of oil sludge is a thermal decomposition process that converts oil sludge into valuable products such as fuel oil, gas, and solid residues. The process involves several stages, including pretreatment, pyrolysis, and post-treatment. Pretreatment ensures the oil sludge is prepared for efficient pyrolysis by removing debris and achieving uniform dispersion. The pyrolysis reactor, which operates in a closed system with external heat, thermally decomposes the sludge into oil, gas, and char. Post-treatment involves upgrading the pyrolysis oil and treating byproducts to ensure environmental compliance. This process not only addresses oil sludge pollution but also generates economic value by producing usable fuel.
Key Points Explained:
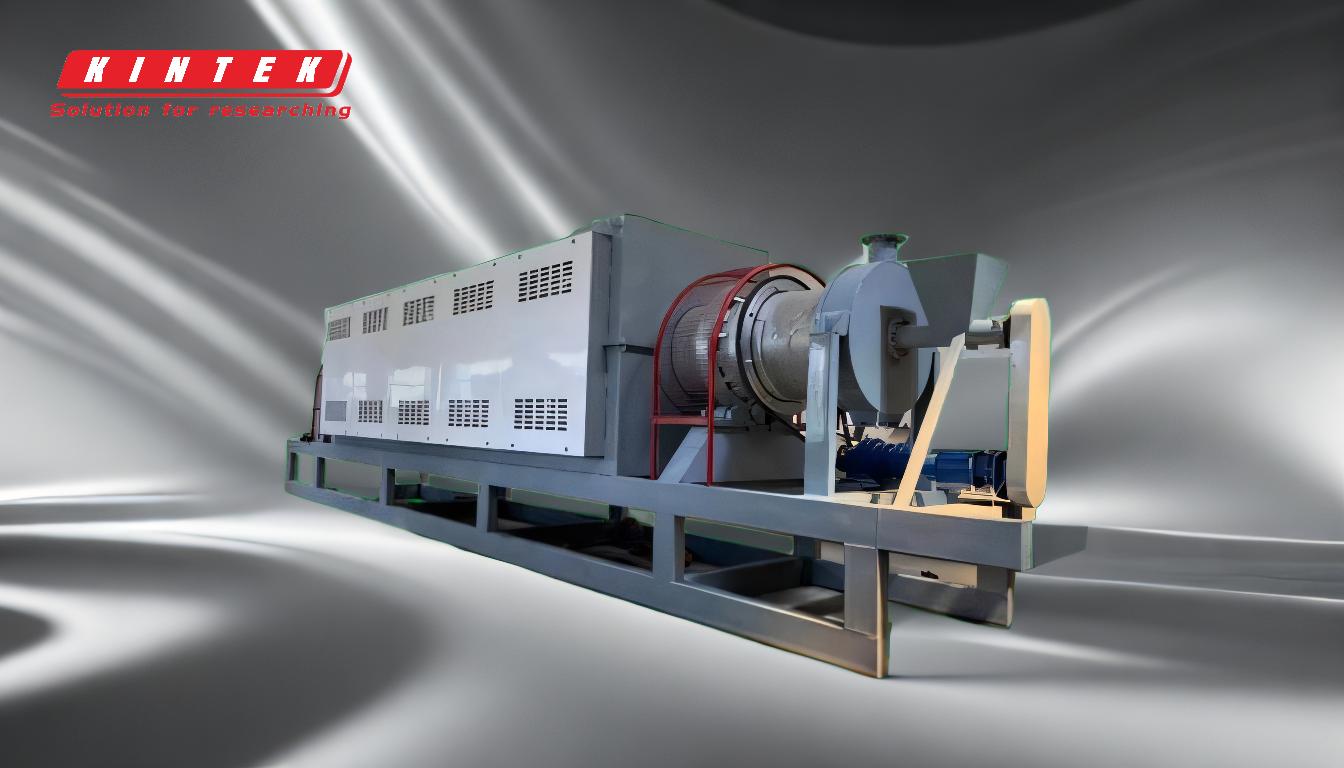
-
Pretreatment of Oil Sludge:
- The first step in the pyrolysis process is pretreatment, where large aggregates of oil sludge are dispersed using a sorting wheel.
- Particles larger than 20mm are separated and collected, while smaller particles pass through sieve holes into a pretreatment tank.
- This step ensures debris removal, fiber crushing, uniform dispersion, and proper storage and transportation of the sludge.
-
Pyrolysis Reactor and Process:
- The pyrolysis reactor is a closed system that relies on external heat to thermally decompose the oil sludge.
- The reactor operates based on thermodynamic principles, breaking down the sludge into oil, gas, and solid residues.
- A drum pyrolysis reactor, for example, uses a rotating drum mechanism to circulate heat internally, making it suitable for slow pyrolysis of biomass.
-
Products of Pyrolysis:
- The primary products of oil sludge pyrolysis are fuel oil, non-condensable gases (e.g., methane, ethane, propane, butane), and biochar.
- These products have various applications, including fuel production, heat, and electricity generation.
-
Post-Treatment and Upgrading:
- Pyrolysis oil undergoes upgrading to remove oxygen or nitrogen, improving its properties for use as fuel.
- The distillation process involves heating the oil in a reactor, converting it into oil gas, and then liquefying it through cooling and condensation.
- Non-liquefiable gases are recycled for heating, and smoke and exhaust gases are treated to ensure no environmental pollution.
-
Environmental and Economic Benefits:
- The oil sludge pyrolysis process addresses environmental pollution by converting hazardous sludge into useful products.
- The production of fuel oil and other byproducts generates economic profit, making the process both environmentally and economically sustainable.
-
Components of an Oil Sludge Pyrolysis Plant:
- A typical plant includes a screw feeder, reactor, buffer chamber, condensers, oil-water separator, water seal device, oil tank, dedusting system, vacuum system, tail gas cleaning system, exhaust gas burner, and thermometer.
- Specialized machines are used to process wastewater and exhaust, ensuring compliance with environmental regulations.
By following these steps, the pyrolysis of oil sludge effectively transforms waste into valuable resources, contributing to both environmental protection and economic gain.
Summary Table:
Stage | Description |
---|---|
Pretreatment | Prepares sludge by removing debris, crushing fibers, and ensuring uniform dispersion. |
Pyrolysis | Thermally decomposes sludge into oil, gas, and char in a closed reactor system. |
Post-Treatment | Upgrades pyrolysis oil and treats byproducts to ensure environmental compliance. |
Products | Fuel oil, non-condensable gases, and biochar with applications in energy production. |
Benefits | Reduces pollution, generates economic value, and produces usable fuel. |
Discover how pyrolysis can transform oil sludge into valuable resources—contact us today for more details!