RF sputtering, a technique widely used in the semiconductor and computer industries, operates at a frequency of 13.56 MHz, which is standardized for industrial applications. This method uses an alternating high-frequency electric field to generate plasma, making it particularly effective for insulating materials. RF sputtering is advantageous for depositing thin films on substrates, as it prevents charge buildup on target materials, which can lead to arcing and quality issues. The process involves two cycles: one where the target material is negatively charged to attract sputtering gas atoms, and another where it is positively charged to eject gas ions and source atoms toward the substrate. This technique is suitable for both conductive and non-conductive materials, though it is most commonly used for dielectric materials. RF sputtering is also used in fabricating optical planar waveguides and photonic microcavities, offering high-quality film deposition at low substrate temperatures.
Key Points Explained:
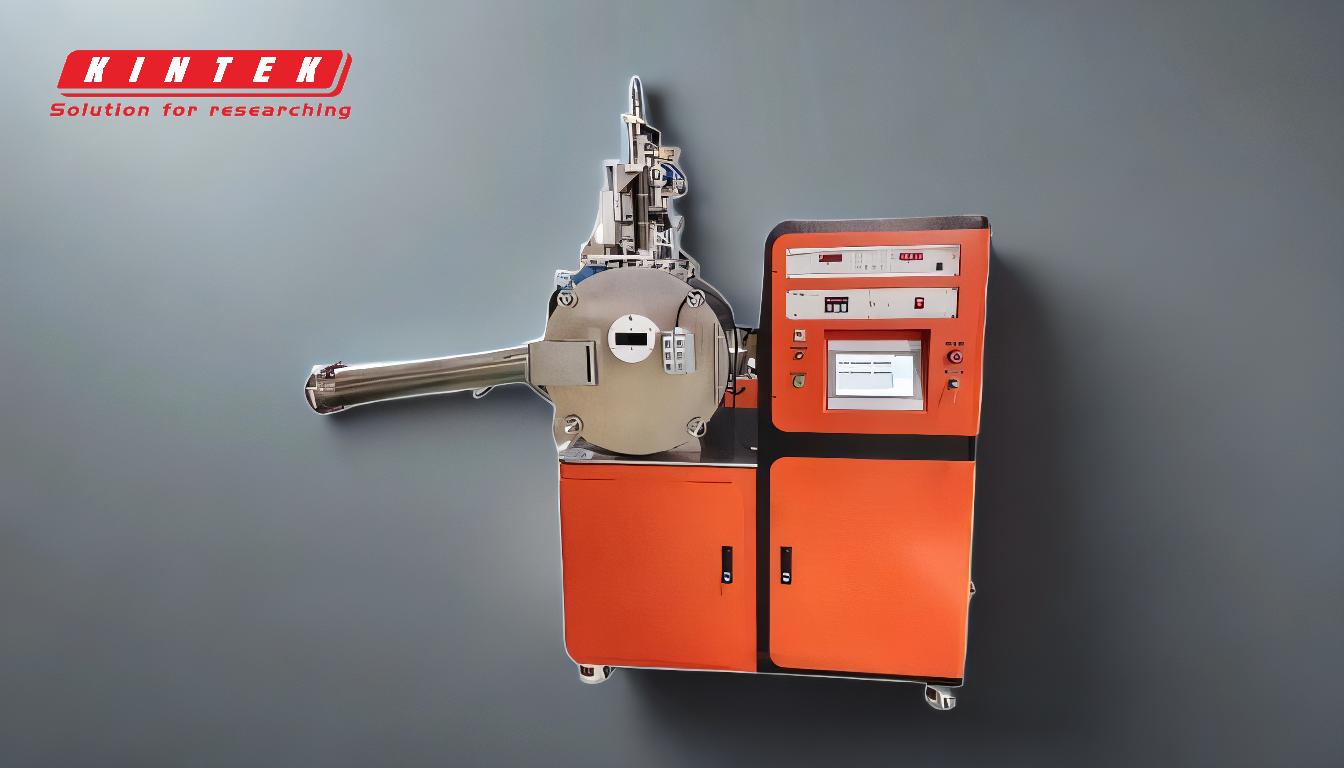
-
Frequency of RF Sputtering:
- RF sputtering operates at a frequency of 13.56 MHz, which is a standard frequency allocated for industrial applications. This frequency is chosen because it effectively generates plasma and prevents charge buildup on insulating target materials.
-
Mechanism of RF Sputtering:
- RF sputtering uses an alternating high-frequency electric field to create plasma in a vacuum environment. The alternating current (AC) power source, typically fixed at 13.56 MHz, alternates the electrical potential of the current, preventing charge accumulation on the target material.
- The process involves two cycles:
- First Cycle: The target material is negatively charged, attracting sputtering gas ions to knock out source atoms.
- Second Cycle: The target is positively charged, ejecting gas ions and source atoms toward the substrate for deposition.
-
Advantages of RF Sputtering:
- Prevents Charge Buildup: By alternating the electrical potential, RF sputtering avoids charge accumulation on insulating materials, which can cause arcing and disrupt the sputtering process.
- Suitable for Insulating Materials: RF sputtering is particularly effective for dielectric materials, making it a preferred method for depositing thin films on insulating targets.
- High-Quality Film Deposition: RF sputtering allows for the deposition of high-quality, homogeneous films at low substrate temperatures, making it ideal for applications in the semiconductor and optical industries.
-
Applications of RF Sputtering:
- Semiconductor Industry: RF sputtering is commonly used to deposit thin films on silicon substrates, such as SiO2 films, which are essential in semiconductor manufacturing.
- Optical and Photonic Devices: RF sputtering is used to fabricate optical planar waveguides and photonic microcavities that operate in the visible and near-infrared (NIR) regions. It is also suitable for creating 1-D photonic crystals and depositing alternating layers of materials with controlled refractive indices.
-
Technical Parameters:
- RF Peak-to-Peak Voltage: Typically 1000 V.
- Electron Density: Ranges from 10^9 to 10^11 cm^-3.
- Chamber Pressure: Operates between 0.5 to 10 mTorr.
- Deposition Rate: Lower compared to DC sputtering, making RF sputtering more suitable for smaller substrate sizes and specialized applications.
-
Comparison with DC Sputtering:
- Deposition Rate: RF sputtering has a lower deposition rate compared to DC sputtering, which makes it less efficient for large-scale production but more suitable for high-precision applications.
- Material Compatibility: RF sputtering is more versatile as it can be used for both conductive and non-conductive materials, whereas DC sputtering is limited to conductive targets.
-
Challenges and Limitations:
- Higher Costs: RF sputtering is generally more expensive due to the complexity of the RF power source and the need for precise control over the sputtering parameters.
- Smaller Substrate Sizes: RF sputtering is typically used for smaller substrates due to the lower deposition rate and higher costs associated with the process.
In summary, RF sputtering is a versatile and precise technique for depositing thin films, particularly on insulating materials. Its ability to prevent charge buildup and deposit high-quality films at low temperatures makes it indispensable in the semiconductor and optical industries. However, its higher costs and lower deposition rates limit its use to specialized applications and smaller substrates.
Summary Table:
Aspect | Details |
---|---|
Frequency | 13.56 MHz (standard for industrial applications) |
Mechanism | Alternating high-frequency electric field generating plasma in a vacuum |
Advantages | Prevents charge buildup, ideal for insulating materials, high-quality films |
Applications | Semiconductor manufacturing, optical waveguides, photonic microcavities |
Technical Parameters | RF Peak-to-Peak Voltage: 1000 V, Chamber Pressure: 0.5-10 mTorr |
Comparison with DC | Lower deposition rate, more versatile for conductive/non-conductive materials |
Limitations | Higher costs, smaller substrate sizes |
Discover how RF sputtering can enhance your thin film processes—contact our experts today!