The rate of deposition in Chemical Vapor Deposition (CVD) is influenced by a variety of factors, including the delivery rate of the precursor, the temperatures of the vaporizer and substrate, and the chemical reactions occurring within the reactor. These factors collectively determine the speed at which a film is deposited onto a substrate, which can vary widely depending on the specific conditions and setup of the CVD process. Understanding these factors is crucial for optimizing the deposition rate to achieve desired film characteristics such as uniformity, quality, and performance.
Key Points Explained:
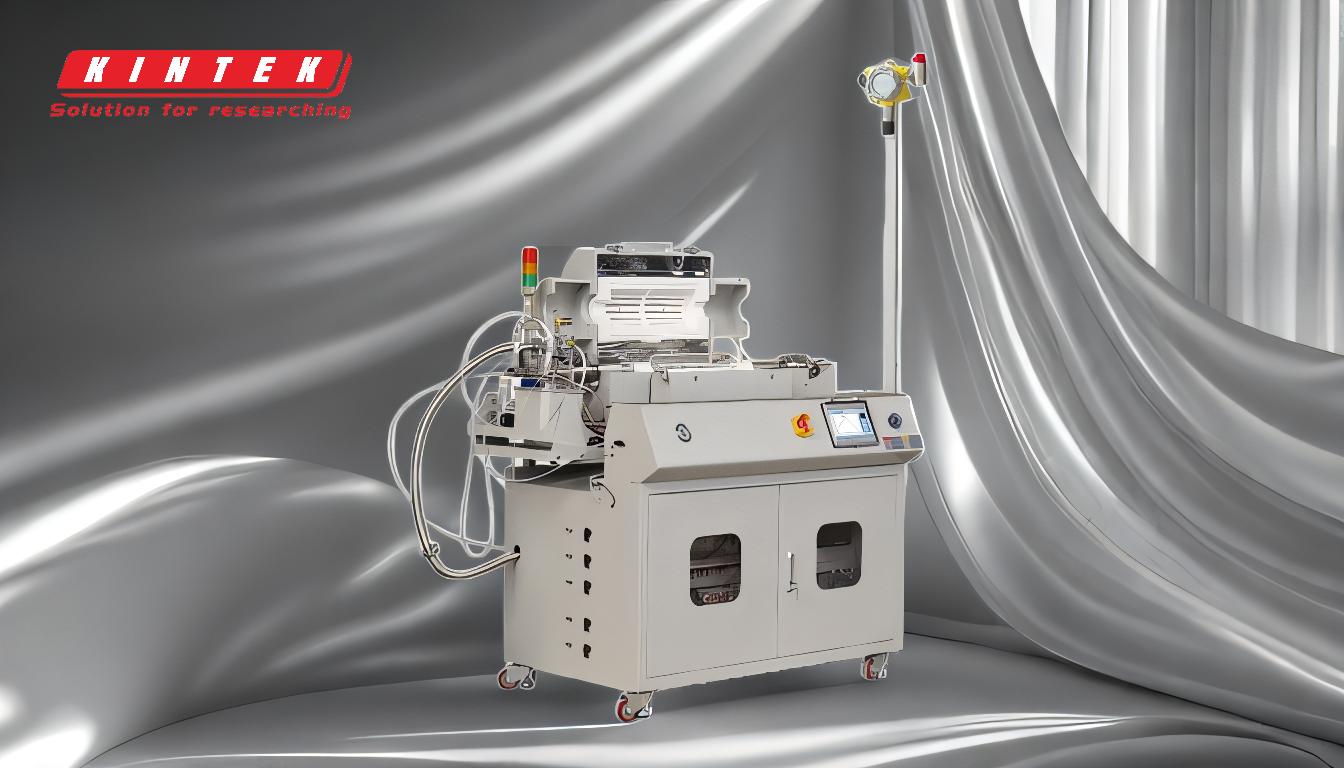
-
Precursor Delivery Rate:
- The rate at which the precursor is delivered to the substrate is a primary factor in determining the deposition rate. A higher delivery rate generally leads to a faster deposition, as more precursor molecules are available to react and form the film.
- The delivery rate is influenced by the design of the CVD system, including the vaporizer and the gas flow system. Precise control over this rate is essential for achieving consistent and predictable deposition rates.
-
Temperature of the Vaporizer and Substrate:
- The temperature of both the vaporizer and the substrate plays a critical role in the deposition process. The vaporizer temperature affects the rate at which the precursor is vaporized and introduced into the reactor.
- The substrate temperature influences the kinetics of the chemical reactions occurring at the surface. Higher temperatures generally increase the reaction rate, leading to faster deposition. However, excessively high temperatures can also lead to undesirable film properties or even damage the substrate.
-
Chemical Reactions in the Reactor:
- The chemical reactions that take place within the CVD reactor are complex and depend on factors such as gas feedstock, gas ratios, reactor pressure, and reaction temperature. These reactions determine the rate at which the film is deposited.
- The reaction temperature is particularly important, as it directly affects the rate of the chemical reactions. Optimal temperature control is necessary to ensure that the reactions proceed at the desired rate without causing defects in the film.
-
System Setup and Reactor Configuration:
- The overall setup of the CVD system, including the reactor configuration, can significantly impact the deposition rate. Factors such as the design of the reactor, the flow dynamics of the gases, and the placement of the substrate within the reactor all play a role.
- The reactor pressure and gas partial pressures are also critical. These parameters influence the concentration of reactive species at the substrate surface, which in turn affects the deposition rate.
-
Substrate Characteristics:
- The size, geometry, and chemical composition of the substrate can influence the deposition rate. For example, a larger substrate may require a longer time to achieve uniform deposition, while a substrate with a complex shape may present challenges in maintaining consistent deposition rates across its surface.
- The substrate temperature, as mentioned earlier, is also a key factor. It must be carefully controlled to ensure that the deposition rate is consistent and that the resulting film has the desired properties.
-
Economic and Production Considerations:
- The economics of production, including the cost of precursors, energy consumption, and the efficiency of the CVD process, can also influence the deposition rate. In some cases, a slower deposition rate may be chosen to reduce costs or to achieve higher film quality.
- The purity of the target material and the overall efficiency of the CVD process are also important considerations. Higher purity materials and more efficient processes can lead to faster deposition rates and better film quality.
In summary, the rate of deposition in CVD is a complex interplay of various factors, including precursor delivery rate, temperature control, chemical reactions, system setup, substrate characteristics, and economic considerations. Understanding and optimizing these factors is essential for achieving the desired deposition rate and film properties in CVD processes.
Summary Table:
Factor | Impact on Deposition Rate |
---|---|
Precursor Delivery Rate | Higher delivery rates increase deposition speed; controlled flow ensures consistency. |
Vaporizer & Substrate Temperature | Higher temperatures accelerate reactions; excessive heat may damage the substrate. |
Chemical Reactions in Reactor | Reaction temperature and gas ratios determine reaction speed and film quality. |
System Setup & Reactor Design | Reactor pressure, gas flow, and configuration influence reactive species concentration. |
Substrate Characteristics | Size, shape, and composition affect uniformity and deposition speed. |
Economic & Production Factors | Cost, energy efficiency, and material purity influence deposition rate and film quality. |
Ready to optimize your CVD process? Contact our experts today for tailored solutions!