The rate of Physical Vapor Deposition (PVD) depends on several factors, including the type of PVD technique, the properties of the target material, process parameters (such as power, temperature, and target-substrate distance), and the specific application requirements. Typical PVD deposition rates range from 1 to 100 angstroms per second (A/s), with common coating rates falling between 50 and 500 micrometers per hour (µm/hr). These rates are influenced by the size of the erosion zone, plasma characteristics, and process conditions like laser power and feed rates in laser-based PVD methods. Understanding and controlling these factors is essential for achieving uniform film thickness and high-quality coatings.
Key Points Explained:
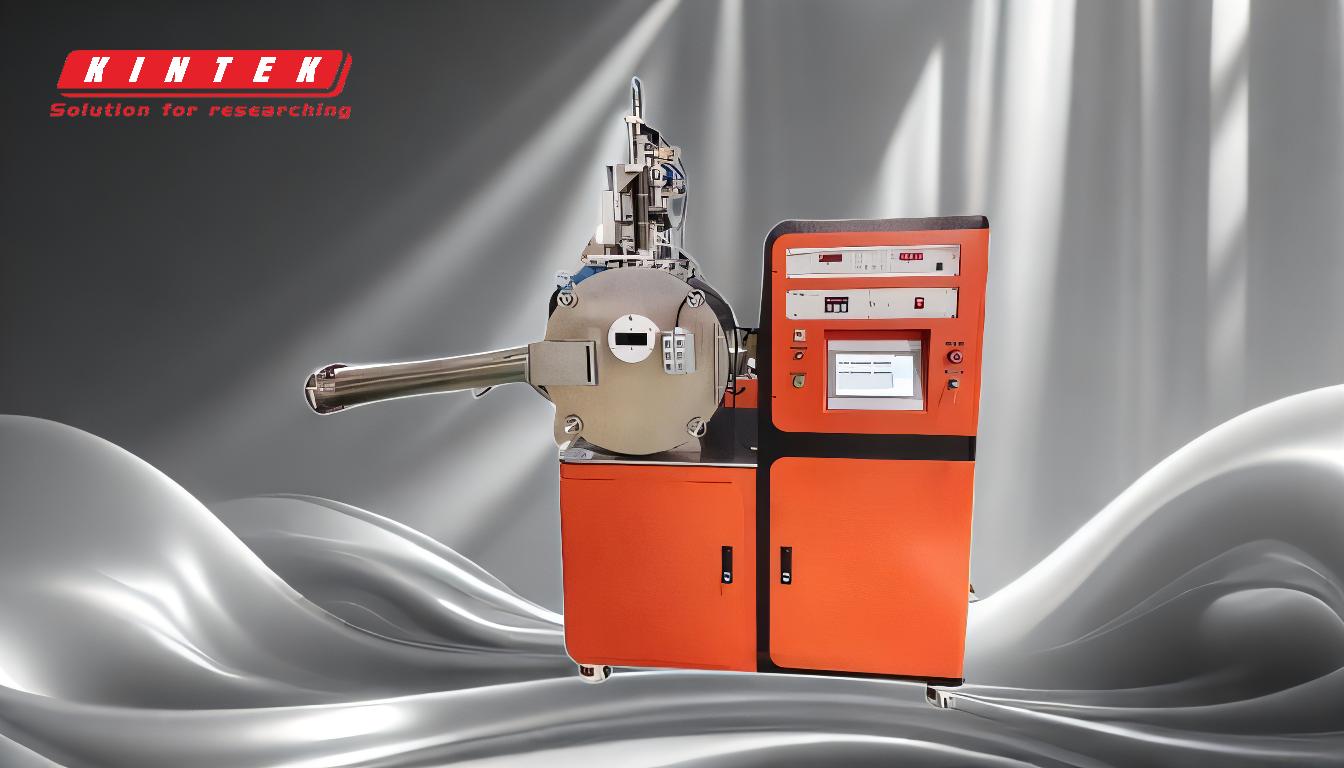
-
Definition of Deposition Rate:
- The deposition rate refers to the speed at which a thin film is deposited onto a substrate during the PVD process.
- It is a critical parameter that affects the uniformity, thickness, and overall quality of the coating.
-
Typical Deposition Rates:
- PVD deposition rates typically range from 1 to 100 angstroms per second (A/s).
- In terms of coating rates, common values are between 50 and 500 micrometers per hour (µm/hr), depending on the specific PVD technique and application.
-
Factors Influencing Deposition Rate:
- Target Material Properties: The physical and chemical properties of the target material, such as its sputtering yield and melting point, directly impact the deposition rate.
-
Process Parameters:
- Power and Temperature: Higher power and temperature generally increase the deposition rate.
- Target-Substrate Distance: A shorter distance between the target and substrate typically results in a higher deposition rate and better thickness uniformity.
- Erosion Zone Size: A larger erosion zone on the target material can enhance the deposition rate and improve coating uniformity.
- Plasma Characteristics: Factors like plasma temperature, composition, and density play a significant role in determining the deposition rate in plasma-based PVD processes.
- Laser Parameters (for laser-based PVD): In methods like laser cladding, the deposition rate is influenced by laser power, power feed rates, and traverse speed.
-
Importance of Controlling Deposition Rate:
- Controlling the deposition rate is essential for achieving consistent film thickness and uniformity, which are critical for the performance of the final product.
- Variations in the deposition rate can lead to defects, such as uneven coatings or poor adhesion, affecting the functionality and durability of the coating.
-
Impact of Deposition Method:
- The specific PVD technique used (e.g., sputtering, evaporation, or laser-based methods) significantly influences the deposition rate and the properties of the resulting coating.
- Even when using the same target material, different deposition methods can produce coatings with distinct performance characteristics.
-
Monitoring and Optimization:
- Monitoring the deposition rate and other process parameters (e.g., elemental composition in the chamber) is crucial to ensure the desired material properties and to detect contamination.
- Optimizing process conditions, such as adjusting power, temperature, and target-substrate distance, can help achieve the desired deposition rate and coating quality.
By understanding these factors and their interactions, equipment and consumable purchasers can make informed decisions about selecting the appropriate PVD system and process parameters to meet their specific application requirements.
Summary Table:
Factor | Impact on Deposition Rate |
---|---|
Target Material Properties | Sputtering yield, melting point, and other properties directly affect deposition rate. |
Process Parameters | Higher power, temperature, and shorter target-substrate distance increase deposition rate. |
Erosion Zone Size | Larger erosion zones enhance deposition rate and improve coating uniformity. |
Plasma Characteristics | Plasma temperature, composition, and density influence deposition rate in plasma-based PVD. |
Laser Parameters | Laser power, feed rates, and traverse speed affect deposition rate in laser-based PVD. |
Deposition Method | Different PVD techniques (e.g., sputtering, evaporation) yield varying deposition rates. |
Optimize your PVD process for superior coatings—contact our experts today!