Activated carbon regeneration temperature typically ranges between 220°C and 370°C, depending on the specific process and conditions. The regeneration process involves heating the carbon to remove adsorbed contaminants and restore its adsorption capacity. The lower temperature range (220–240°C) is often associated with the initial phase of regeneration, while higher temperatures (320–370°C) are used for more thorough regeneration. These temperatures ensure the effective desorption of volatile organic compounds (VOCs) and other contaminants without damaging the carbon structure.
Key Points Explained:
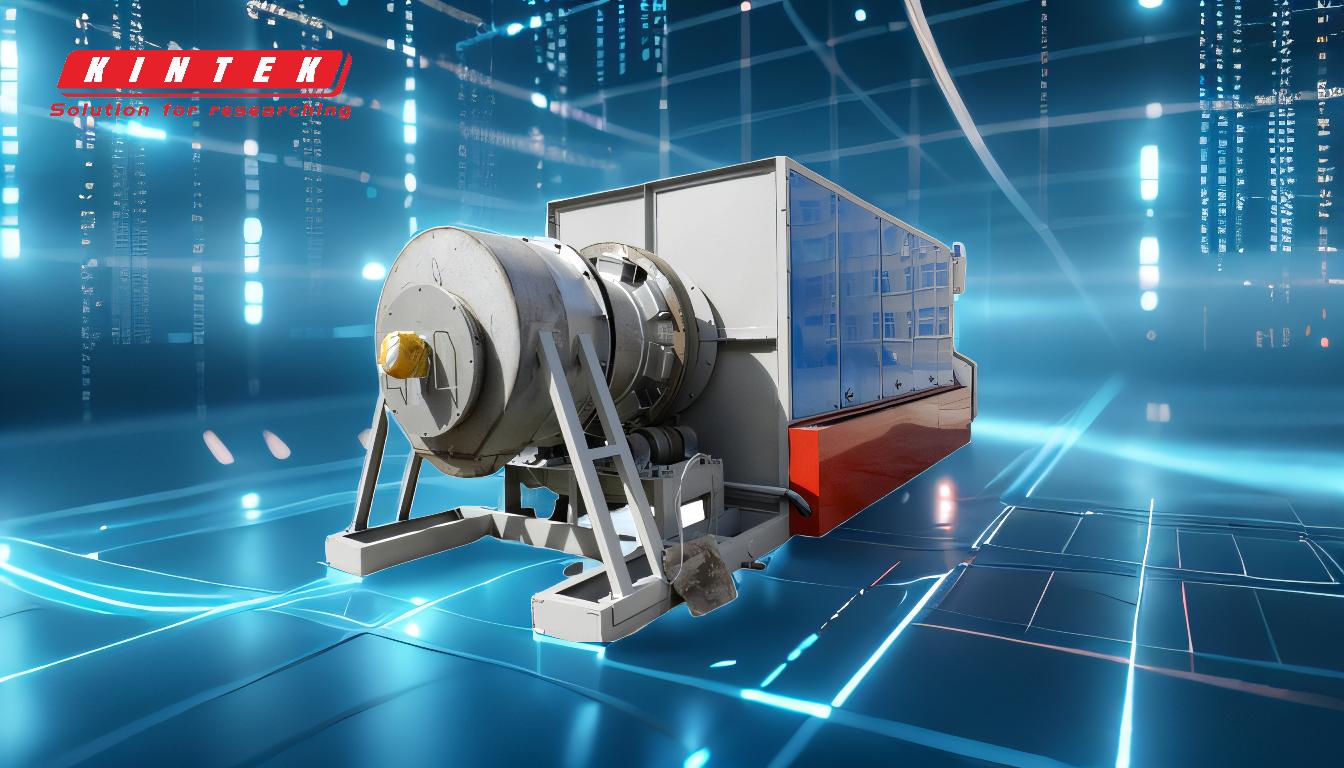
-
Regeneration Temperature Range:
- The regeneration temperature for activated carbon typically falls between 220°C and 370°C.
- This range is divided into two phases:
- Initial Phase (220–240°C): This lower temperature range is used to initiate the desorption of lighter contaminants and volatile organic compounds (VOCs).
- Advanced Phase (320–370°C): Higher temperatures are applied to remove more stubborn or heavier contaminants, ensuring a thorough regeneration process.
-
Purpose of Temperature Control:
- Desorption of Contaminants: Heating the activated carbon to these temperatures helps break the bonds between the carbon surface and adsorbed molecules, allowing contaminants to be released.
- Preservation of Carbon Structure: The temperature range is carefully chosen to avoid thermal degradation of the activated carbon, which could reduce its adsorption capacity.
-
Factors Influencing Regeneration Temperature:
- Type of Contaminants: Heavier or more complex contaminants may require higher temperatures for effective removal.
- Activated Carbon Properties: The specific surface area, pore structure, and thermal stability of the carbon can influence the optimal regeneration temperature.
- Regeneration Method: Catalytic regeneration, thermal regeneration, or other methods may have different temperature requirements.
-
Applications of Regeneration:
- Industrial Air Purification: Used in systems where activated carbon filters are employed to capture VOCs and other pollutants.
- Water Treatment: Regenerated carbon can be reused in water purification systems to remove organic contaminants.
- Environmental Remediation: Activated carbon regeneration is critical in processes like soil and groundwater cleanup.
-
Importance of Temperature Precision:
- Efficiency: Maintaining the correct temperature ensures maximum desorption of contaminants while minimizing energy consumption.
- Safety: Excessive temperatures can lead to carbon degradation or even combustion, while insufficient temperatures may leave contaminants adsorbed.
By understanding the regeneration temperature range and its implications, equipment and consumable purchasers can make informed decisions about the selection and maintenance of activated carbon systems, ensuring optimal performance and cost-effectiveness.
Summary Table:
Aspect | Details |
---|---|
Temperature Range | 220°C–370°C (divided into initial phase: 220–240°C, advanced phase: 320–370°C) |
Purpose | Desorb contaminants, preserve carbon structure |
Key Factors | Type of contaminants, carbon properties, regeneration method |
Applications | Industrial air purification, water treatment, environmental remediation |
Importance of Precision | Ensures efficiency, prevents carbon degradation, and maintains safety |
Optimize your activated carbon system today—contact our experts for tailored solutions!