The RF frequency used in the sputtering process is typically 13.56 MHz. This frequency is chosen because it falls within the Industrial, Scientific, and Medical (ISM) radio bands, which are internationally recognized for non-communication purposes. The RF sputtering process involves creating a plasma in a vacuum chamber using an inert gas like argon. The RF power source ionizes the gas atoms, which then strike the target material, causing it to sputter and deposit a thin film on the substrate. The process includes positive and negative cycles to prevent ion buildup on insulating targets, ensuring a consistent and efficient sputtering process.
Key Points Explained:
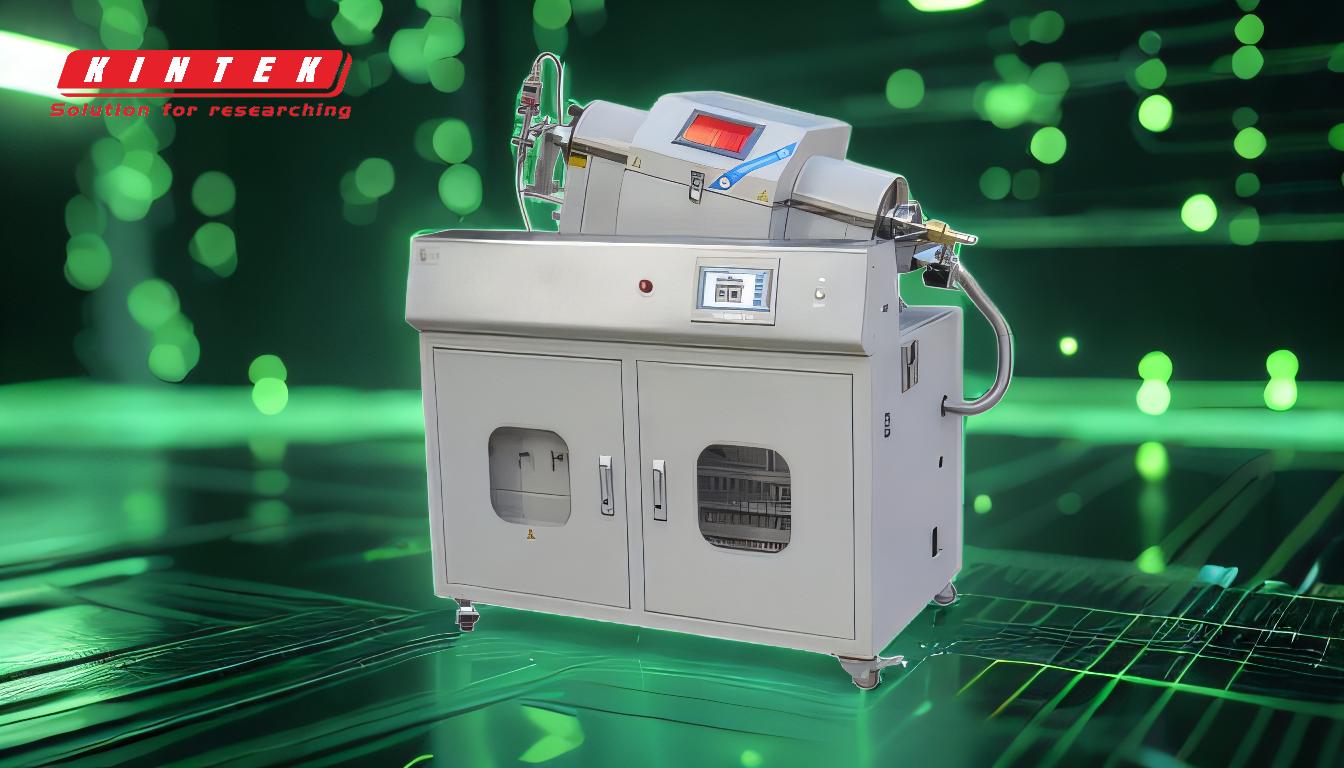
-
RF Frequency in Sputtering:
- The RF frequency used in sputtering is typically 13.56 MHz. This frequency is part of the ISM band, which is reserved for industrial, scientific, and medical applications. The choice of this frequency ensures minimal interference with communication systems and allows for efficient ionization of the gas in the sputtering chamber.
-
Role of Argon in Sputtering:
- Argon is the most commonly used gas in the sputtering process due to its inert nature and relatively low cost. When introduced into the vacuum chamber, argon atoms are ionized by the RF power source, creating a plasma. These ions then bombard the target material, causing it to sputter and deposit onto the substrate.
-
RF Sputtering Process:
- The RF sputtering process begins with placing the target material, substrate, and RF electrodes in a vacuum chamber. An inert gas, such as argon, is introduced, and the RF power source is activated. The RF waves ionize the gas atoms, which then strike the target material, breaking it into small pieces that travel to the substrate and form a thin film.
-
Positive and Negative Cycles:
- The RF sputtering process involves two cycles: positive and negative. In the positive cycle, electrons are attracted to the cathode, creating a negative bias. In the negative cycle, ion bombardment continues. This alternating cycle prevents ion buildup on insulating targets by avoiding a constant negative voltage on the cathode, ensuring a stable and efficient sputtering process.
-
Magnetron Sputtering and Target Utilization:
- In magnetron sputtering, a ring magnetic field forces secondary electrons to move around it, creating a region with the highest plasma density. This area emits a strong light blue glow during sputtering, forming a halo. The target in this region is heavily bombarded by ions, leading to the formation of a ring-shaped groove. Once this groove penetrates the target, the entire target is scrapped, resulting in low target utilization rates, typically below 40%.
By understanding these key points, one can appreciate the complexity and precision required in the RF sputtering process, particularly in the selection of the RF frequency and the role of argon in creating a stable plasma for efficient thin film deposition.
Summary Table:
Key Aspect | Details |
---|---|
RF Frequency | 13.56 MHz, part of the ISM band for minimal interference and efficient ionization. |
Role of Argon | Inert gas used to create plasma, ionized by RF power for target bombardment. |
RF Sputtering Process | Involves vacuum chamber, RF electrodes, and alternating positive/negative cycles. |
Target Utilization | Magnetron sputtering leads to low utilization rates, typically below 40%. |
Unlock the potential of RF sputtering for your applications—contact our experts today for tailored solutions!