RF sputtering, or Radio Frequency sputtering, is a technique used to deposit thin films, particularly for non-conductive (dielectric) materials, in industries such as semiconductors and computing. It operates by alternating the electrical potential at radio frequencies (typically 13.56 MHz) in a vacuum environment, which prevents charge buildup on the target material. This process involves two cycles: the positive cycle, where electrons are attracted to the target, creating a negative bias, and the negative cycle, where ion bombardment ejects target atoms toward the substrate. RF sputtering is essential for materials that cannot be processed using DC sputtering due to surface charging issues.
Key Points Explained:
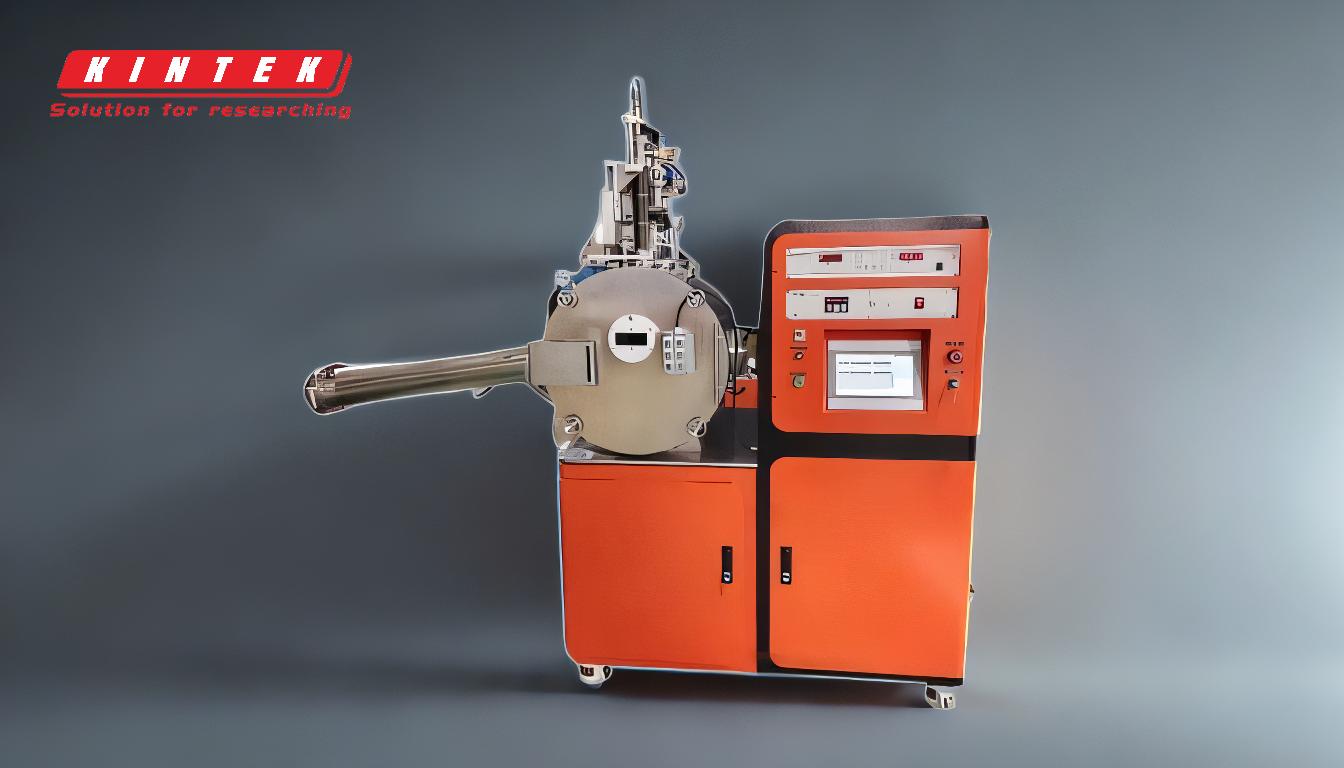
-
Definition and Purpose of RF Sputtering:
- RF sputtering is a thin-film deposition technique used primarily for non-conductive (dielectric) materials.
- It is widely employed in the semiconductor and computer industries to create high-quality thin films.
- The technique overcomes the limitations of DC sputtering, which is unsuitable for non-conductive materials due to surface charging.
-
How RF Sputtering Works:
- Alternating Current (AC) Power Source: RF sputtering uses an AC power source, typically fixed at 13.56 MHz, to alternate the electrical potential.
-
Two Cycles:
- Positive Cycle: The target material acts as an anode, attracting electrons and creating a negative bias.
- Negative Cycle: The target becomes positively charged, ejecting gas ions and target atoms toward the substrate for deposition.
- Prevention of Charge Buildup: The alternating potential ensures that charge buildup on the target surface is minimized, preventing arcing and maintaining process stability.
-
Key Parameters and Conditions:
- Frequency: 13.56 MHz is the standard frequency used.
- Voltage: The RF peak-to-peak voltage is typically around 1000 V.
- Electron Density: Ranges from 10^9 to 10^11 Cm^-3.
- Chamber Pressure: Maintained between 0.5 to 10 mTorr.
- Material Suitability: RF sputtering is suitable for both conductive and non-conductive materials but is most commonly used for dielectric materials.
-
Advantages of RF Sputtering:
- Versatility: Can deposit both conductive and non-conductive materials.
- Quality Control: Prevents charge buildup, reducing the risk of arcing and ensuring high-quality thin films.
- Stability: The alternating potential ensures a stable sputtering process, even for insulating materials.
-
Limitations of RF Sputtering:
- Deposition Rate: Lower compared to DC sputtering.
- Cost: Higher operational costs due to the complexity of the RF power source and matching network.
- Substrate Size: Typically used for smaller substrates due to higher costs and technical constraints.
-
Applications of RF Sputtering:
- Semiconductor Industry: Used for depositing thin films of dielectric materials in semiconductor devices.
- Computing Industry: Essential for creating thin films in computer components.
- Research and Development: Utilized in laboratories for developing new materials and coatings.
-
Comparison with Other Sputtering Techniques:
- DC Sputtering: More cost-effective for conductive materials but unsuitable for non-conductive materials due to surface charging.
- Magnetron Sputtering: Offers higher deposition rates but may not be suitable for all materials.
- Reactive Sputtering: Used for depositing compound films but requires precise control of reactive gases.
In summary, RF sputtering is a critical technique for depositing thin films of non-conductive materials, offering advantages in quality control and versatility. However, it comes with limitations such as lower deposition rates and higher costs, making it most suitable for specific applications in the semiconductor and computing industries.
Summary Table:
Aspect | Details |
---|---|
Definition | Thin-film deposition technique for non-conductive (dielectric) materials. |
Frequency | 13.56 MHz |
Voltage | ~1000 V peak-to-peak |
Chamber Pressure | 0.5 to 10 mTorr |
Material Suitability | Conductive and non-conductive materials, primarily dielectric. |
Advantages | Versatility, quality control, and process stability. |
Limitations | Lower deposition rate, higher cost, and smaller substrate size. |
Applications | Semiconductor devices, computer components, and R&D. |
Discover how RF sputtering can enhance your thin-film processes—contact our experts today!