The magnetron plays a critical role in the sputtering process by generating and controlling plasma within the vacuum chamber. It uses a magnetic field to ionize the target material, causing it to sputter and deposit onto the substrate. The magnetron enhances the efficiency of the sputtering process by trapping electrons near the target surface, increasing plasma density, and improving the uniformity of film deposition. It also allows for precise control over the deposition rate and thickness by manipulating the path of sputtered atoms. Two main types of magnetrons, DC and RF, are used depending on the desired deposition rate, film quality, and material compatibility.
Key Points Explained:
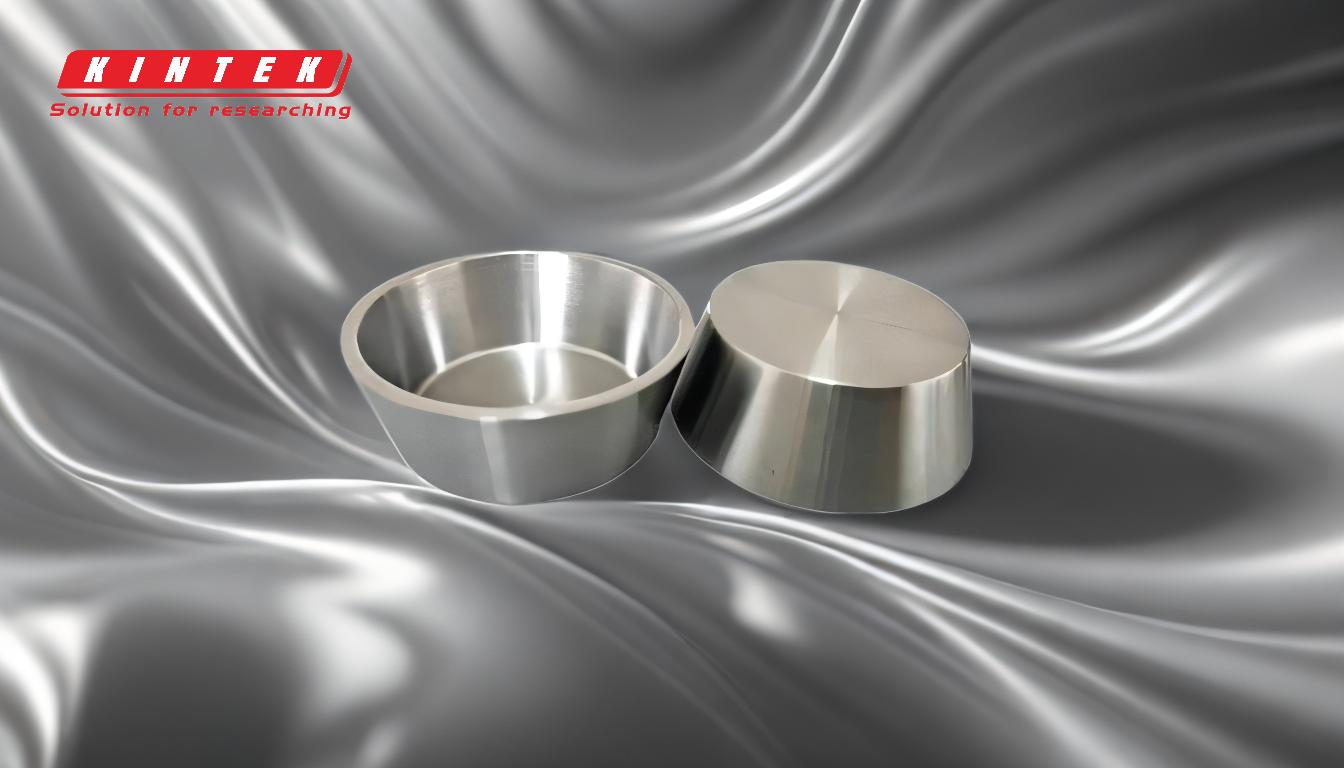
-
Plasma Generation and Ionization:
- The magnetron generates plasma inside the vacuum chamber using a magnetic field.
- This plasma ionizes the target material, causing it to sputter or vaporize.
- The ionized material then deposits onto the substrate, forming a thin film.
-
Types of Magnetrons:
- DC Magnetrons: Use a direct current power supply. These are typically chosen for their simplicity and effectiveness in depositing conductive materials.
- RF Magnetrons: Use a high-frequency radio frequency power supply. These are preferred for depositing insulating materials and achieving higher film quality.
-
Control of Sputtered Atoms:
- Magnetrons control the path of displaced atoms that would otherwise fly randomly around the vacuum chamber.
- High-energy magnetic fields are generated and manipulated to collect and contain the plasma around the substrate.
- This ensures that the ejected atoms travel in predictable paths to the substrate, allowing for controlled film deposition rates and thickness.
-
Enhanced Sputtering Efficiency:
- In RF sputtering, the magnetron creates a magnetic field that forms a boundary tunnel, trapping electrons near the target surface.
- This increases the sputtering yield at lower pressures by maintaining higher plasma currents and reducing collisions between sputtered atoms and chamber molecules.
- It also enhances the uniformity of layer deposition.
-
Magnetic Field Configuration:
- A permanent magnet or electromagnet is added to create lines of magnetic flux parallel to the target surface.
- This magnetic field concentrates and intensifies the plasma near the target surface by trapping electrons.
- The result is enhanced ion bombardment and a higher sputtering rate without increasing the operating pressure.
-
Benefits of Using Magnetrons:
- Higher Deposition Rates: The magnetron configuration allows for higher sputtering rates, making the process more efficient.
- Improved Film Quality: The controlled environment and enhanced plasma density lead to better film quality and uniformity.
- Material Compatibility: The choice between DC and RF magnetrons allows for compatibility with a wide range of materials, including both conductive and insulating types.
-
Operational Advantages:
- Lower Operating Pressure: The ability to maintain higher plasma currents at lower pressures reduces the likelihood of collisions, improving the overall efficiency of the sputtering process.
- Precision and Control: The ability to manipulate the magnetic fields provides precise control over the deposition process, ensuring consistent and repeatable results.
In summary, the magnetron is a crucial component in the sputtering process, providing the necessary plasma generation, control, and efficiency to achieve high-quality thin film deposition. Its design and functionality make it adaptable to various materials and deposition requirements, ensuring optimal performance in both DC and RF sputtering applications.
Summary Table:
Aspect | Details |
---|---|
Plasma Generation | Generates plasma using a magnetic field to ionize the target material. |
Types of Magnetrons | DC (for conductive materials) and RF (for insulating materials). |
Control of Atoms | Manipulates sputtered atoms' paths for precise deposition rates and thickness. |
Enhanced Efficiency | Traps electrons, increases plasma density, and improves deposition uniformity. |
Operational Benefits | Higher deposition rates, improved film quality, and material compatibility. |
Optimize your sputtering process with advanced magnetron technology—contact our experts today!