Zirconia undergoes significant shrinkage during the sintering process, a critical step in transforming it into a dense, strong, and durable ceramic material. This shrinkage is primarily due to the reduction of porosity and the increase in particle density as the material is subjected to high temperatures (and sometimes pressure). The transformation occurs as zirconia transitions from a monoclinic to a polytetragonal crystalline structure at temperatures between 1,100°C and 1,200°C. The shrinkage is a key factor in achieving the final properties of zirconia, such as enhanced strength, translucency, and structural integrity, making it suitable for applications like dental restorations.
Key Points Explained:
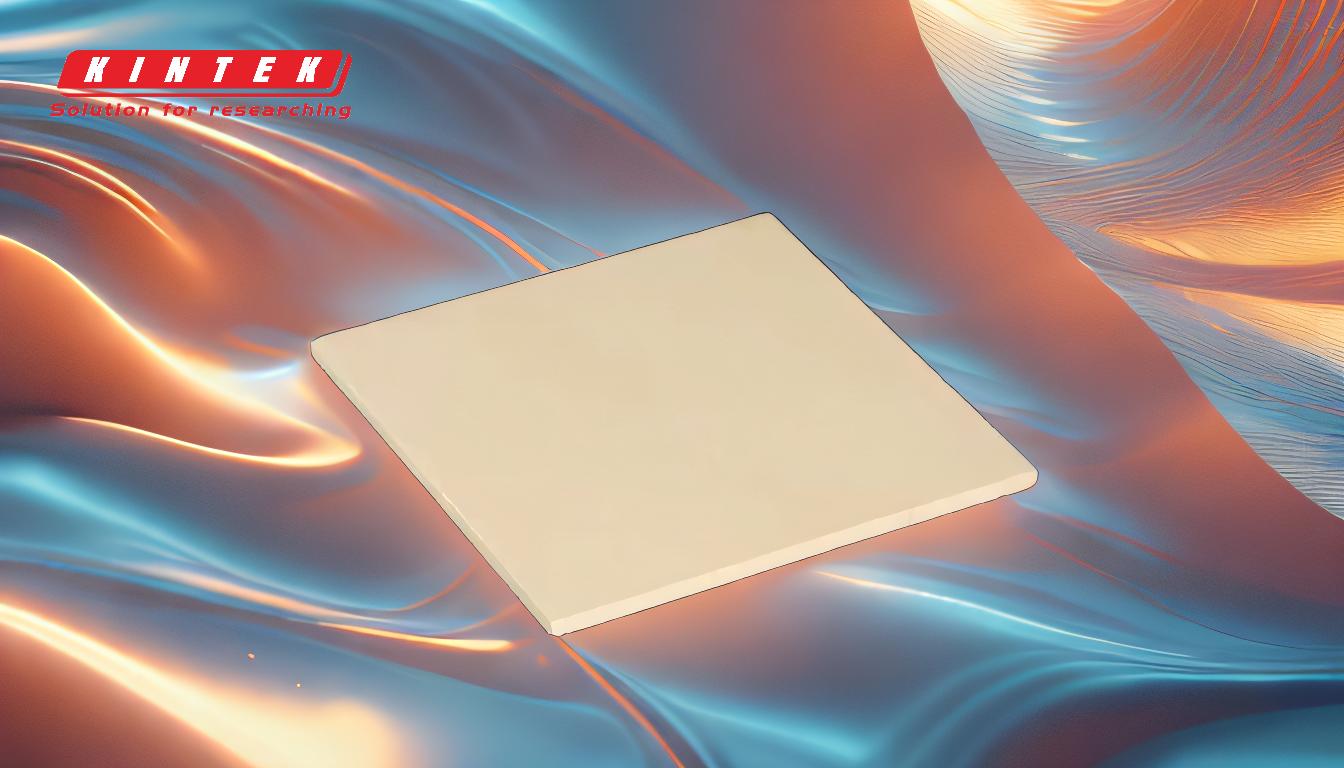
-
Shrinkage During Sintering:
- Zirconia undergoes significant shrinkage during sintering, a process that involves heating the material to high temperatures (typically between 1,100°C and 1,200°C) and sometimes applying pressure.
- This shrinkage is a result of the reduction in porosity and the increase in particle density, which leads to a more compact and dense material.
-
Transformation of Crystalline Structure:
- During sintering, zirconia transitions from a monoclinic crystalline structure to a polytetragonal crystalline state.
- This transformation is critical for enhancing the material's mechanical properties, such as strength and hardness, and is accompanied by significant shrinkage.
-
Impact on Material Properties:
- The shrinkage process improves the density of zirconia, which in turn enhances its strength, durability, and structural integrity.
- The reduction in porosity also contributes to the material's translucency, making it more suitable for aesthetic applications like dental restorations.
-
Role of Temperature and Pressure:
- The sintering process involves heating zirconia to high temperatures, where the material reaches its transition temperature, allowing the glass phase to flow and incorporate the powder structure.
- In some cases, pressure is also applied to further reduce porosity and enhance the material's density and strength.
-
Practical Implications for Applications:
- Understanding the shrinkage behavior of zirconia is crucial for manufacturers and users, particularly in applications like dental restorations, where precise dimensions and material properties are essential.
- The shrinkage must be accounted for during the design and manufacturing process to ensure the final product meets the required specifications.
In summary, the shrinkage of zirconia during sintering is a fundamental aspect of its processing, leading to improved density, strength, and durability. This process is essential for achieving the desired properties in zirconia-based products, particularly in high-precision applications like dental restorations.
Summary Table:
Key Aspect | Details |
---|---|
Shrinkage During Sintering | Reduction in porosity and increase in particle density at 1,100°C–1,200°C. |
Crystalline Transformation | Monoclinic to polytetragonal structure, enhancing strength and hardness. |
Material Properties | Improved density, strength, durability, and translucency. |
Temperature & Pressure Role | High temperatures and optional pressure reduce porosity and enhance density. |
Applications | Critical for dental restorations and high-precision manufacturing. |
Discover how zirconia sintering can optimize your product performance—contact our experts today!