The sintering temperature for zirconia typically ranges between 1400°C and 1600°C, with most materials achieving optimal physical, mechanical, and esthetic properties at around 1500°C to 1550°C. This high-temperature process is essential for transforming zirconia into a dense, durable material with close to 99% of its theoretical maximum density. The transformation from monoclinic to polytetragonal structure occurs at lower temperatures (1100°C to 1200°C), but the final sintering process requires specialized high-temperature furnaces. Sintering at temperatures slightly above or below the optimal range can significantly affect the material's strength, with deviations as small as 150°C leading to reduced performance.
Key Points Explained:
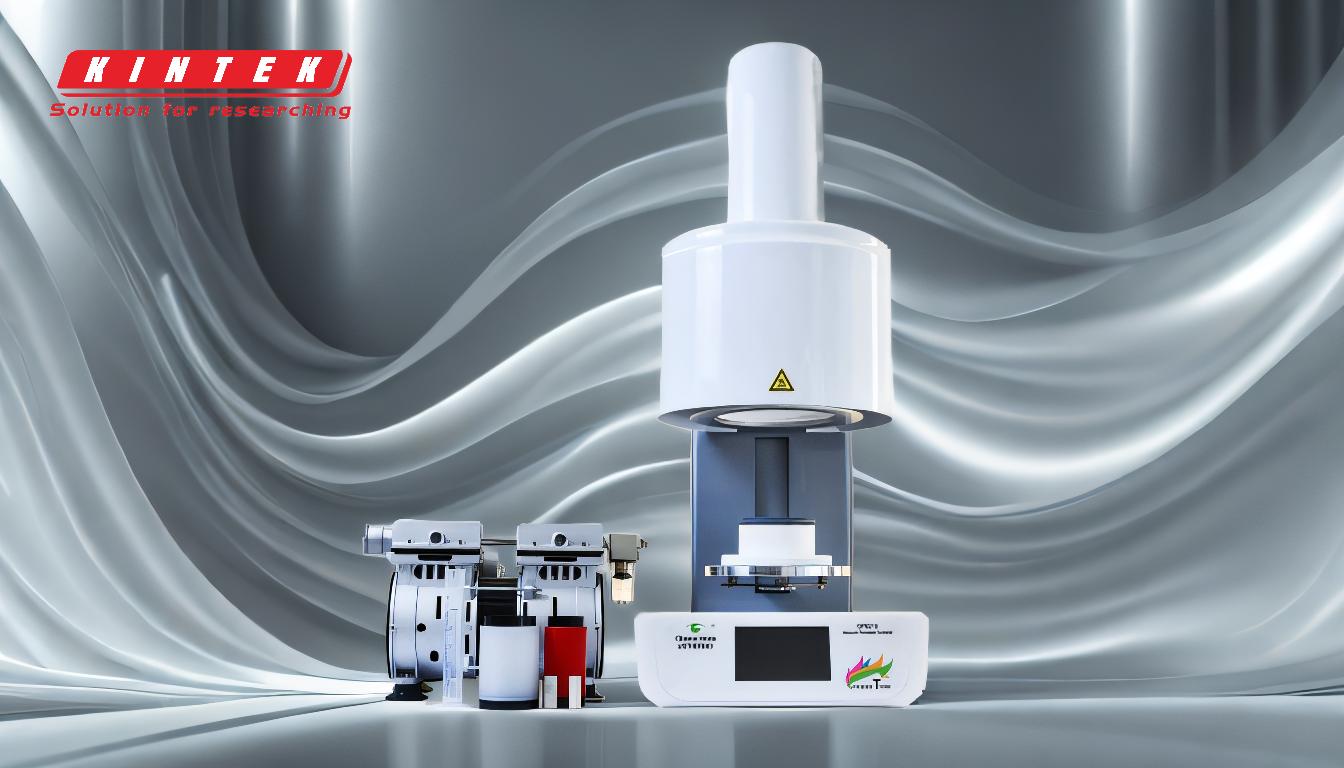
-
Sintering Temperature Range:
- The sintering temperature for zirconia generally falls between 1400°C and 1600°C.
- This range is necessary to achieve the desired hardness, density, and strength in the final product.
- Most manufacturers recommend sintering at 1500°C to 1550°C for optimal results.
-
Optimal Temperature for Physical and Mechanical Properties:
- Yttria partially-stabilized zirconia achieves its ideal properties at approximately 1550°C.
- Sintering at this temperature ensures maximum strength, with studies showing a peak strength of around 1280 MPa at 1500°C.
- Deviations from this range, even by 150°C, can lead to reduced strength due to grain growth. For example, strength drops to 980 MPa at 1600°C and 600 MPa at 1700°C.
-
Transformation Temperatures:
- The transformation from the monoclinic to the polytetragonal structure of zirconia occurs at lower temperatures, typically between 1100°C and 1200°C.
- However, the final sintering process requires higher temperatures to achieve near-theoretical maximum density.
-
Importance of Temperature Control:
- Precise temperature control is critical during sintering. Even small deviations can significantly impact the material's properties.
- A slow heat rise of 4°C to 10°C per minute is often recommended to ensure uniform sintering and avoid defects.
-
Specialized Sintering Furnaces:
- Standard porcelain furnaces are insufficient for sintering zirconia. Specialized high-temperature sintering furnaces are required to reach the necessary temperatures.
- These furnaces are designed to handle the extreme heat and provide consistent results.
-
Impact of Sintering Temperature on Density:
- Higher sintering temperatures result in denser zirconia, often reaching close to 99% of the theoretical maximum density.
- This high density is crucial for achieving the material's desired mechanical properties, such as hardness and strength.
-
Practical Considerations for Purchasers:
- When purchasing sintering furnaces, ensure they can consistently achieve and maintain temperatures within the 1500°C to 1550°C range.
- Consider the furnace's temperature accuracy and uniformity, as these factors directly impact the quality of the sintered zirconia.
- Evaluate the furnace's ability to control the heating rate, as a slow and controlled rise is essential for optimal results.
By understanding these key points, purchasers can make informed decisions about the equipment and processes needed to achieve high-quality sintered zirconia with the desired properties.
Summary Table:
Aspect | Details |
---|---|
Sintering Temperature Range | 1400°C to 1600°C, with optimal results at 1500°C–1550°C. |
Optimal Strength | Peak strength of ~1280 MPa at 1500°C; drops to 980 MPa at 1600°C. |
Transformation Temperature | Monoclinic to polytetragonal occurs at 1100°C–1200°C. |
Heating Rate | Slow rise of 4°C–10°C per minute recommended for uniform sintering. |
Furnace Requirements | Specialized high-temperature furnaces needed for consistent results. |
Density | Close to 99% of theoretical maximum density achieved at optimal temperatures. |
Ensure your zirconia sintering process meets industry standards—contact our experts today for tailored solutions!