The sintering time for zirconia can vary significantly depending on the specific requirements of the process, the equipment used, and the desired properties of the final product. Generally, sintering times can range from a few seconds to over 24 hours. Traditional sintering processes often take between 15 to 20 hours, but modern techniques, such as high-speed sintering, can reduce this time to as little as 6 to 8 hours. Factors such as temperature, heating rate, pressure, particle size, and composition play crucial roles in determining the optimal sintering time. Understanding these factors can help in selecting the appropriate sintering parameters to achieve the desired density and material properties.
Key Points Explained:
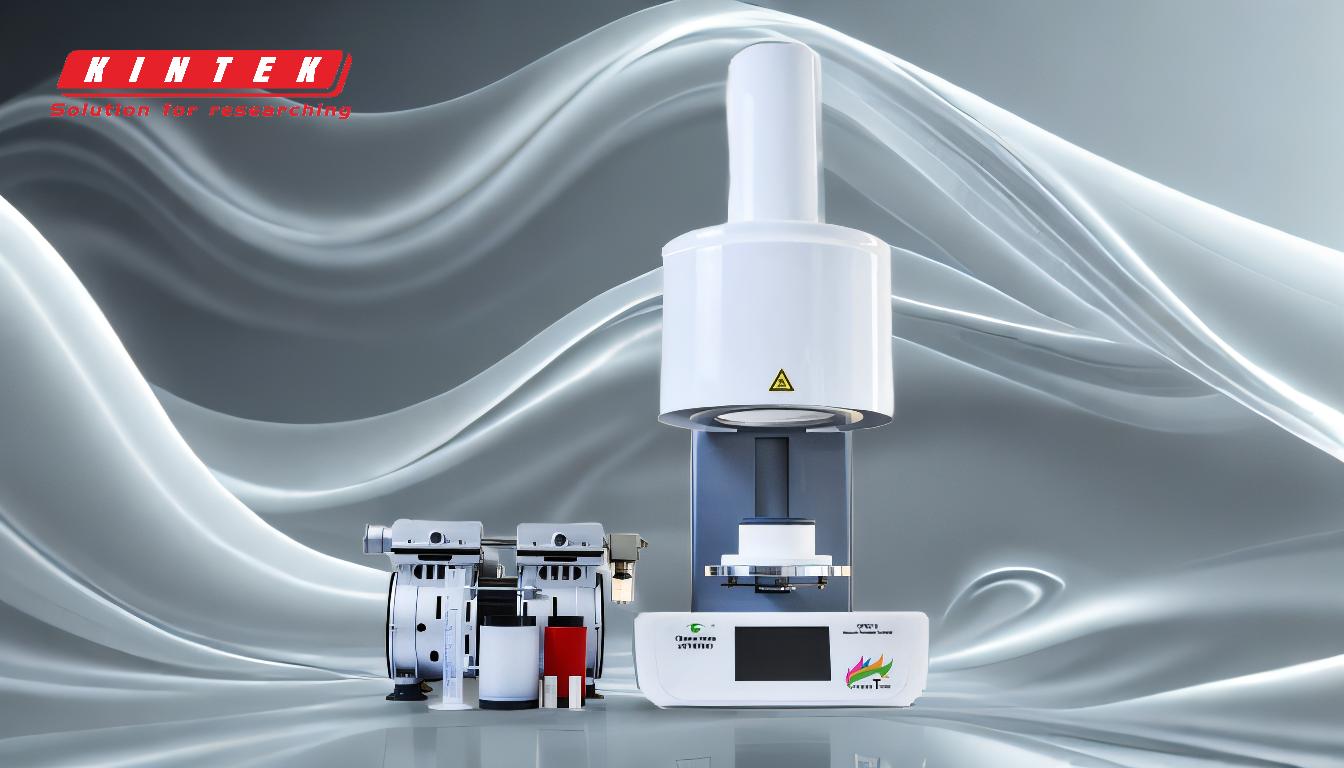
-
Typical Sintering Time for Zirconia:
- Traditional Sintering: Typically takes between 15 to 20 hours. This is a common duration for conventional sintering processes where the material is heated gradually to achieve the desired density and properties.
- High-Speed Sintering: Can reduce the sintering time to 6 to 8 hours. Some manufacturers offer high-speed sintering profiles that optimize the heating and cooling rates to achieve similar results in a shorter time frame.
-
Factors Influencing Sintering Time:
- Temperature: The sintering temperature is critical as it directly affects the kinetics of the sintering process. Higher temperatures can accelerate sintering but must be carefully controlled to avoid material degradation.
- Heating Rate: The rate at which the material is heated can influence the densification process. Faster heating rates can reduce sintering time but may also affect the final density and porosity.
- Pressure: Applying pressure during sintering can enhance particle rearrangement and eliminate porosity, potentially reducing the required sintering time.
- Particle Size: Smaller particles generally sinter faster due to their higher surface area and increased surface energy, which promotes densification.
- Composition: Homogeneous compositions tend to sinter more uniformly, leading to better densification and potentially shorter sintering times.
-
Techniques and Their Impact on Sintering Time:
- Field-Assisted Techniques: These methods, such as microwave or spark plasma sintering, can significantly reduce sintering times by providing additional energy to the material, promoting faster densification.
- Selective Laser Sintering: This additive manufacturing technique can sinter materials in seconds, but the post-form sintering step may still take several hours to achieve the final properties.
- Liquid Phase Sintering: The addition of a liquid phase can speed up the sintering process by enhancing particle mobility and promoting faster densification. However, this may also lead to reduced density and residual porosity if not carefully controlled.
-
Equipment and Environmental Considerations:
- Furnace Type: The type of furnace used (belt conveyor, push, or batch furnace) can influence the sintering time. Each furnace type has different heating and cooling capabilities, which can affect the overall process duration.
- Controlled Atmosphere: Sintering is often carried out in a controlled atmospheric environment to prevent oxidation and other unwanted reactions. The choice of atmosphere can also impact the sintering time and the quality of the final product.
-
Trade-offs and Considerations:
- Density vs. Time: Faster sintering processes may lead to reduced density and increased porosity. It is essential to balance the sintering time with the desired material properties.
- Material Properties: The final properties of the sintered zirconia, such as strength, hardness, and thermal conductivity, must be considered when determining the optimal sintering time and conditions.
In summary, the sintering time for zirconia is influenced by a variety of factors, including the sintering technique, equipment, and material properties. Traditional sintering processes typically take 15 to 20 hours, but modern techniques can reduce this time significantly. Understanding the interplay between these factors is crucial for optimizing the sintering process to achieve the desired material properties efficiently.
Summary Table:
Aspect | Details |
---|---|
Traditional Sintering | 15-20 hours for conventional processes. |
High-Speed Sintering | 6-8 hours with optimized heating and cooling rates. |
Key Factors | Temperature, heating rate, pressure, particle size, and composition. |
Modern Techniques | Field-assisted, selective laser, and liquid phase sintering reduce time. |
Equipment Impact | Furnace type and controlled atmosphere influence sintering time and quality. |
Optimize your zirconia sintering process—contact our experts today!