The source of evaporation for thin film deposition primarily involves heating the source material to its evaporation point, allowing it to transform into a vapor phase. This is achieved through methods such as resistive heating (using electrically heated wires or crucibles), electron beam heating, or other thermal sources. The process occurs in a vacuum to prevent contamination and ensure uniform deposition. The evaporated material then condenses onto a substrate, forming a thin film. The substrate's temperature, material purity, and vacuum conditions are critical factors influencing the quality and performance of the deposited film.
Key Points Explained:
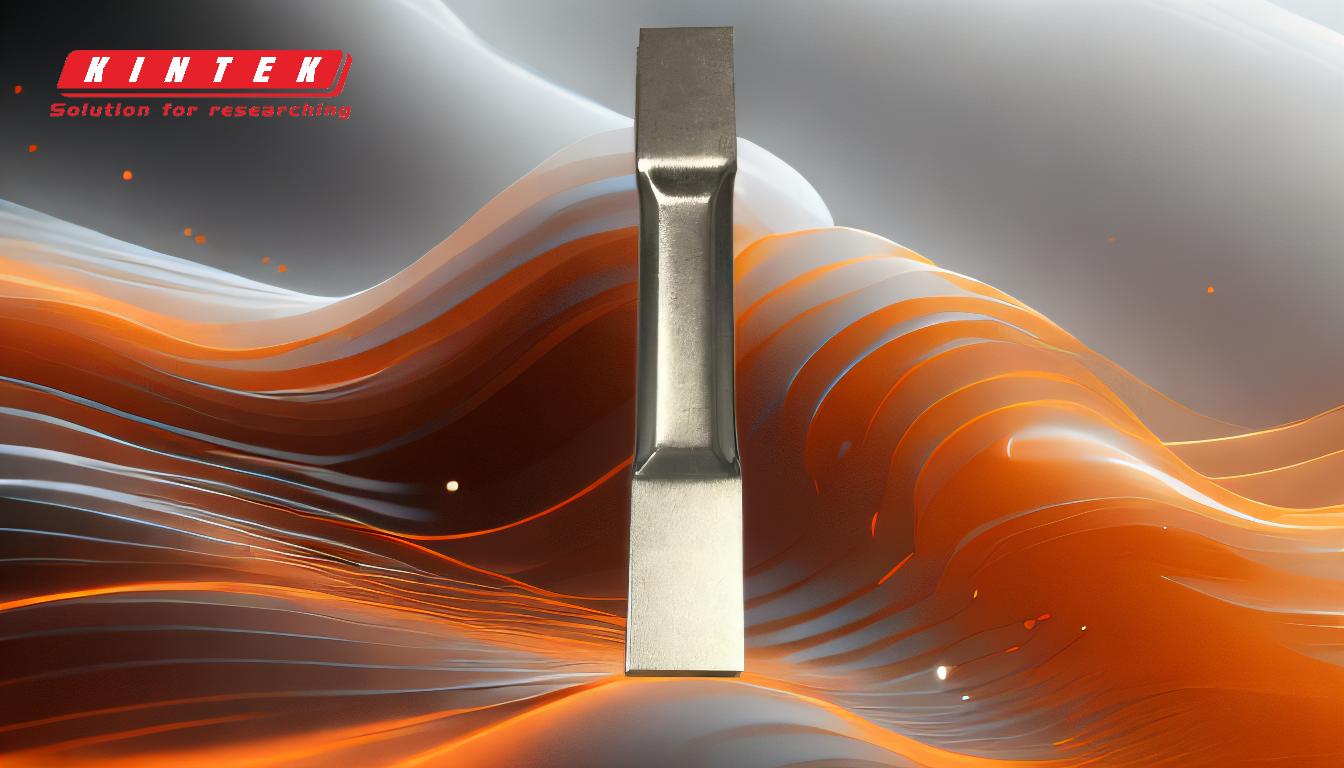
-
Evaporation Process in Thin Film Deposition:
- Evaporation is the process of converting a solid or liquid material into a vapor phase by applying heat.
- The vaporized material then condenses onto a substrate to form a thin film.
- This process is analogous to steam condensing into water droplets on a surface.
-
Heat Sources for Evaporation:
-
Resistive Heating:
- Electrically heated wires or crucibles are used to heat the source material.
- The material is placed in a crucible made of a material with a significantly higher melting point to withstand the high temperatures.
-
Electron Beam Heating:
- An electron beam is directed at the source material to melt and evaporate it.
- This method is particularly useful for materials with very high melting points.
-
Other Thermal Sources:
- Other methods, such as laser heating or induction heating, can also be used depending on the material and application.
-
Resistive Heating:
-
Role of Vacuum in Evaporation:
- The evaporation process must occur in a vacuum to:
- Prevent contamination from atmospheric gases.
- Ensure uniform deposition of the thin film.
- Maintain the integrity of the process by reducing collisions between vaporized atoms and gas molecules.
- The evaporation process must occur in a vacuum to:
-
Substrate Temperature and Its Influence:
- The temperature of the substrate plays a crucial role in the quality of the thin film.
- Heating the substrate above 150 °C can improve the adhesion of the film to the substrate.
- Proper substrate heating ensures that the evaporated atoms have enough energy to move freely and form a uniform film.
-
Factors Affecting Thin Film Quality:
-
Purity of the Source Material:
- High-purity materials are essential to avoid impurities in the deposited film.
-
Temperature and Pressure Conditions:
- Precise control of temperature and pressure is necessary to achieve the desired film properties.
-
Substrate Surface Preparation:
- The substrate surface must be clean and properly prepared to ensure good adhesion and uniformity of the film.
-
Purity of the Source Material:
-
Comparison to Everyday Phenomena:
- The evaporation process in thin film deposition can be compared to everyday phenomena such as steam condensing into water droplets on a cold surface.
- This analogy helps in understanding the basic principles of evaporation and condensation in a controlled environment.
By carefully controlling the heat source, vacuum conditions, substrate temperature, and material purity, high-quality thin films with desired properties can be achieved through the evaporation method.
Summary Table:
Aspect | Details |
---|---|
Evaporation Process | Converts solid/liquid to vapor phase for thin film deposition. |
Heat Sources | Resistive heating, electron beam heating, laser heating, induction heating. |
Vacuum Role | Prevents contamination, ensures uniform deposition, maintains process integrity. |
Substrate Temperature | Heating above 150°C improves film adhesion and uniformity. |
Key Factors | Material purity, temperature/pressure control, substrate surface preparation. |
Discover how to achieve high-quality thin films for your applications—contact our experts today!