The sputtering process in nanotechnology is a physical vapor deposition technique used to deposit thin films of material onto a substrate. It involves bombarding a target material with high-energy ions in a vacuum environment, causing atoms to be ejected from the target's surface. These ejected atoms then travel through the vacuum and deposit onto a substrate, forming a thin film with precise properties. The process is widely used in industries such as semiconductors, optics, and solar panels due to its ability to produce highly controlled and uniform coatings. Key components include a vacuum chamber, a target material, a substrate, and a sputtering gas like argon. The process is highly accurate and versatile, enabling the creation of films with specific electrical, optical, or mechanical properties.
Key Points Explained:
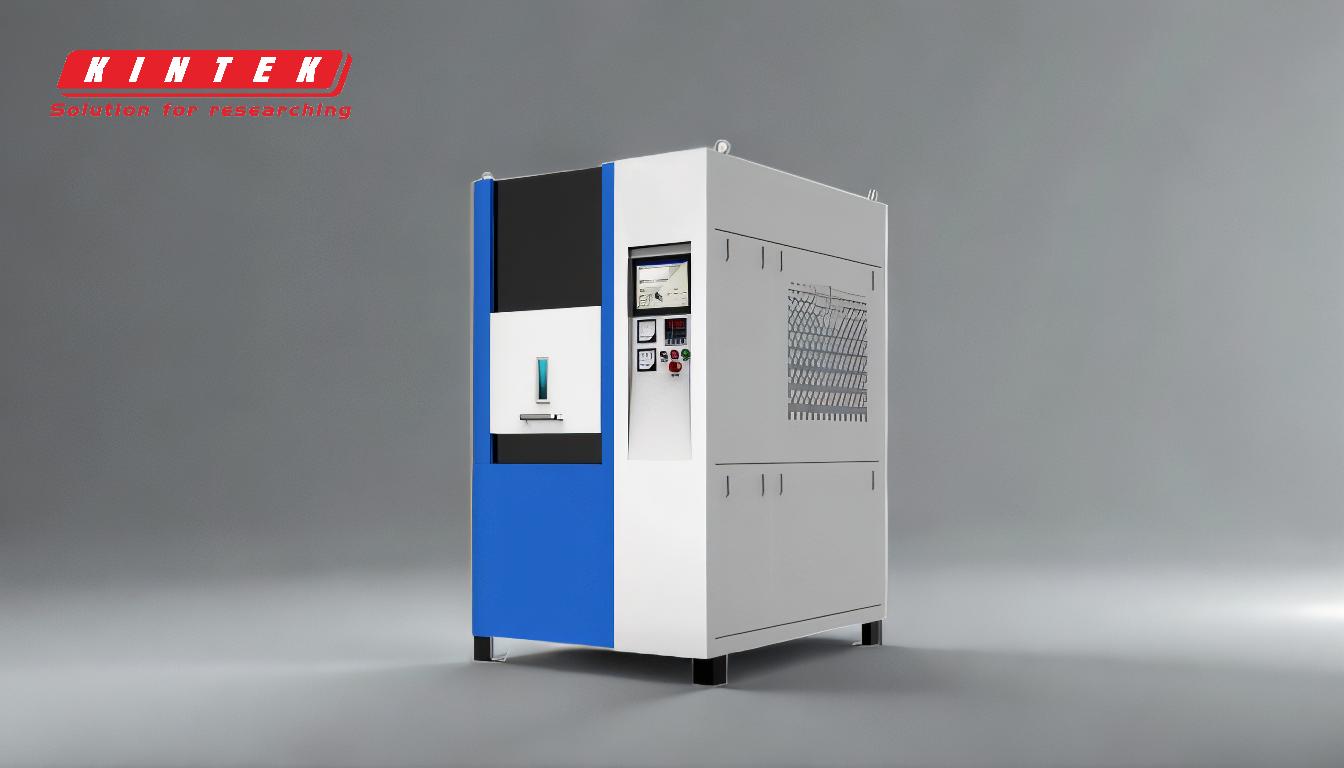
-
Definition and Mechanism of Sputtering:
- Sputtering is a physical process where atoms from a solid target material are ejected into the gas phase due to bombardment by energetic ions.
- The process occurs in a vacuum environment, ensuring minimal interference from external contaminants.
- The ejected atoms travel through the vacuum and deposit onto a substrate, forming a thin film.
-
Components of the Sputtering Process:
- Vacuum Chamber: A controlled environment where the sputtering process takes place, ensuring no contamination and enabling the formation of a plasma.
- Target Material: The source material from which atoms are ejected. Common materials include metals, alloys, and ceramics.
- Substrate: The surface onto which the ejected atoms deposit, forming a thin film. Substrates can be silicon wafers, glass, or plastics.
- Sputtering Gas: Typically an inert gas like argon or xenon, which is ionized to create a plasma that bombards the target material.
-
Steps in the Sputtering Process:
- Vacuum Creation: The chamber is evacuated to remove air and other gases, creating a high-vacuum environment.
- Gas Introduction: An inert gas, usually argon, is introduced into the chamber.
- Plasma Formation: A voltage is applied between the target (cathode) and the substrate (anode), ionizing the gas and creating a plasma.
- Ion Bombardment: The positively charged ions in the plasma are accelerated toward the target, striking it with sufficient energy to dislodge atoms.
- Film Deposition: The ejected atoms travel through the vacuum and deposit onto the substrate, forming a thin film.
-
Applications of Sputtering in Nanotechnology:
- Semiconductors: Used to deposit thin films of conductive, insulating, or semiconducting materials in the fabrication of integrated circuits.
- Optics: Creates reflective coatings for mirrors and anti-reflective coatings for lenses.
- Solar Panels: Deposits thin films of photovoltaic materials to enhance energy conversion efficiency.
- Data Storage: Used in the production of magnetic and optical storage media, such as hard drives and CDs.
- Packaging: Produces barrier coatings for food packaging to extend shelf life.
-
Advantages of Sputtering:
- Precision: Allows for highly controlled deposition of thin films with specific properties, such as thickness, uniformity, and composition.
- Versatility: Can deposit a wide range of materials, including metals, alloys, oxides, and nitrides.
- Scalability: Suitable for both small-scale research and large-scale industrial production.
- Film Quality: Produces films with excellent adhesion, density, and uniformity.
-
Challenges and Considerations:
- Cost: The equipment and vacuum requirements can be expensive.
- Complexity: Requires careful control of parameters such as gas pressure, voltage, and target-substrate distance.
- Material Limitations: Some materials may be difficult to sputter due to low sputtering yields or high melting points.
-
Historical Context and Evolution:
- Sputtering has been studied since the early 1800s, with significant advancements made in the 20th century.
- Modern sputtering techniques, such as magnetron sputtering, have improved deposition rates and film quality.
- The process continues to evolve, with ongoing research into new materials and applications in nanotechnology.
By understanding these key points, one can appreciate the critical role sputtering plays in nanotechnology and its wide-ranging applications in modern technology.
Summary Table:
Aspect | Details |
---|---|
Definition | Physical vapor deposition technique for thin film creation. |
Key Components | Vacuum chamber, target material, substrate, sputtering gas (e.g., argon). |
Steps | 1. Vacuum creation 2. Gas introduction 3. Plasma formation 4. Ion bombardment 5. Film deposition |
Applications | Semiconductors, optics, solar panels, data storage, packaging. |
Advantages | Precision, versatility, scalability, high-quality films. |
Challenges | High cost, process complexity, material limitations. |
Discover how sputtering can revolutionize your nanotechnology projects—contact us today for expert guidance!