Sputtering is a versatile thin-film deposition technique widely used in industries such as semiconductors, optics, and data storage. It involves bombarding a target material with high-energy ions in a vacuum chamber, causing atoms to be ejected and deposited onto a substrate. This method is highly controllable and can produce uniform, high-quality films ranging from nanometers to micrometers in thickness. Sputtering is used for applications like anti-reflective coatings, semiconductor metallization, and wear-resistant tool coatings. The process is precise, repeatable, and capable of depositing a wide range of materials, including metals, alloys, and compounds, making it a cornerstone of modern manufacturing and technology.
Key Points Explained:
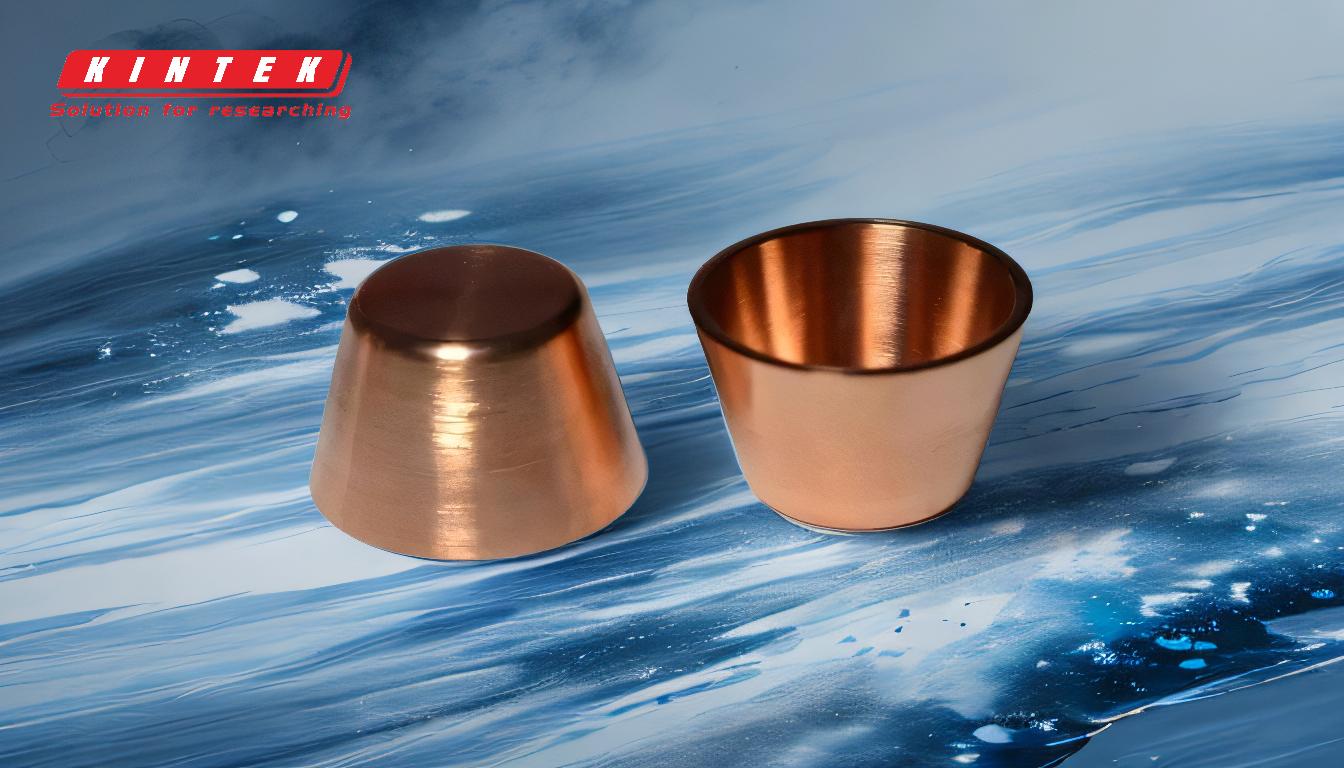
-
Definition of Sputtering
- Sputtering is a physical vapor deposition (PVD) technique where atoms are ejected from a solid target material due to bombardment by high-energy ions in a vacuum environment.
- The ejected atoms form a vapor stream that deposits onto a substrate, creating a thin film.
- This process is highly controllable and can produce films with precise thickness and composition.
-
Mechanism of Sputtering
- A controlled gas, typically argon, is introduced into a vacuum chamber.
- A cathode is electrically energized to generate a plasma, ionizing the gas atoms.
- The positively charged ions are accelerated toward the target material, dislodging atoms or molecules upon impact.
- These dislodged atoms form a vapor stream that deposits onto the substrate, forming a thin film.
-
Applications of Sputtering Deposition
- Semiconductor Industry: Used for depositing thin films in integrated circuits, such as metallization layers and contact metals in thin-film transistors.
- Optics and Glass: Applied for anti-reflective coatings, low-emissivity coatings, and high-emissivity films on glass.
- Data Storage: Used in the production of computer hard disks, CDs, and DVDs.
- Tool Coatings: Deposits wear-resistant coatings like titanium nitride on cutting tools.
- Solar Cells: Utilized in the fabrication of photovoltaic solar cells.
- Decorative and Functional Coatings: Applied for reflective coatings on polymers, dry-film lubricants, and decorative finishes.
-
Advantages of Sputtering
- Uniformity: Produces highly uniform and dense films.
- Versatility: Can deposit a wide range of materials, including metals, alloys, and compounds.
- Precision: Allows for precise control over film thickness and composition.
- Adhesion: Ensures strong adhesion of the film to the substrate.
- Scalability: Suitable for large-scale industrial production.
-
Types of Sputtering Techniques
- DC Sputtering: Uses direct current to generate plasma, suitable for conductive materials.
- RF Sputtering: Uses radio frequency to ionize the gas, enabling the deposition of non-conductive materials.
- Magnetron Sputtering: Incorporates magnetic fields to enhance plasma density, improving deposition rates and film quality.
- Reactive Sputtering: Introduces reactive gases (e.g., nitrogen or oxygen) to form compound films like oxides or nitrides.
-
Key Components of a Sputtering System
- Vacuum Chamber: Maintains a controlled environment for the process.
- Target Material: The source of atoms to be deposited.
- Substrate: The surface onto which the thin film is deposited.
- Power Supply: Provides energy to generate plasma.
- Gas Delivery System: Introduces and controls the flow of sputtering gas.
-
Challenges and Considerations
- Cost: High initial investment for equipment and maintenance.
- Complexity: Requires precise control of parameters like pressure, power, and gas flow.
- Material Limitations: Some materials may be difficult to sputter due to low sputter yields or high melting points.
- Contamination: Requires careful handling to avoid impurities in the deposited film.
-
Future Trends in Sputtering Technology
- Advanced Materials: Development of new target materials for specialized applications.
- Sustainability: Focus on reducing energy consumption and environmental impact.
- Automation: Integration of AI and machine learning for process optimization.
- Miniaturization: Adaptation for nanotechnology and microelectronics.
In summary, sputtering is a critical technique in modern manufacturing, enabling the deposition of high-quality thin films for a wide range of applications. Its precision, versatility, and scalability make it indispensable in industries like semiconductors, optics, and energy.
Summary Table:
Aspect | Details |
---|---|
Definition | Physical vapor deposition (PVD) technique using high-energy ions. |
Mechanism | Bombardment of target material in a vacuum chamber to deposit thin films. |
Applications | Semiconductors, optics, data storage, tool coatings, solar cells, and more. |
Advantages | Uniformity, versatility, precision, strong adhesion, and scalability. |
Techniques | DC, RF, magnetron, and reactive sputtering. |
Components | Vacuum chamber, target material, substrate, power supply, gas delivery. |
Challenges | High cost, complexity, material limitations, and contamination risks. |
Future Trends | Advanced materials, sustainability, automation, and miniaturization. |
Discover how sputtering can enhance your manufacturing process—contact our experts today!