Brazing aluminum is a widely used process in industries requiring strong, durable, and corrosion-resistant joints. The strength of brazing aluminum primarily depends on the alloy composition, particularly the Al-Si system, which is the most common brazing material. The eutectic Al-Si alloy with 11.7% silicon offers excellent brazeability, strength, and compatibility with various aluminum base materials. The process involves precise control of vacuum levels, temperature uniformity, and heating cycles to ensure optimal joint strength. The resulting brazed joints exhibit high toughness, bending strength, and resistance to corrosion, making them suitable for demanding applications.
Key Points Explained:
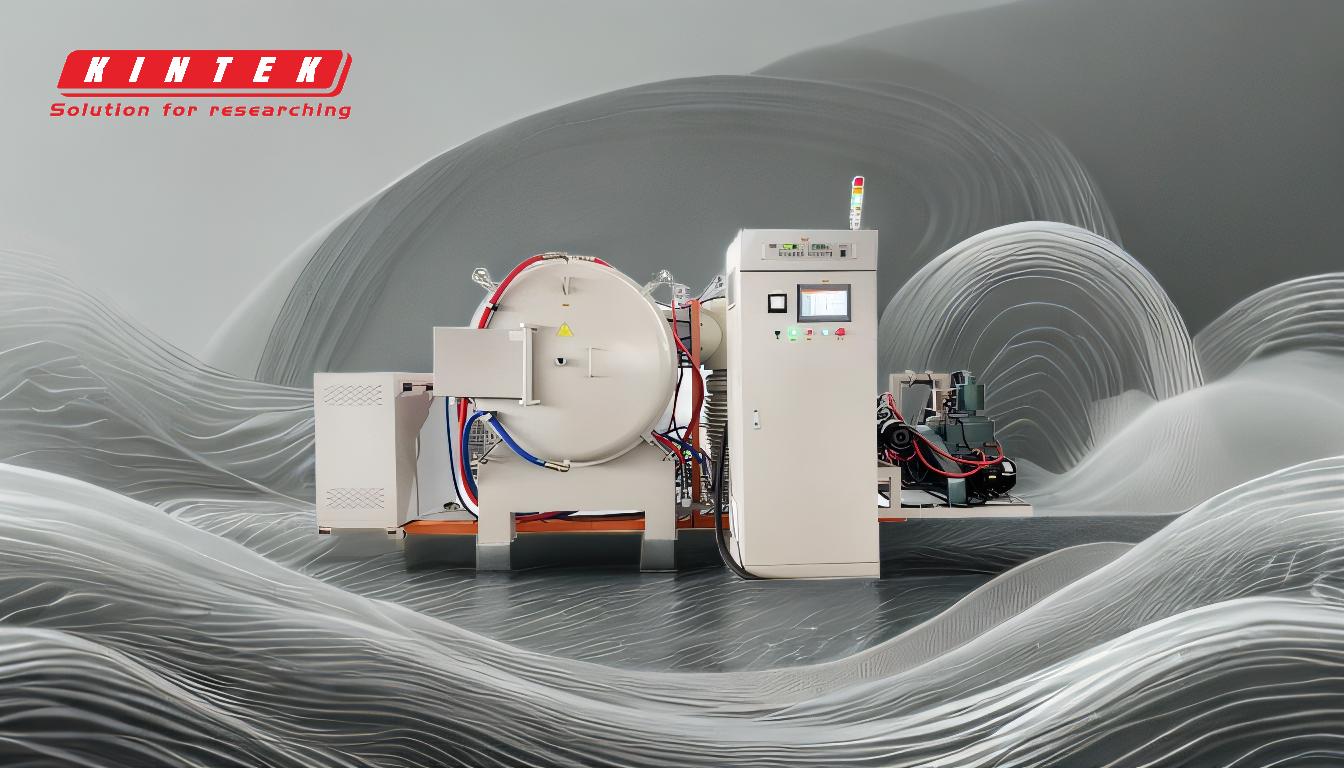
-
Al-Si Brazing Alloys:
- The most commonly used brazing alloys for aluminum are based on the Al-Si system, with silicon content (w(si)) ranging from 7% to 12%.
- These alloys are preferred due to their excellent brazeability, strength, and compatibility with aluminum base materials.
- The eutectic Al-Si alloy with 11.7% silicon has a eutectic temperature of 577°C, making it ideal for brazing aluminum alloys with relatively high melting points.
-
Strength and Durability:
- Brazed joints made with Al-Si alloys exhibit high toughness and bending strength, which are critical for structural applications.
- The densification of the brazing alloy during the process further enhances the mechanical properties of the joint.
- The resulting joints also maintain color consistency with the base material and offer excellent corrosion resistance.
-
Process Parameters:
- Vacuum Levels: Maintaining vacuum levels in the range of 10^-5 mbar or better is crucial for achieving high-quality brazed joints.
- Temperature Control: Heating parts to temperatures between 575°C and 590°C, depending on the alloy, ensures proper melting and flow of the brazing material.
- Temperature Uniformity: Ensuring temperature uniformity within ±5.5°C across the parts is essential to prevent defects and achieve consistent joint strength.
- Furnace Type: Multiple-zone temperature-controlled furnaces are typically used to achieve precise temperature control and uniformity.
-
Cycle Times:
- The cycle time for brazing aluminum depends on factors such as furnace type, part configuration, and fixturing.
- Properly designed fixturing ensures that parts are held securely during the brazing process, minimizing distortion and ensuring consistent joint quality.
-
Applications:
- The strength and durability of brazed aluminum joints make them suitable for a wide range of applications, including aerospace, automotive, and heat exchangers.
- The corrosion resistance of the joints is particularly beneficial in environments exposed to harsh conditions.
In summary, the strength of brazing aluminum is largely determined by the choice of Al-Si brazing alloys, precise control of process parameters, and the quality of the brazing equipment. The resulting joints offer excellent mechanical properties, corrosion resistance, and compatibility with aluminum base materials, making them ideal for demanding industrial applications.
Summary Table:
Key Factor | Details |
---|---|
Brazing Alloy | Al-Si system with 7-12% silicon; 11.7% Si eutectic at 577°C |
Joint Strength | High toughness, bending strength, and corrosion resistance |
Process Parameters | Vacuum levels: 10^-5 mbar; Temperature: 575-590°C; Uniformity: ±5.5°C |
Furnace Type | Multiple-zone temperature-controlled furnaces |
Applications | Aerospace, automotive, heat exchangers, and harsh environments |
Unlock the full potential of brazing aluminum for your applications—contact our experts today!