A rotary kiln is a complex piece of industrial equipment designed for high-temperature processing of materials. Its structure is carefully engineered to ensure efficient heat transfer, material movement, and durability under extreme conditions. The primary components include the kiln shell, refractory lining, support tyres (riding rings) and rollers, drive gear, and internal heat exchangers. These components work together to facilitate the rotation, heating, and processing of materials. The kiln shell is typically cylindrical and tapered at the ends, while the drive assembly ensures smooth rotation. The support system, including tyres and rollers, maintains alignment and stability. The refractory lining protects the shell from high temperatures, and internal heat exchangers optimize thermal efficiency. Understanding the structure of a rotary kiln is essential for proper operation, maintenance, and customization to meet specific industrial needs.
Key Points Explained:
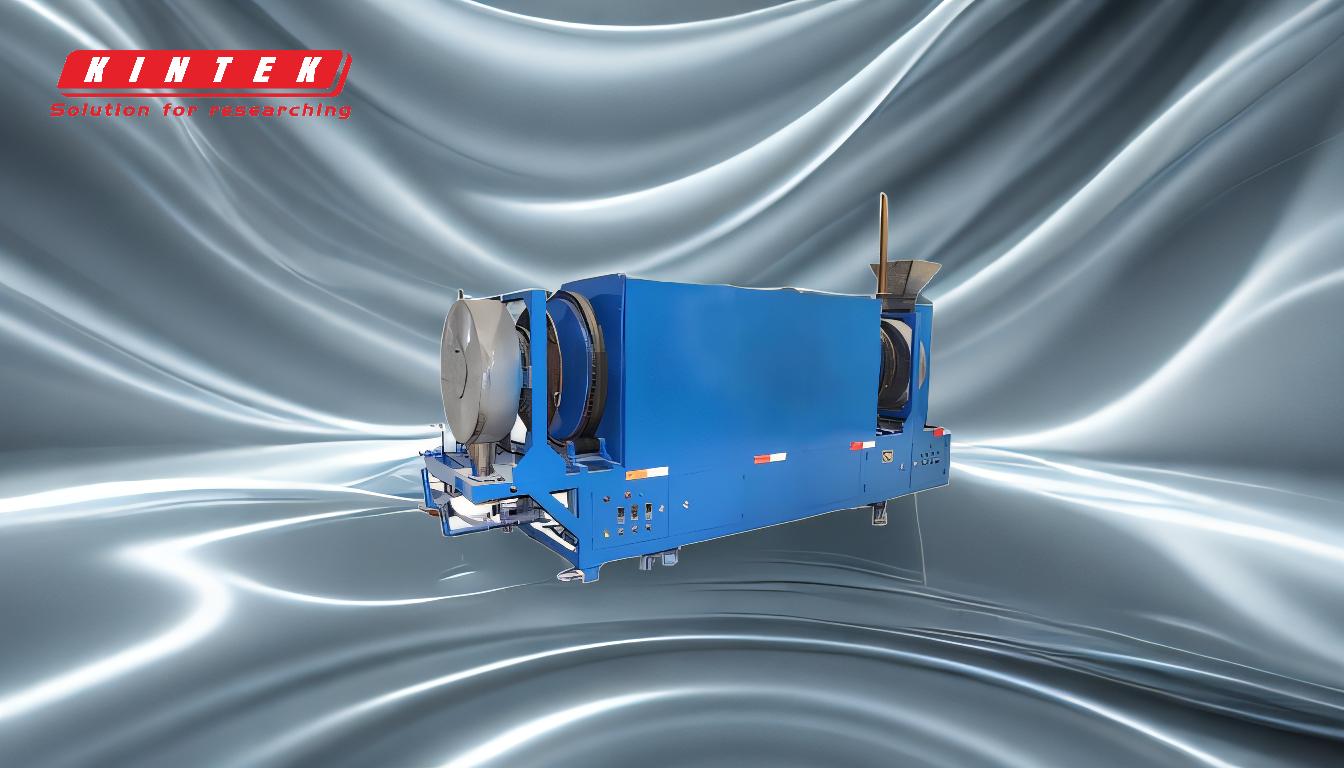
-
Kiln Shell
- The kiln shell is the outermost cylindrical structure of the rotary kiln, typically made of high-strength steel to withstand extreme temperatures and mechanical stresses.
- It is conically tapered at the ends to facilitate material flow and reduce wear.
- The shell experiences torsion and flexural stress due to rotation and the weight of the materials inside.
- Its design ensures durability and efficient heat transfer to the materials being processed.
-
Refractory Lining
- The refractory lining is an inner layer of heat-resistant material that protects the kiln shell from high temperatures and chemical reactions.
- It is essential for maintaining the structural integrity of the kiln and ensuring consistent thermal performance.
- The lining is customized based on the specific material being processed and the operating temperature range.
- Regular maintenance and replacement of the refractory lining are necessary to prevent damage and ensure optimal performance.
-
Support System (Tyres and Rollers)
- The support system consists of tyres (riding rings) and rollers that hold the kiln in place and allow it to rotate smoothly.
- Tyres are large rings mounted on the kiln shell, while rollers are positioned beneath the tyres to provide support and alignment.
- This system ensures the kiln remains stable and properly aligned during operation, preventing excessive wear and tear.
- Thrust rollers are used to control axial movement and maintain the kiln's position.
-
Drive Assembly
- The drive assembly is responsible for rotating the kiln at a controlled speed, ensuring consistent material processing.
- It can be a chain and sprocket drive, gear drive, friction drive, or direct drive assembly, depending on the kiln's size and application.
- The drive system is designed to handle the heavy load of the kiln and materials while maintaining precise control over rotation speed.
- Proper maintenance of the drive assembly is critical to prevent operational disruptions.
-
Internal Heat Exchangers
- Internal heat exchangers are components designed to optimize heat transfer within the kiln, improving energy efficiency.
- They ensure that the heat generated by fuel combustion is effectively transferred to the materials being processed.
- These components can be customized based on the specific requirements of the material and the desired thermal performance.
- Efficient heat exchangers reduce fuel consumption and operating costs.
-
Additional Components
- Trunnion Wheels: These support the kiln and allow it to rotate smoothly.
- Discharge Breeching: This component directs the processed material out of the kiln.
- Product Discharge Area: The area where the final product is collected after processing.
- Customization: Many components can be customized to meet specific industrial needs, though this often comes at a higher cost.
By understanding the structure of a rotary kiln, equipment purchasers can make informed decisions about customization, maintenance, and operational efficiency. Each component plays a critical role in ensuring the kiln's performance and longevity, making it essential to consider all aspects when selecting or maintaining a rotary kiln.
Summary Table:
Component | Function |
---|---|
Kiln Shell | Outer cylindrical structure made of high-strength steel for durability. |
Refractory Lining | Heat-resistant inner layer protecting the shell and ensuring thermal performance. |
Support System | Tyres and rollers for stability, alignment, and smooth rotation. |
Drive Assembly | Ensures controlled rotation of the kiln for consistent material processing. |
Heat Exchangers | Optimizes heat transfer for energy efficiency and reduced operating costs. |
Additional Parts | Includes trunnion wheels, discharge breeching, and product discharge area. |
Need a rotary kiln tailored to your industrial needs? Contact our experts today for a customized solution!