The temperature of a burn-off oven typically ranges between 500°F (260°C) and 1000°F (538°C), depending on the specific application and the materials being processed. Burn-off ovens are designed to remove organic contaminants, such as oils, greases, and paints, from metal parts or tools through a process called pyrolysis. The temperature must be high enough to break down these contaminants into ash or gas without damaging the underlying material. The exact temperature setting depends on factors like the type of contaminant, the material of the part, and the desired cycle time. Proper temperature control ensures efficient cleaning while maintaining the integrity of the parts.
Key Points Explained:
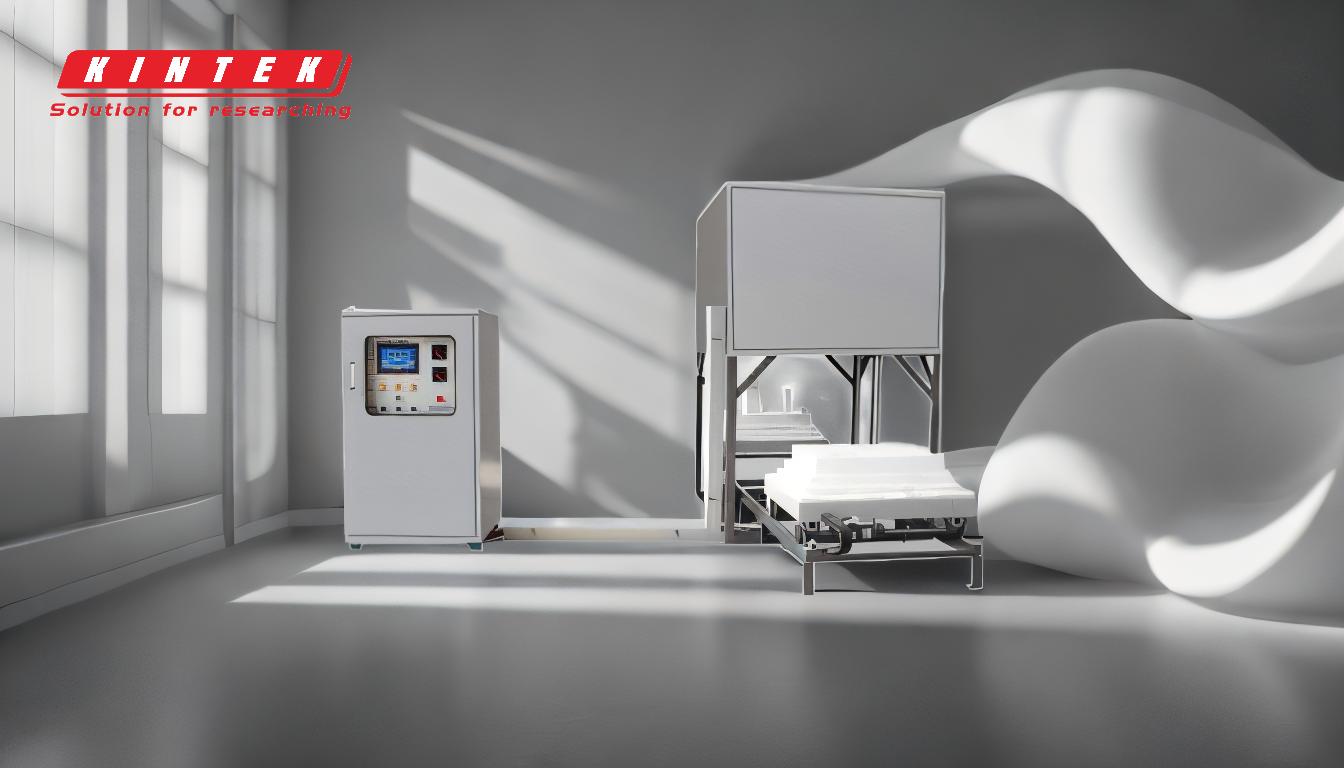
-
Purpose of a Burn-Off Oven:
- Burn-off ovens are primarily used to remove organic contaminants like oils, greases, paints, and adhesives from metal parts or tools.
- The process, known as pyrolysis, involves heating the contaminants to a temperature where they decompose into ash or gaseous byproducts.
-
Typical Temperature Range:
- The temperature of a burn-off oven usually ranges between 500°F (260°C) and 1000°F (538°C).
- Lower temperatures (around 500°F) are suitable for light contaminants, while higher temperatures (up to 1000°F) are used for heavier or more stubborn residues.
-
Factors Influencing Temperature Selection:
- Type of Contaminant: Different organic materials have varying decomposition temperatures. For example, oils and greases may require lower temperatures, while paints or adhesives might need higher heat.
- Material of the Part: The base material being cleaned must withstand the selected temperature without warping, discoloration, or other damage.
- Cycle Time: Higher temperatures can reduce the time required for complete contaminant removal, but they must be balanced against the risk of damaging the parts.
-
Temperature Control and Safety:
- Burn-off ovens are equipped with precise temperature controls to ensure consistent and safe operation.
- Proper ventilation is essential to handle the fumes and gases produced during the pyrolysis process.
-
Applications of Burn-Off Ovens:
- Commonly used in industries like automotive, aerospace, and manufacturing for cleaning tools, parts, and equipment.
- Also used in restoration projects to remove old coatings or residues from metal surfaces.
-
Benefits of Using a Burn-Off Oven:
- Efficiency: Quickly and effectively removes contaminants without the need for harsh chemicals.
- Eco-Friendly: Produces minimal waste compared to chemical cleaning methods.
- Versatility: Can handle a wide range of materials and contaminants.
By understanding the temperature requirements and operational principles of a burn-off oven, users can optimize the cleaning process for their specific needs while ensuring the longevity and quality of their parts.
Summary Table:
Aspect | Details |
---|---|
Temperature Range | 500°F (260°C) to 1000°F (538°C) |
Purpose | Removes oils, greases, paints, and adhesives via pyrolysis. |
Key Factors | Contaminant type, part material, and cycle time. |
Applications | Automotive, aerospace, manufacturing, and restoration projects. |
Benefits | Efficient, eco-friendly, and versatile contaminant removal. |
Need a burn-off oven for your application? Contact us today to find the perfect solution!