The temperature of catalytic pyrolysis varies depending on the desired end product and the specific process conditions. Generally, catalytic pyrolysis occurs within a temperature range of 450°C to 800°C, with different temperature zones yielding different products. Lower temperatures (below 450°C) favor biochar production, intermediate temperatures (450°C to 600°C) are optimal for bio-oil, and higher temperatures (above 800°C) produce gases. The heating rate and residence time also play critical roles in determining the efficiency and output of the pyrolysis process.
Key Points Explained:
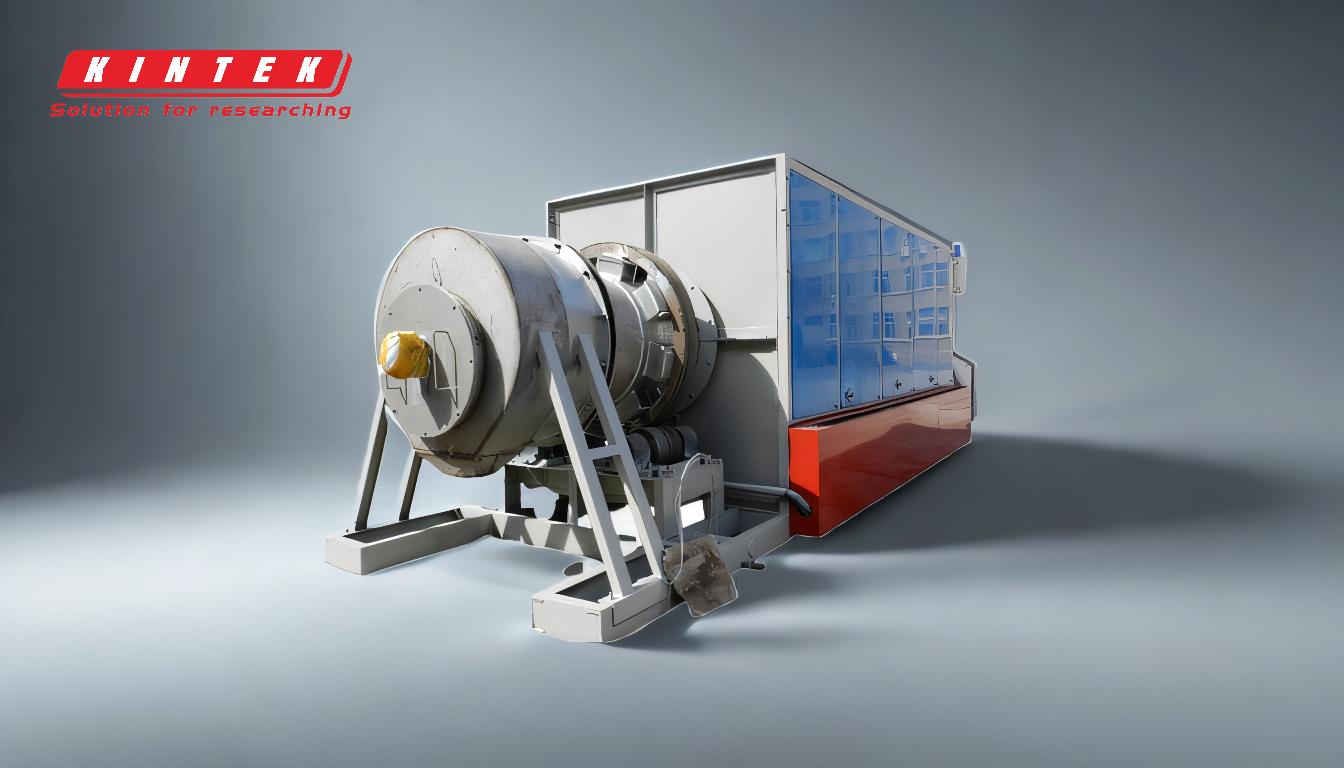
-
Temperature Ranges for Different Products:
- Low Temperatures (<450°C): At these temperatures, pyrolysis primarily produces biochar. This is due to the slow heating rates and incomplete decomposition of organic materials, leaving behind a solid carbon-rich residue.
- Intermediate Temperatures (450°C–600°C): This range is optimal for bio-oil production. The relatively high heating rates and controlled conditions allow for the breakdown of organic materials into liquid hydrocarbons, which are then condensed into bio-oil.
- High Temperatures (>800°C): At these temperatures, pyrolysis mainly yields gases. The rapid heating rates and high energy input cause the organic materials to break down completely into smaller molecules, resulting in syngas (a mixture of hydrogen, carbon monoxide, and other gases).
-
Optimal Temperature for Bio-Oil Production:
- A temperature range of 500°C to 600°C is ideal for maximizing bio-oil yield. This range balances the decomposition of organic materials and the condensation of liquid hydrocarbons, reducing the overall production cost.
-
Flash Pyrolysis Conditions:
- For effective flash pyrolysis, the temperature should be within 450°C to 600°C, with a heating rate of 10^3 to 10^4 °C/s and a residence time of less than 1 second. These conditions ensure rapid decomposition of the feedstock and high bio-oil yields.
-
Medium Temperature Pyrolysis:
- Medium temperature pyrolysis typically occurs between 600°C and 700°C. This range is often used when a balance between bio-oil and gas production is desired.
-
Factors Influencing Pyrolysis:
- Temperature: The primary factor determining the type of product (biochar, bio-oil, or gas).
- Heating Rate: Affects the speed of decomposition and the distribution of products.
- Residence Time: Influences the extent of decomposition and the quality of the end products.
- Atmosphere and Pressure: Can alter the chemical reactions and product yields.
- Feed Rate: Determines the amount of material processed and the efficiency of the pyrolysis process.
-
Reactor Temperature for High-Temperature Pyrolysis:
- In a pyrolysis reactor, temperatures can reach 350°C to 400°C, which is sufficient for high-temperature pyrolysis. This process breaks down waste materials into valuable products such as pyrolysis oil, carbon black, and syngas.
By understanding these temperature ranges and their effects on pyrolysis, equipment and consumable purchasers can make informed decisions about the type of pyrolysis process to implement based on the desired end products.
Summary Table:
Temperature Range | Product | Key Characteristics |
---|---|---|
<450°C | Biochar | Slow heating rates, incomplete decomposition, solid carbon-rich residue. |
450°C–600°C | Bio-Oil | Optimal for liquid hydrocarbons, high heating rates, controlled conditions. |
>800°C | Gases (Syngas) | Rapid heating, complete breakdown into smaller molecules (hydrogen, carbon monoxide). |
500°C–600°C | Optimal Bio-Oil | Maximizes yield, balances decomposition and condensation, reduces production costs. |
450°C–600°C (Flash) | High Bio-Oil Yield | Heating rate: 10^3 to 10^4 °C/s, residence time: <1 second. |
600°C–700°C | Bio-Oil & Gas | Balances bio-oil and gas production. |
350°C–400°C (Reactor) | Pyrolysis Oil | Breaks down waste into pyrolysis oil, carbon black, and syngas. |
Ready to optimize your pyrolysis process? Contact our experts today for tailored solutions!