Pyrolysis is a thermal decomposition process that occurs in the absence of oxygen, and temperature plays a pivotal role in determining the outcome of the reaction. For household fuel charcoal, the temperature is typically maintained between 400-450°C to ensure that some volatile content is retained. This temperature range is crucial for producing reactive free radicals during the thermal breakdown of wood, which ultimately influences the final product distribution. Factors such as temperature, pressure, and the residence time of volatiles are key parameters that affect the efficiency and output of the pyrolysis process. Additionally, the design of the pyrolysis reactor, including its thickness (typically 16mm), also contributes to the overall performance and durability of the system.
Key Points Explained:
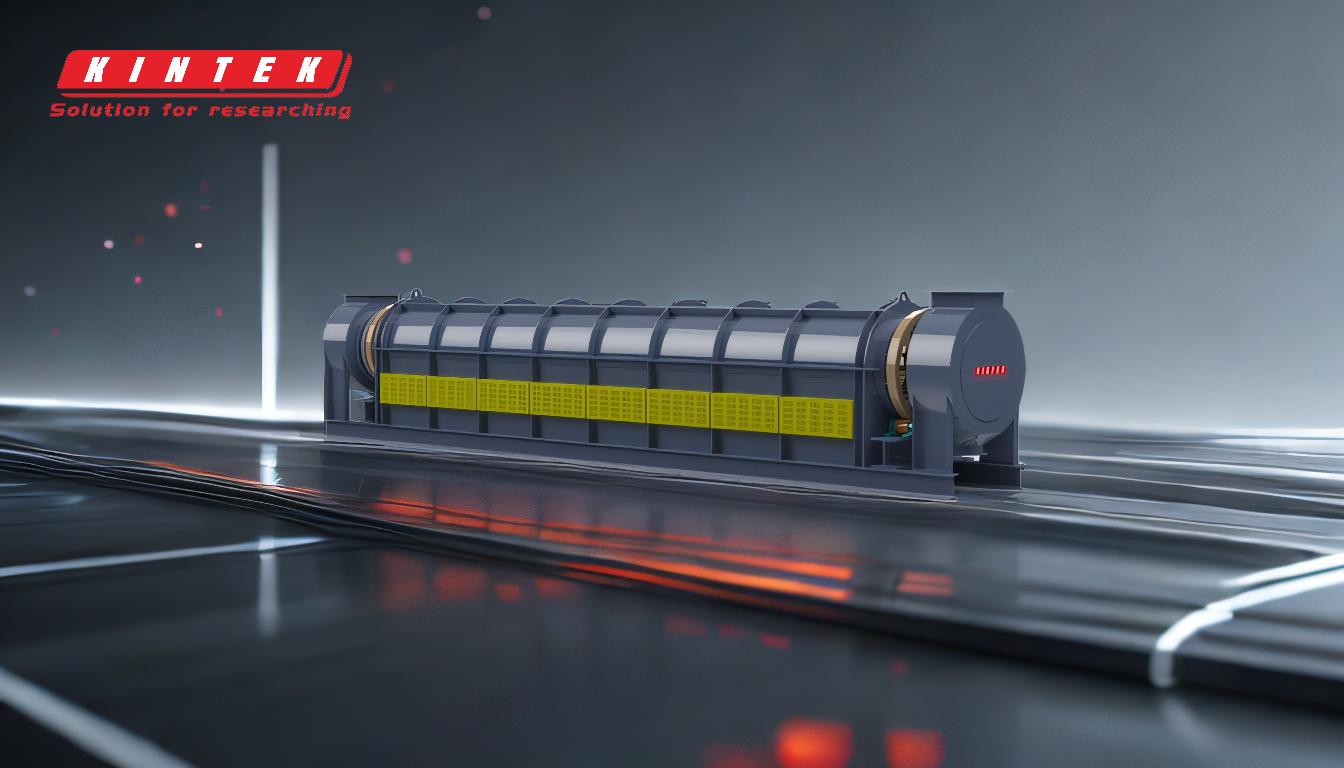
-
Temperature Range for Pyrolysis:
- Pyrolysis typically occurs within a specific temperature range, which varies depending on the material being processed and the desired end products.
- For household fuel charcoal, the temperature is usually kept between 400-450°C. This range ensures that some volatile content is retained, which is essential for the quality and usability of the charcoal.
-
Role of Temperature in Product Distribution:
- The thermal breakdown of materials like wood produces reactive free radicals. The distribution of these radicals and the final products (such as gases, liquids, and solids) are highly dependent on the temperature.
- Higher temperatures can lead to more complete decomposition, but may also result in the loss of desirable volatile compounds. Conversely, lower temperatures may leave more volatile content intact but could result in incomplete decomposition.
-
Influence of Other Parameters:
- Pressure: The pressure within the pyrolysis reactor can affect the rate of decomposition and the types of products formed. Higher pressures may favor the formation of certain compounds over others.
- Residence Time: The amount of time that volatiles spend in the reactor can also impact the final product distribution. Longer residence times may allow for more complete reactions, but could also lead to the degradation of some products.
-
Design of the Pyrolysis Reactor:
- The physical design of the pyrolysis reactor is crucial for efficient operation. A typical reactor thickness of 16mm ensures durability and can withstand the high temperatures and pressures involved in the process.
- The reactor's design also influences heat distribution and the overall efficiency of the pyrolysis process, making it a key factor in achieving the desired product outcomes.
-
Applications and Implications:
- Understanding the temperature and other parameters of pyrolysis is essential for optimizing the process for specific applications, such as the production of biochar, syngas, or bio-oil.
- The ability to control these parameters allows for the customization of the pyrolysis process to meet the needs of different industries, from energy production to waste management.
In summary, the temperature of pyrolysis is a critical factor that influences the efficiency, product distribution, and quality of the end products. By carefully controlling the temperature, along with other parameters like pressure and residence time, it is possible to optimize the pyrolysis process for various applications. The design of the reactor, including its thickness, also plays a significant role in ensuring the durability and effectiveness of the system.
Summary Table:
Parameter | Details |
---|---|
Temperature Range | 400-450°C for household fuel charcoal |
Key Role | Influences reactive free radicals and final product distribution |
Other Parameters | Pressure, residence time, and reactor design (e.g., 16mm thickness) |
Applications | Biochar, syngas, bio-oil production, and waste management |
Ready to optimize your pyrolysis process? Contact our experts today for tailored solutions!