Rotary kilns are versatile industrial equipment designed to operate across a wide temperature range, typically from 200°C to 2500°C, depending on the specific application and process requirements. This broad range allows rotary kilns to support diverse industrial processes, including cement production, calcination, and thermal treatment of materials. The temperature distribution within the kiln is carefully controlled to ensure consistent heating and gradual temperature changes along the length of the kiln, which is critical for maintaining process efficiency and product quality. Additionally, factors such as rotation speed, material flow rate, and heating zones play a significant role in optimizing the kiln's performance.
Key Points Explained:
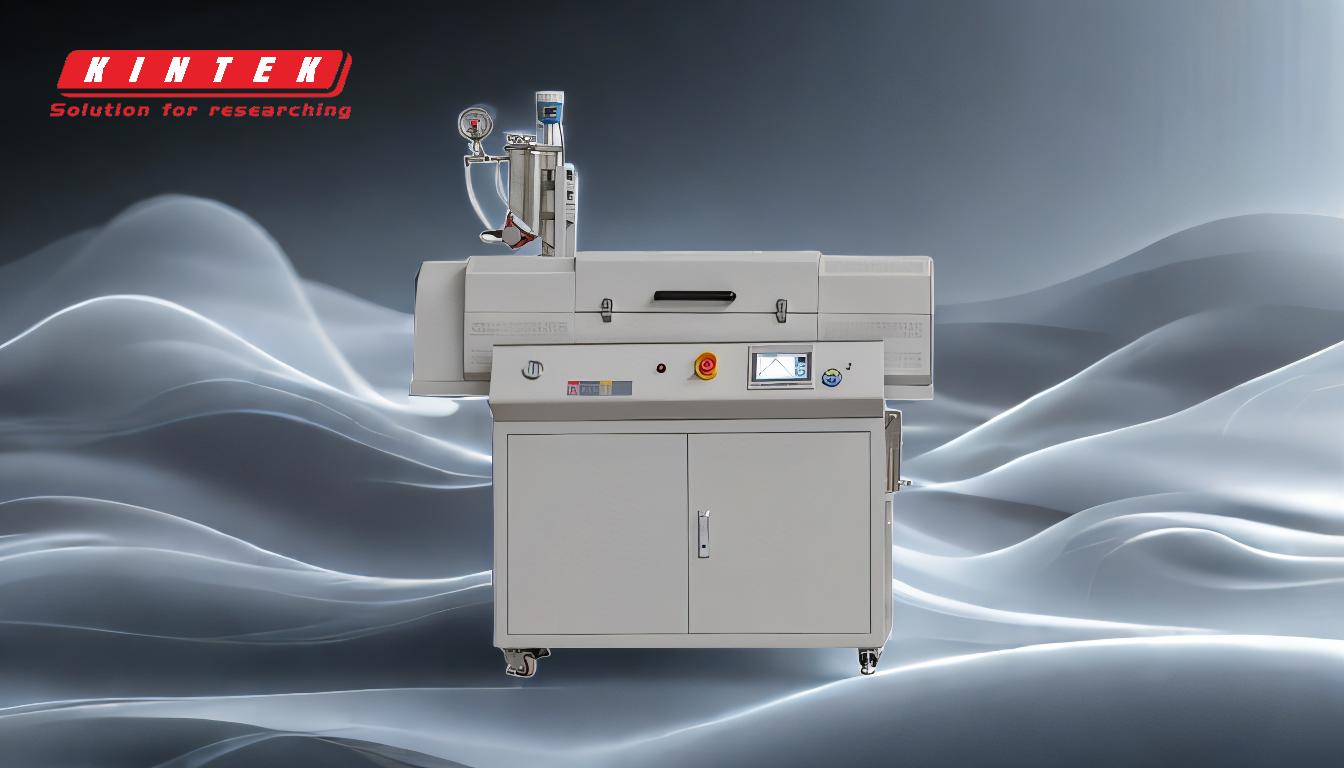
-
Temperature Range of Rotary Kilns:
- Rotary kilns are designed to operate across a wide temperature spectrum, from 200°C to 2500°C. This flexibility makes them suitable for a variety of industrial applications, including cement production, calcination, and material processing.
- The specific temperature range depends on the process requirements and the type of material being processed. For example, in cement production, temperatures can reach up to 1450°C, while in specialized processes like metal oxide reduction, temperatures can exceed 2000°C.
-
Temperature Distribution Within the Kiln:
- Along the length of the rotary kiln, the temperature should exhibit a gradual shift from one end to the other. This ensures proper heating and processing of materials.
- A consistent temperature around the circumference of the kiln at any given point is critical. Sudden or drastic temperature changes can indicate operational issues, such as uneven heating or material flow problems.
-
Indirect Rotary Kiln Temperatures:
- In indirect rotary kilns, the furnace tube temperature typically ranges between 1200°C and 1300°C, while the material temperature is maintained below 1150°C. This setup ensures efficient heat transfer without overheating the material.
- Indirect kilns are often used for processes requiring precise temperature control and minimal contamination.
-
Influence of Operational Parameters:
- The rotation speed of a rotary kiln typically ranges from 0.5 to 5 rpm, depending on the application. Higher rotation speeds are used in modern cement plants to increase material flow and processing efficiency.
- Other critical parameters include the inclination angle, material flow rate, and retention time of solid particles. These factors determine the kiln's performance and the quality of the final product.
-
Heating Zones in Rotary Kilns:
- Rotary kilns are divided into multiple heating zones, such as drying, heating, reaction, and soaking zones. The number and configuration of these zones depend on whether the kiln uses a wet or dry feed.
- Each zone is designed to achieve specific temperature and processing goals, ensuring optimal material transformation and energy efficiency.
-
Control Mechanisms:
- The bed depth of materials in the kiln is controlled using a ring dam, which helps regulate material flow and retention time.
- Modern rotary kilns are equipped with advanced control systems to monitor and adjust parameters such as temperature, rotation speed, and material flow in real time, ensuring consistent performance and product quality.
By understanding these key points, equipment and consumable purchasers can make informed decisions about selecting and operating rotary kilns for their specific industrial needs. The ability to control and optimize these parameters ensures efficient and reliable operation, ultimately leading to cost savings and high-quality output.
Summary Table:
Parameter | Details |
---|---|
Temperature Range | 200°C to 2500°C, depending on application (e.g., cement: ~1450°C). |
Indirect Kiln Temp | Furnace tube: 1200°C–1300°C; material: below 1150°C. |
Rotation Speed | 0.5 to 5 rpm, adjustable for material flow and efficiency. |
Heating Zones | Drying, heating, reaction, and soaking zones for optimal material processing. |
Control Mechanisms | Ring dams, advanced systems for real-time monitoring and adjustments. |
Ready to optimize your industrial processes with rotary kilns? Contact us today for expert guidance!