RF sputtering is a specialized thin-film deposition technique that utilizes radio frequency (RF) power to sputter target materials, particularly insulating (non-conductive) materials, onto a substrate. The process operates at a fixed frequency of 13.56 MHz, which prevents charge buildup on the target surface, a common issue in DC sputtering. By alternating the electrical potential between positive and negative cycles, RF sputtering ensures continuous ion bombardment and material ejection, enabling the deposition of high-quality thin films. This method is widely used in industries such as semiconductors and electronics due to its ability to handle insulating materials and maintain process stability.
Key Points Explained:
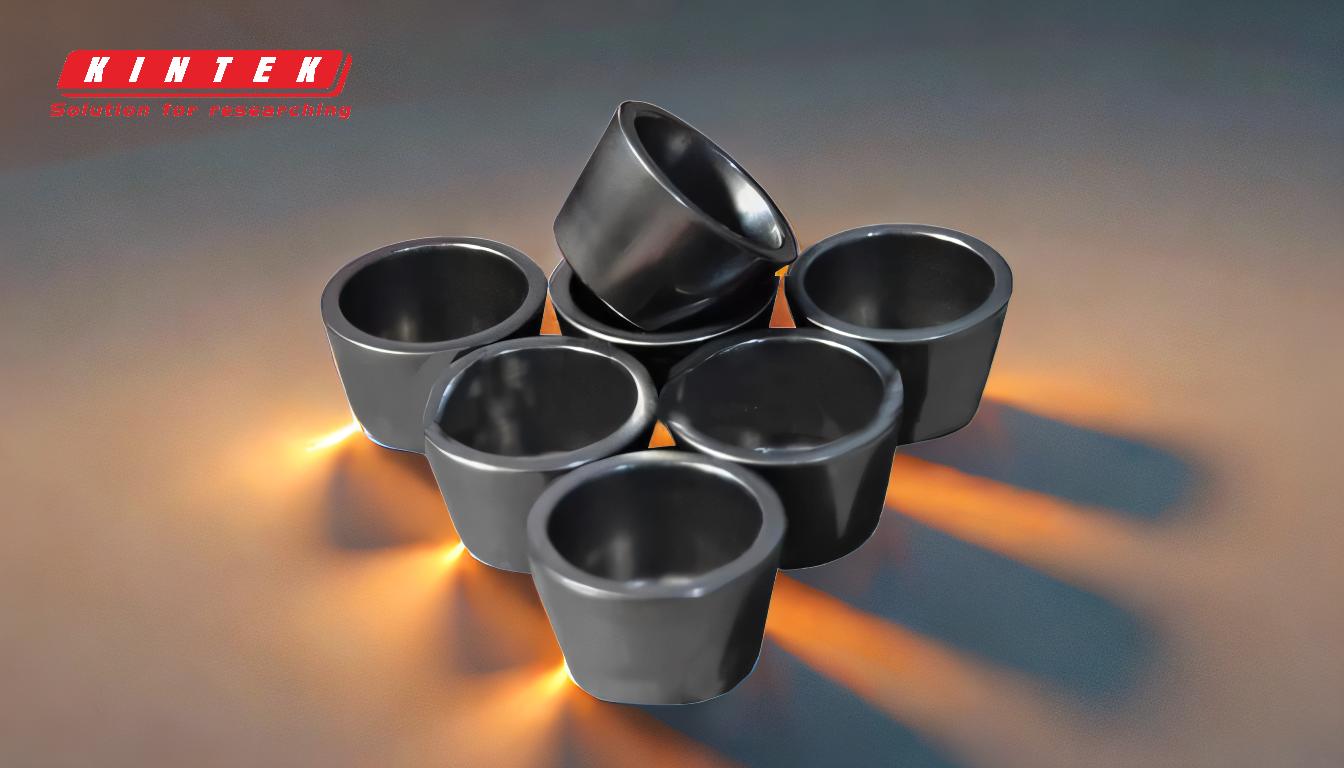
-
Basic Setup of RF Sputtering:
- RF sputtering involves a cathode (target material) and an anode (substrate holder) connected in series with a blocking capacitor.
- The capacitor is part of an impedance-matching network that optimizes power transfer from the RF source to the plasma discharge.
- The RF power supply typically operates at 13.56 MHz, a frequency chosen to minimize interference with communication systems.
-
Role of Alternating Electrical Potential:
- The RF power alternates the electrical potential of the current, creating two distinct cycles: positive and negative.
- In the positive cycle, the target acts as an anode, attracting electrons and creating a negative bias on the target surface.
- In the negative cycle, the target acts as a cathode, attracting positively charged gas ions that bombard the target, ejecting atoms and ions toward the substrate.
-
Prevention of Charge Buildup:
- Charge buildup is a significant issue when sputtering insulating materials, as it can lead to arcing and process instability.
- The alternating potential in RF sputtering "cleans" the target surface during each cycle, preventing charge accumulation.
- This is particularly important for insulating targets, where a constant negative voltage would otherwise halt the sputtering process.
-
Mechanism of Ion Bombardment:
- During the negative cycle, positively charged ions from the plasma are accelerated toward the negatively biased target.
- These ions collide with the target material, ejecting atoms and ions in a process called sputtering.
- The ejected particles travel through the vacuum environment and deposit onto the substrate, forming a thin film.
-
Advantages of RF Sputtering:
- Deposition of Insulating Materials: RF sputtering is uniquely suited for depositing non-conductive materials, which are challenging to sputter using DC methods.
- Stable Process: The alternating potential ensures continuous ion bombardment and material ejection, maintaining process stability.
- High-Quality Films: The controlled environment and precise power delivery result in uniform and high-quality thin films.
-
Applications of RF Sputtering:
- RF sputtering is widely used in the semiconductor industry for depositing dielectric layers and other insulating materials.
- It is also employed in the electronics industry for creating thin films in devices such as sensors, displays, and solar cells.
- The technique is essential for applications requiring precise control over film composition and thickness.
-
Comparison with DC Sputtering:
- Unlike DC sputtering, which is limited to conductive targets, RF sputtering can handle both conductive and insulating materials.
- The alternating potential in RF sputtering eliminates the issue of charge buildup, making it more versatile and reliable for certain applications.
- However, RF sputtering systems are typically more complex and expensive due to the need for impedance matching and RF power supplies.
-
Impedance Matching and Power Delivery:
- The impedance-matching network ensures maximum power transfer from the RF source to the plasma discharge.
- Proper matching minimizes reflected power, improving process efficiency and reducing the risk of equipment damage.
- The blocking capacitor in the circuit prevents DC current from flowing, ensuring the alternating potential is maintained.
-
Plasma Generation and Role of Inert Gas:
- RF sputtering relies on a plasma generated by ionizing an inert gas, such as argon, within the vacuum chamber.
- The energetic RF wave excites the gas atoms, creating positive ions and free electrons.
- The ions are accelerated toward the target during the negative cycle, initiating the sputtering process.
-
Importance of Frequency (13.56 MHz):
- The 13.56 MHz frequency is chosen because it falls within the Industrial, Scientific, and Medical (ISM) radio band, minimizing interference with other communication systems.
- This frequency also ensures efficient energy transfer to the plasma while maintaining process stability.
By understanding these key points, equipment and consumable purchasers can better evaluate the suitability of RF sputtering systems for their specific applications, ensuring optimal performance and cost-effectiveness.
Summary Table:
Key Aspect | Details |
---|---|
Frequency | Operates at 13.56 MHz to prevent charge buildup and ensure stability. |
Target Materials | Ideal for insulating (non-conductive) materials, unlike DC sputtering. |
Mechanism | Alternating electrical potential enables continuous ion bombardment. |
Advantages | - Deposits insulating materials - Stable process - High-quality films |
Applications | - Semiconductors - Electronics (sensors, displays, solar cells) |
Comparison with DC Sputtering | Handles both conductive and insulating materials, but more complex and costly. |
Need an RF sputtering system for your application? Contact us today to get started!