Thermal evaporation is a physical vapor deposition (PVD) technique used to create thin films by heating a target material in a vacuum chamber until it evaporates. The vaporized material then travels through the vacuum and deposits onto a substrate, forming a thin, uniform coating. This process relies on resistive heating, where an electric current passes through a source (such as a boat or coil) to generate the necessary heat. Thermal evaporation is widely used in industries like electronics, optics, and solar cell manufacturing to deposit metals such as aluminum and silver. The method is valued for its simplicity, precision, and ability to produce high-purity films.
Key Points Explained:
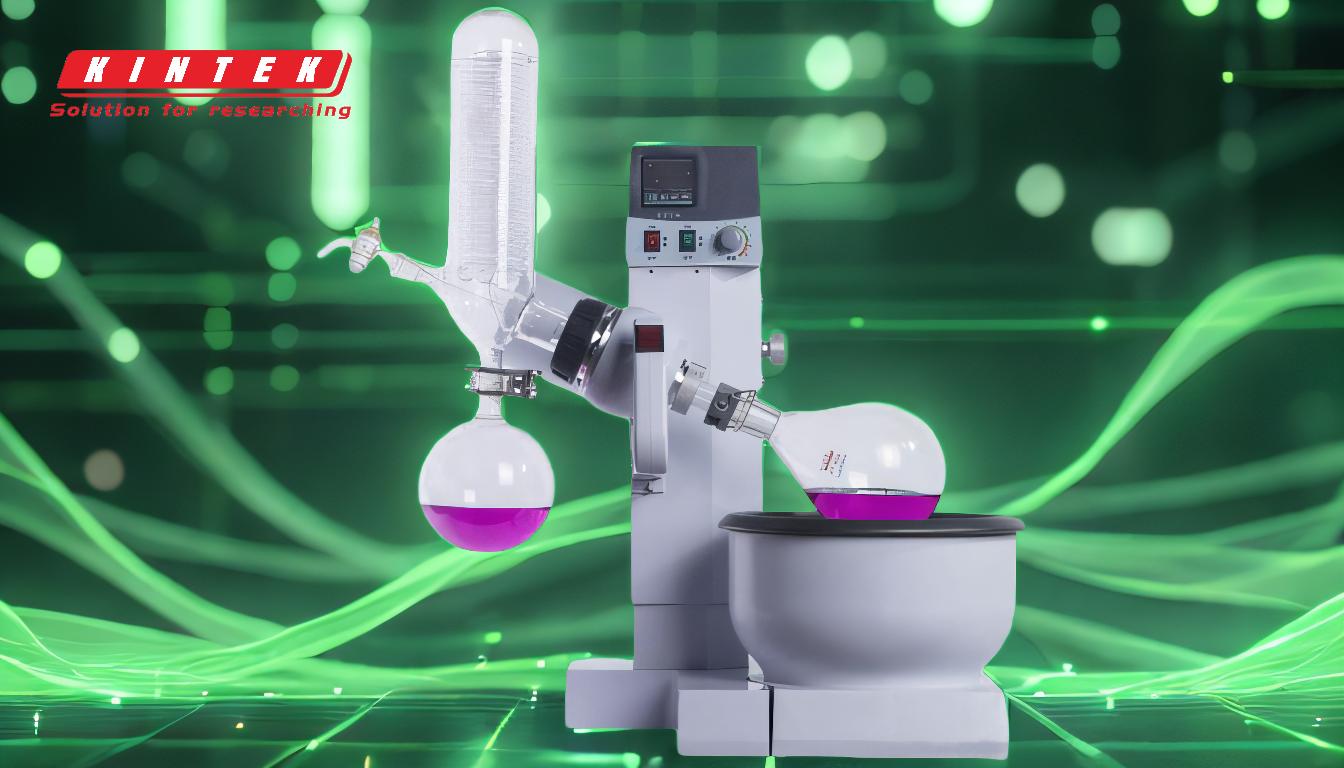
-
Definition and Purpose of Thermal Evaporation
- Thermal evaporation is a physical vapor deposition (PVD) process used to create thin films on substrates.
- It involves heating a target material until it evaporates, allowing the vapor to deposit onto a substrate in a vacuum environment.
- This technique is commonly used in industries such as electronics, optics, and renewable energy for applications like OLEDs, solar cells, and thin-film transistors.
-
Mechanism of Thermal Evaporation
- The target material is placed in an evaporation source (e.g., a boat, coil, or basket) within a vacuum chamber.
- An electric current is passed through the source, generating heat through electrical resistance (resistive heating).
- The material is heated to its evaporation point, where it transitions from a solid or liquid phase to a gaseous phase.
- The vaporized atoms or molecules travel through the vacuum and deposit onto the substrate, forming a thin film.
-
Role of Heat and Energy in Evaporation
- Heat provides energy to the molecules of the target material, increasing their kinetic energy and collision frequency.
- As the material reaches its evaporation point, the molecules gain sufficient energy to overcome the binding forces of the solid or liquid phase and transition into the gas phase.
- The maximum vapor production occurs when the material reaches its boiling temperature.
-
Components of the Thermal Evaporation System
- Vacuum Chamber: Provides a low-pressure environment to minimize contamination and ensure efficient vapor travel.
- Evaporation Source: Typically a resistance boat or coil made of high-melting-point materials like tungsten or molybdenum.
- Substrate Holder: Positions the substrate above the evaporation source to receive the vaporized material.
- Power Supply: Supplies the electric current needed to heat the evaporation source.
-
Advantages of Thermal Evaporation
- Simplicity: The process is straightforward and easy to control.
- High Purity: The vacuum environment minimizes contamination, resulting in high-purity thin films.
- Versatility: Suitable for depositing a wide range of materials, including metals like aluminum, silver, and gold.
- Precision: Allows for precise control over film thickness and uniformity.
-
Applications of Thermal Evaporation
- Electronics: Used to deposit metal layers in OLEDs, thin-film transistors, and semiconductor devices.
- Optics: Creates reflective and anti-reflective coatings for lenses and mirrors.
- Solar Cells: Deposits conductive layers in photovoltaic devices.
- Decorative Coatings: Produces metallic finishes for consumer products.
-
Limitations of Thermal Evaporation
- Material Compatibility: Limited to materials with relatively low evaporation temperatures.
- Uniformity Challenges: Achieving uniform coatings on complex or uneven substrates can be difficult.
- Energy Efficiency: Requires significant energy to maintain high temperatures and vacuum conditions.
-
Comparison with Other PVD Techniques
- Thermal evaporation is simpler and more cost-effective than methods like sputtering or pulsed laser deposition.
- However, it may not achieve the same level of film adhesion or uniformity as more advanced techniques.
-
Future Trends in Thermal Evaporation
- Development of advanced evaporation sources for higher melting-point materials.
- Integration with other deposition techniques for hybrid thin-film fabrication.
- Enhanced process automation and control for improved reproducibility and scalability.
By understanding the thermal evaporation process, equipment purchasers can make informed decisions about the suitability of this technique for their specific applications, ensuring optimal performance and cost-effectiveness.
Summary Table:
Aspect | Details |
---|---|
Definition | A PVD technique for creating thin films by evaporating materials in a vacuum. |
Key Components | Vacuum chamber, evaporation source (boat/coil), substrate holder, power supply. |
Advantages | Simplicity, high purity, versatility, and precise film thickness control. |
Applications | Electronics (OLEDs, semiconductors), optics (lenses, mirrors), solar cells. |
Limitations | Limited to low-evaporation-temperature materials; uniformity challenges. |
Comparison | Simpler and more cost-effective than sputtering or pulsed laser deposition. |
Discover how thermal evaporation can enhance your production process—contact our experts today!