Thin film deposition thickness is a critical parameter influenced by various factors such as deposition techniques, material properties, and process conditions. The thickness typically ranges from nanometers to micrometers and is measured using advanced techniques like ellipsometry, profilometry, and interferometry. The deposition rate, uniformity, and final thickness are affected by parameters like target-substrate distance, power, temperature, and the nature of the substrate. Understanding these factors is essential for optimizing thin film properties to meet specific application requirements in fields such as photonics, optics, electronics, and mechanics.
Key Points Explained:
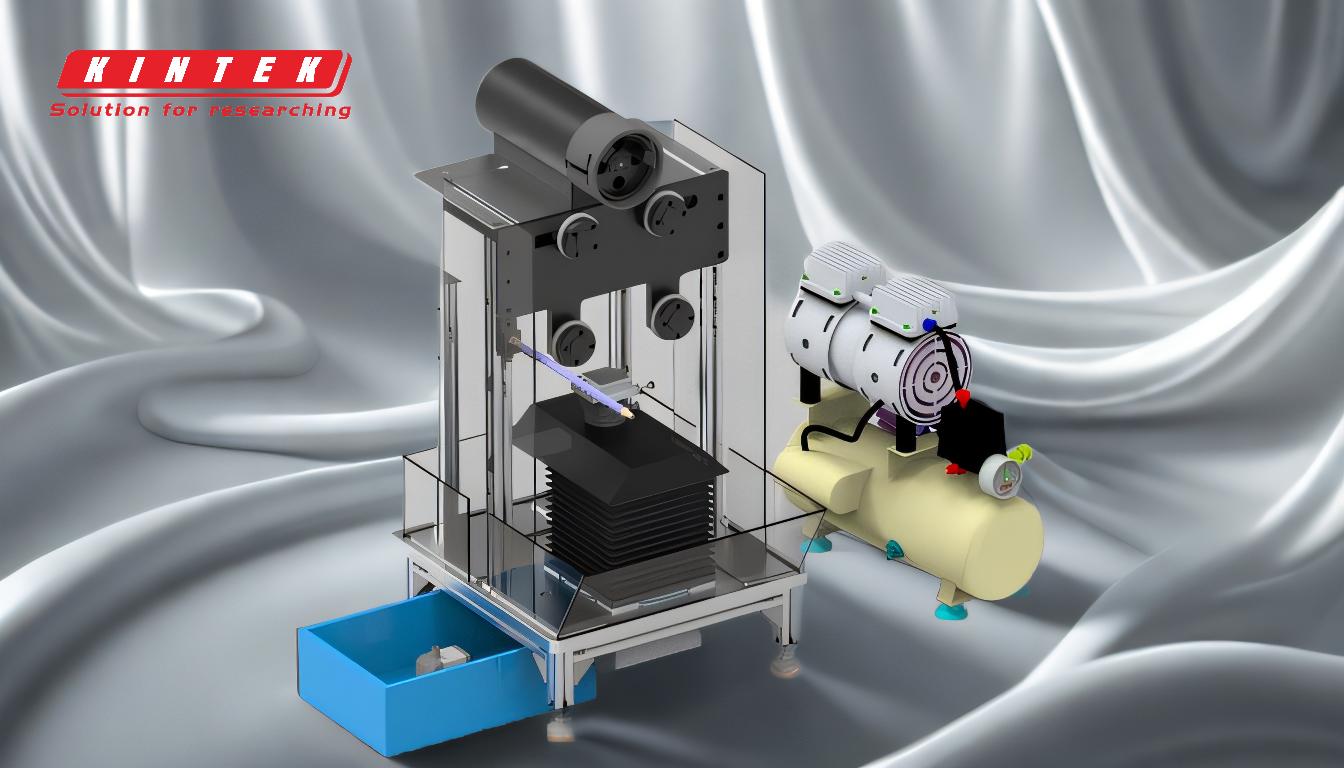
-
Thin Film Thickness Range:
- Thin films are typically measured in nanometers, with thicknesses ranging from a few nanometers to several micrometers depending on the application and deposition method.
- For example, in sputtering, the thickness can vary based on the duration of the process and the energy level of the coating particles.
-
Measurement Techniques:
- Quartz Crystal Microbalance (QCM): Measures mass changes during deposition to infer thickness.
- Ellipsometry: Analyzes the change in polarization of light reflected from the film to determine thickness and refractive index.
- Profilometry: Uses a stylus or optical method to measure the surface profile and thickness.
- Interferometry: Relies on the interference of light waves to calculate thickness by analyzing the interference pattern.
-
Factors Influencing Thickness:
- Deposition Rate: Controlled by the size of the erosion zone, target-substrate distance, power, and temperature. Higher power and shorter distances generally increase the deposition rate.
- Material Properties: The refractive index and mass of the material affect the interference patterns and thickness calculations.
- Process Parameters: Deposition temperature, residual gas composition, and substrate nature play significant roles in determining the final thickness and uniformity.
-
Application-Specific Requirements:
- Thin films must meet specific criteria based on their intended use, such as optical transparency, electrical conductivity, or mechanical durability.
- For instance, optical films require precise thickness control to achieve desired light interference effects, while electronic films may need specific thicknesses to ensure proper conductivity.
-
Uniformity and Control:
- Thickness uniformity is crucial for consistent film properties. It decreases with increasing target-substrate distance and smaller erosion zones.
- Advanced deposition systems often incorporate real-time monitoring and feedback mechanisms to maintain uniformity and control thickness.
-
Practical Considerations for Purchasers:
- When selecting equipment or consumables for thin film deposition, consider the following:
- The required thickness range and uniformity for your application.
- Compatibility of the deposition system with the materials and substrates you plan to use.
- Availability of real-time thickness monitoring and control features.
- The impact of process parameters (power, temperature, distance) on deposition rate and film quality.
- When selecting equipment or consumables for thin film deposition, consider the following:
By understanding these key points, purchasers can make informed decisions to ensure that the thin film deposition process meets their specific requirements, resulting in high-quality films tailored to their application needs.
Summary Table:
Key Aspect | Details |
---|---|
Thickness Range | Nanometers to micrometers, depending on application and deposition method. |
Measurement Techniques | QCM, Ellipsometry, Profilometry, Interferometry. |
Influencing Factors | Deposition rate, material properties, process parameters (power, temperature, distance). |
Application Requirements | Optical transparency, electrical conductivity, mechanical durability. |
Uniformity & Control | Real-time monitoring and feedback mechanisms ensure consistent thickness. |
Purchasing Considerations | Thickness range, system compatibility, real-time monitoring, process impact. |
Ensure your thin film deposition meets precision standards—contact our experts today for tailored solutions!