A pyrolysis reactor is a specialized equipment used to thermally decompose materials in the absence of oxygen, converting them into smaller molecules, gases, liquids, or solid residues. It is widely applied in waste management, chemical production, and energy generation. Pyrolysis reactors are essential for processing high-caloric waste streams, reducing sludge volumes, degrading complex oil-based flows, and converting biomass into bio-oil or biochar. They also play a critical role in producing bulk chemicals like ethylene and specialty chemicals such as tetrafluoroethylene. Additionally, pyrolysis reactors are used to recycle plastics, tires, and rubber into fuel oil, contributing to environmental sustainability by reducing pollution and promoting waste-to-energy solutions.
Key Points Explained:
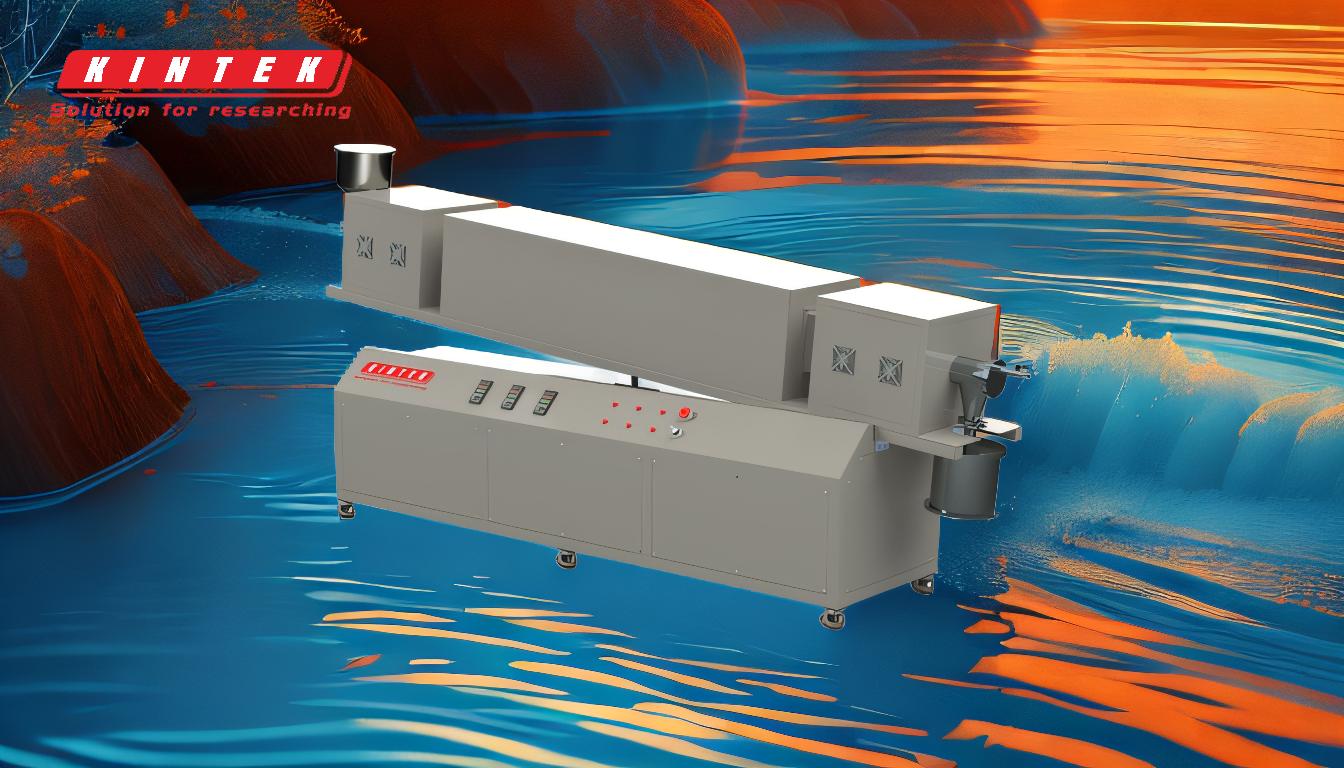
-
Definition and Function of a Pyrolysis Reactor:
- A pyrolysis reactor is a closed system that thermally decomposes materials in an oxygen-free environment, breaking them down into gases, liquids, or solid residues.
- It operates based on thermodynamic principles and relies on an external heat source to drive the decomposition process.
-
Applications in Waste Management:
- Sludge Reduction: Pyrolysis reactors are used to reduce the volume of sludge generated during physico-chemical water purification processes.
- Complex Waste Streams: They are effective in degrading complex oil-based waste flows and processing high-caloric waste materials.
- Plastic and Tire Recycling: Pyrolysis reactors convert waste plastics, tires, and rubber into fuel oil, addressing environmental pollution and promoting recycling.
-
Biomass and Biofuel Production:
- Pyrolysis reactors are instrumental in processing biomass to produce bio-oil, biochar, and syngas, which are renewable energy sources.
- They are also used to produce charcoal and activated carbon from wood, contributing to sustainable material production.
-
Chemical Industry Applications:
- Bulk Chemicals: Pyrolysis reactors are used to produce ethylene, vinyl chloride monomer (VCM), and other bulk chemicals from petroleum, coal, and wood.
- Specialty Chemicals: They enable the production of specialty chemicals like tetrafluoroethylene, which are essential for various industrial applications.
- Hydrogen Production: Pyrolysis reactors can convert natural gas into hydrogen gas and solid carbon char, supporting clean energy initiatives.
-
Environmental Benefits:
- Pyrolysis reactors contribute to a pollution-free and eco-friendly world by recycling waste materials into valuable products like fuel oil and reducing landfill dependency.
- They help mitigate environmental pollution by processing hazardous waste streams and converting them into usable resources.
-
Types of Pyrolysis Reactors:
- Rotary Kiln Reactors: These are commonly used for continuous processing of materials and are suitable for large-scale operations.
- Fluidized Bed Reactors: These reactors provide efficient heat transfer and are ideal for processing fine particles or biomass.
-
Future Prospects:
- Pyrolysis reactors have aspirational applications, such as converting waste plastics back into usable oil and producing syngas from biomass, which can further enhance renewable energy production.
- Ongoing advancements in reactor design and technology aim to improve efficiency, scalability, and environmental performance.
In summary, pyrolysis reactors are versatile and essential equipment in waste management, chemical production, and renewable energy generation. They play a pivotal role in converting waste materials into valuable resources, reducing environmental pollution, and supporting sustainable industrial practices.
Summary Table:
Aspect | Details |
---|---|
Definition | A closed system that thermally decomposes materials in an oxygen-free environment. |
Key Applications | Waste management, chemical production, renewable energy generation. |
Waste Management | Reduces sludge, processes oil-based waste, recycles plastics and tires. |
Biomass Production | Converts biomass into bio-oil, biochar, and syngas. |
Chemical Production | Produces bulk chemicals (e.g., ethylene) and specialty chemicals. |
Environmental Impact | Reduces pollution, promotes recycling, and supports waste-to-energy solutions. |
Types of Reactors | Rotary kiln reactors, fluidized bed reactors. |
Future Prospects | Advanced recycling of plastics, syngas production, and improved efficiency. |
Ready to explore how pyrolysis reactors can transform your waste management and energy production? Contact us today to learn more!