Torrefaction is a thermal process used to improve the properties of biomass, making it more suitable for use as a fuel or feedstock in various applications. The process involves heating biomass in the absence of oxygen at temperatures typically between 200°C and 300°C. This results in the removal of moisture and volatile compounds, leaving behind a dry, energy-dense, and hydrophobic material. Torrefied biomass has several advantages, including higher energy density, improved grindability, and better storage and transportation properties. It is commonly used in co-firing with coal, as a feedstock for gasification, or as a standalone fuel in industrial processes. The process also reduces the risk of biological degradation, making it easier to store and handle.
Key Points Explained:
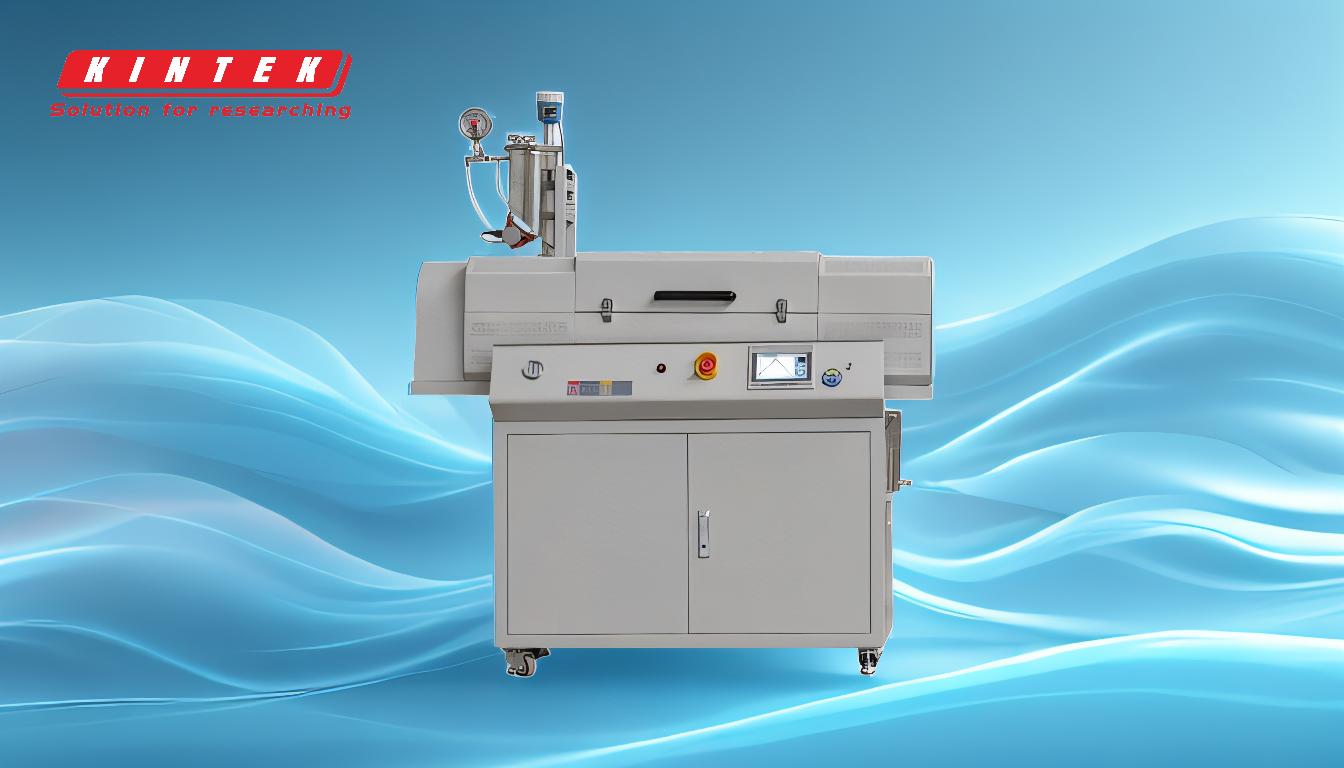
-
Definition and Process of Torrefaction:
- Torrefaction is a thermochemical process where biomass is heated in the absence of oxygen at temperatures ranging from 200°C to 300°C.
- The process removes moisture and volatile organic compounds, resulting in a dry, energy-dense, and hydrophobic material.
- This transformation makes the biomass more stable and easier to handle compared to raw biomass.
-
Benefits of Torrefaction:
- Increased Energy Density: Torrefaction increases the energy content per unit mass of biomass, making it a more efficient fuel source.
- Improved Grindability: The process makes biomass easier to grind, reducing energy consumption in size reduction processes.
- Enhanced Storage and Transportation: Torrefied biomass is hydrophobic, meaning it repels water, which reduces the risk of biological degradation during storage and transportation.
- Reduced Emissions: Torrefaction can lead to lower emissions when the biomass is used as a fuel, as it burns more cleanly compared to raw biomass.
-
Applications of Torrefied Biomass:
- Co-firing with Coal: Torrefied biomass can be mixed with coal in power plants, reducing the carbon footprint of electricity generation.
- Gasification Feedstock: The material is used as a feedstock in gasification processes to produce syngas, which can be further processed into fuels or chemicals.
- Standalone Fuel: Torrefied biomass can be used as a standalone fuel in industrial boilers or for residential heating.
- Pellet Production: The process is often used to produce biomass pellets, which are easier to handle and transport than raw biomass.
-
Economic and Environmental Impact:
- Cost Efficiency: Although the torrefaction process requires energy, the improved properties of the biomass can lead to cost savings in transportation, storage, and processing.
- Sustainability: Torrefaction contributes to the use of renewable energy sources, reducing reliance on fossil fuels and lowering greenhouse gas emissions.
- Waste Reduction: The process can utilize agricultural residues and other waste biomass, turning them into valuable energy resources.
-
Challenges and Considerations:
- Energy Input: The torrefaction process itself requires energy, which must be sourced sustainably to maintain the environmental benefits.
- Technology Development: While torrefaction technology is advancing, further research is needed to optimize the process and reduce costs.
- Market Acceptance: Widespread adoption of torrefied biomass depends on market acceptance and the development of infrastructure for its use and distribution.
In summary, torrefaction is a valuable process for enhancing the properties of biomass, making it a more efficient and sustainable fuel or feedstock. Its benefits include increased energy density, improved grindability, and better storage and transportation properties. However, challenges such as energy input and market acceptance need to be addressed for broader adoption.
Summary Table:
Aspect | Details |
---|---|
Process | Heating biomass at 200°C–300°C without oxygen, removing moisture and volatiles. |
Benefits | Higher energy density, improved grindability, hydrophobic properties. |
Applications | Co-firing with coal, gasification feedstock, standalone fuel, pellet production. |
Economic & Environmental | Cost-efficient, sustainable, reduces waste, lowers emissions. |
Challenges | Energy input, technology development, market acceptance. |
Discover how torrefaction can optimize your biomass use—contact our experts today!