Vacuum evaporation is a process that leverages reduced pressure to lower the boiling point of a liquid, enabling evaporation at lower temperatures. This technique is particularly useful for heat-sensitive substances or liquids with high boiling points, as it minimizes thermal degradation. The process is widely used in applications such as distillation, thin-film deposition, and wastewater treatment. By operating under vacuum conditions, the liquid evaporates more efficiently, and the vapors can be condensed and collected. This mechanism is employed in various equipment, including rotary evaporators, thermal evaporation systems, and advanced vortex evaporators, each tailored for specific applications.
Key Points Explained:
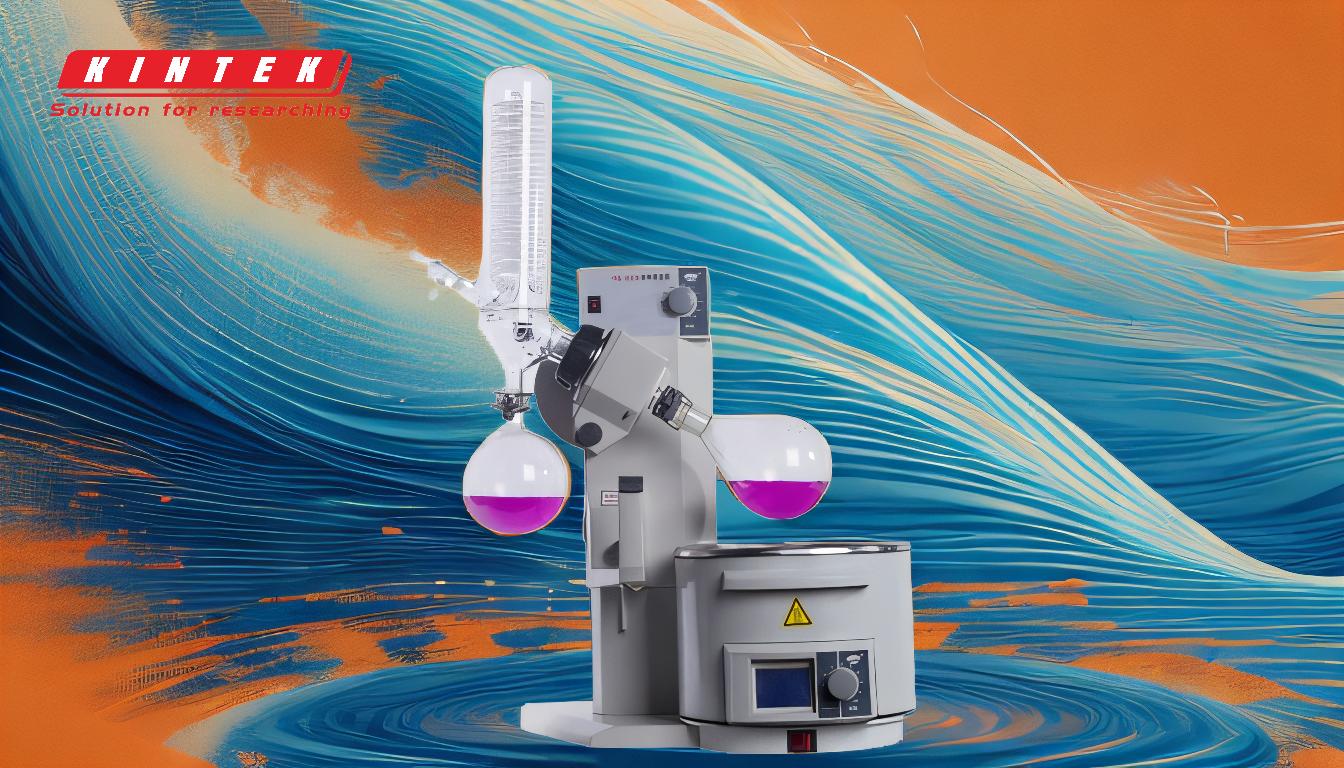
-
Reduction of Boiling Point Under Vacuum:
- Vacuum evaporation works by reducing the pressure in a system, which lowers the boiling point of the liquid. This means that liquids can evaporate at much lower temperatures than their standard boiling points.
- For example, water, which normally boils at 100°C at atmospheric pressure, can boil at significantly lower temperatures (e.g., 40°C or less) under reduced pressure.
- This principle is crucial for handling heat-sensitive materials, as it prevents thermal decomposition or degradation.
-
Mechanism of Vacuum Evaporation:
- The process involves creating a vacuum environment using mechanical pumps, steam jet ejectors, or other vacuum-generating systems.
- Once the pressure is reduced, the liquid begins to evaporate at a lower temperature. The vapors are then condensed back into a liquid form using condensers.
- This mechanism is essential in applications like distillation, where the goal is to separate components based on their boiling points.
-
Applications in Thin-Film Deposition:
- In thermal vacuum evaporation, a solid material is heated in a high vacuum chamber until it produces vapor pressure. The vapor then travels through the vacuum and deposits onto a substrate, forming a thin film.
- This method is part of the Physical Vapor Deposition (PVD) processes and is used in industries like electronics, optics, and coatings.
- The process operates in extremely low pressure ranges (10^-5 to 10^-9 Torr) to ensure high-purity film deposition without interference from gas molecules.
-
Equipment and Techniques:
- Rotary Evaporators: These devices use vacuum and rotation to increase the surface area of the liquid, promoting faster evaporation. They are commonly used in laboratories for solvent removal or concentration of solutions.
- Thermal Evaporation Systems: These systems use resistive heating, electron beams, or other heat sources to vaporize materials in a vacuum chamber.
- Vortex Evaporators: Advanced vortex evaporators combine vacuum pumps, heaters, and cold traps to accelerate evaporation while minimizing sample loss and cross-contamination.
-
Advantages of Vacuum Evaporation:
- Energy Efficiency: By lowering the boiling point, less heat energy is required, making the process more energy-efficient.
- Preservation of Heat-Sensitive Materials: The reduced temperatures prevent damage to delicate substances, such as pharmaceuticals or biological samples.
- High-Purity Output: The vacuum environment ensures minimal contamination, making it ideal for applications requiring high-purity materials.
-
Challenges and Considerations:
- Equipment Complexity: Vacuum systems require specialized equipment, such as pumps and condensers, which can be costly and require maintenance.
- Process Control: Precise control of pressure and temperature is necessary to ensure consistent results.
- Sample Loss in Vortex Evaporators: Traditional vortex evaporators may suffer from sample loss due to insufficient g force, though advanced designs mitigate this issue.
-
Industrial and Environmental Applications:
- Wastewater Treatment: Vacuum evaporation is used to separate water from contaminants with high boiling points, enabling the recovery of clean water and concentration of waste for disposal.
- Chemical and Pharmaceutical Industries: The process is widely used for solvent recovery, concentration of solutions, and purification of compounds.
- Electronics and Optics: Thin-film deposition via vacuum evaporation is critical for manufacturing semiconductors, optical coatings, and other advanced materials.
-
Comparison with Other Evaporation Methods:
- Centrifugal Evaporation: Unlike vortex evaporation, centrifugal evaporation uses higher g forces to prevent bumping and sample loss, making it more suitable for sensitive applications.
- Atmospheric Evaporation: Traditional evaporation methods at atmospheric pressure require higher temperatures, which can damage heat-sensitive materials and consume more energy.
By understanding the vacuum evaporation mechanism, users can select the appropriate equipment and techniques for their specific needs, whether in research, industrial production, or environmental applications.
Summary Table:
Key Aspect | Details |
---|---|
Process | Reduces pressure to lower boiling points, enabling evaporation at low temps. |
Applications | Distillation, thin-film deposition, wastewater treatment, and more. |
Equipment | Rotary evaporators, thermal evaporation systems, vortex evaporators. |
Advantages | Energy-efficient, preserves heat-sensitive materials, high-purity output. |
Challenges | Equipment complexity, precise process control, potential sample loss. |
Discover how vacuum evaporation can optimize your processes—contact our experts today!