The vacuum pyrolysis method is a specialized thermal decomposition process that occurs under reduced pressure, enabling the efficient breakdown of organic materials at lower temperatures compared to conventional pyrolysis. This method is particularly advantageous for processing heat-sensitive materials, as the vacuum system lowers the boiling points and decomposition temperatures of the substrates. It is widely used in waste management, biofuel production, and chemical recovery, offering benefits such as reduced energy consumption, minimized environmental impact, and enhanced product quality. Vacuum pyrolysis reactors can be adapted from existing pyrolysis systems by integrating a vacuum system, making it a versatile and scalable solution for various applications.
Key Points Explained:
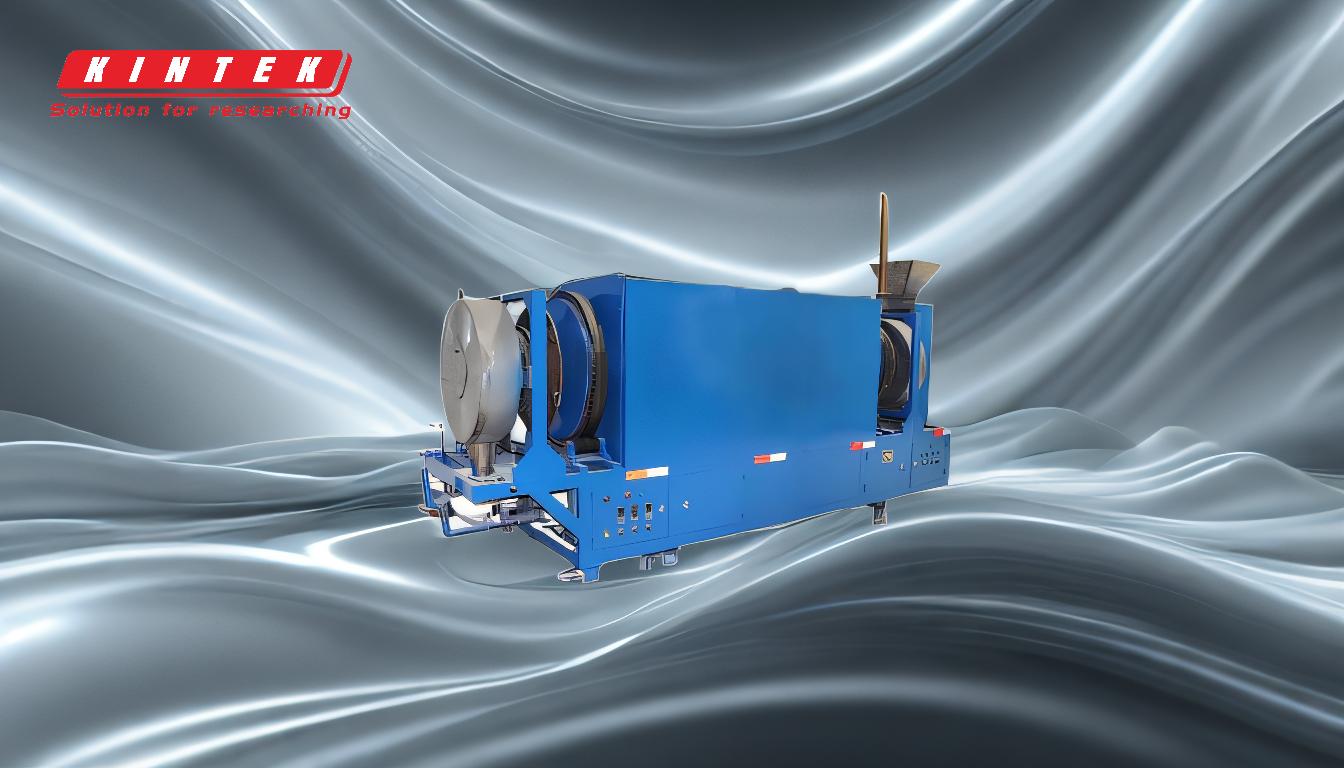
-
Definition of Vacuum Pyrolysis:
- Vacuum pyrolysis is a thermal decomposition process that operates under reduced pressure, facilitated by a vacuum system. This method lowers the boiling points and decomposition temperatures of organic materials, enabling efficient breakdown at lower temperatures compared to atmospheric pyrolysis.
-
Mechanism of Vacuum Pyrolysis:
- The vacuum system reduces the internal pressure of the reactor, which in turn lowers the energy required for thermal decomposition. This allows for rapid and efficient processing of feedstocks, particularly those that are heat-sensitive or prone to degradation at higher temperatures.
-
Applications of Vacuum Pyrolysis:
- Waste Management: Converts organic waste materials, such as plastics, rubber, and biomass, into valuable products like biofuels, chemicals, and char, reducing landfill waste and environmental pollution.
- Biofuel Production: Produces liquid hydrocarbons and other energy-dense products that can be used as alternatives to fossil fuels.
- Chemical Recovery: Enables the extraction of valuable chemicals from waste streams, reducing the need for virgin raw materials.
-
Advantages of Vacuum Pyrolysis:
- Lower Energy Consumption: The reduced pressure allows for decomposition at lower temperatures, saving energy.
- Enhanced Product Quality: Minimizes thermal degradation of sensitive materials, preserving the quality of the end products.
- Environmental Benefits: Reduces greenhouse gas emissions, water pollution, and reliance on imported energy resources by utilizing domestic waste materials.
- Scalability and Flexibility: Can be implemented at small scales and remote locations, reducing transport and handling costs.
-
Comparison with Other Pyrolysis Methods:
- Slow Pyrolysis: Operates at lower heating rates and longer residence times, producing more char and less liquid. Vacuum pyrolysis, by contrast, is faster and more efficient.
- Fast Pyrolysis: Focuses on maximizing liquid yield but requires higher temperatures. Vacuum pyrolysis achieves similar results at lower temperatures.
- Flash Pyrolysis: Extremely rapid process with very short residence times, often leading to less control over product quality. Vacuum pyrolysis offers better control and efficiency.
-
Integration of Vacuum Systems:
- Any type of pyrolysis reactor can be converted into a vacuum pyrolysis reactor by installing a vacuum system. This adaptability makes vacuum pyrolysis a versatile option for various industries.
-
Economic and Social Benefits:
- Job Creation: The implementation of vacuum pyrolysis systems can create jobs in waste management, engineering, and chemical processing.
- Public Health: By reducing waste and pollution, vacuum pyrolysis contributes to cleaner environments and improved public health.
-
Challenges and Considerations:
- Initial Investment: The installation of vacuum systems and specialized reactors may require significant upfront costs.
- Operational Complexity: Managing vacuum conditions and ensuring consistent performance can be technically challenging.
- Feedstock Variability: The efficiency of vacuum pyrolysis can vary depending on the type and quality of the feedstock used.
In summary, vacuum pyrolysis is a highly efficient and versatile method for converting organic waste into valuable products while minimizing environmental impact. Its ability to operate at lower temperatures and reduced pressure makes it particularly suitable for processing heat-sensitive materials, offering significant advantages over traditional pyrolysis methods. However, careful consideration of initial costs and operational complexities is necessary for successful implementation.
Summary Table:
Aspect | Details |
---|---|
Definition | Thermal decomposition under reduced pressure, lowering decomposition temps. |
Applications | Waste management, biofuel production, chemical recovery. |
Advantages | Lower energy use, enhanced product quality, environmental benefits. |
Challenges | High initial costs, operational complexity, feedstock variability. |
Learn how vacuum pyrolysis can revolutionize your waste management—contact us today!