The vapor phase deposition process, particularly chemical vapor deposition (CVD), is a sophisticated method used to create thin films and nanomaterials by exposing a substrate to volatile precursors in vapor form. These precursors react or decompose on the substrate surface, often under elevated temperatures and in an evacuated chamber, to form the desired deposit. The process involves several steps, including the transport of reacting gaseous species to the surface, adsorption, surface-catalyzed reactions, surface diffusion, nucleation, growth, and desorption of gaseous reaction products. CVD is widely used in industries for depositing metals, semiconductors, and ceramics, offering advantages such as high-quality film density and coverage. Plasma-enhanced chemical vapor deposition (PECVD) is a variant that uses energy excitation to convert the working material into a plasma state, enabling lower deposition temperatures and reduced energy consumption.
Key Points Explained:
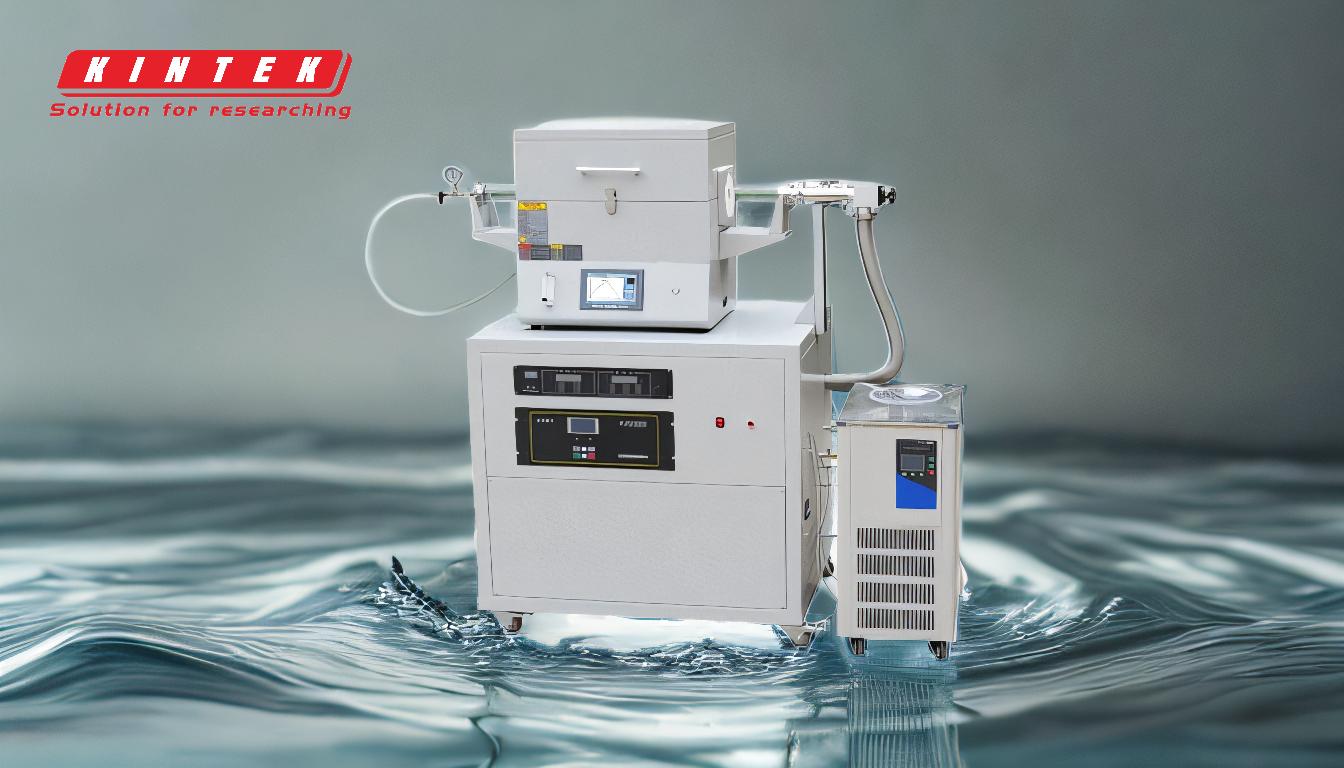
-
Definition and Overview of Chemical Vapor Deposition (CVD):
- CVD is a process where gaseous reactants are introduced into a chamber, and through chemical reactions, a solid material is deposited onto a substrate.
- The process is widely used in the semiconductor industry, as well as for creating protective coatings and nanomaterials.
- The chemical vapor deposition machine is a key piece of equipment used in this process, facilitating the precise control of temperature, pressure, and gas flow.
-
Steps Involved in the CVD Process:
- Transport of Reacting Gases: The gaseous species are transported to the substrate surface.
- Adsorption: The gases adsorb onto the substrate surface.
- Surface Reactions: Heterogeneous surface-catalyzed reactions occur, leading to the formation of the desired material.
- Surface Diffusion: The species diffuse across the surface to growth sites.
- Nucleation and Growth: The material nucleates and grows into a thin film.
- Desorption and Transport of Byproducts: Gaseous reaction products desorb and are transported away from the surface.
-
Types of CVD Processes:
- Thermal CVD: Uses heat to drive the chemical reactions, typically at high temperatures (250-350°C).
- Plasma-Enhanced CVD (PECVD): Utilizes plasma to lower the required deposition temperature and enhance reaction rates, making it suitable for temperature-sensitive substrates.
- Atomic Layer Deposition (ALD): A variant of CVD that allows for precise control of film thickness at the atomic level.
-
Comparison with Physical Vapor Deposition (PVD):
- Deposition Mechanism: PVD involves physical processes like evaporation or sputtering, whereas CVD relies on chemical reactions.
- Material Range: Both can deposit a wide range of materials, but CVD is particularly effective for metals, semiconductors, and ceramics.
- Deposition Rate: PVD generally has lower deposition rates compared to CVD.
- Substrate Temperature: PVD typically does not require heating the substrate, while CVD often involves elevated temperatures.
- Film Quality: CVD films tend to have better density and coverage, while PVD films may offer better surface smoothness and adhesion.
-
Applications of CVD:
- Semiconductor Manufacturing: Used for depositing thin films of silicon, silicon dioxide, and other materials in integrated circuits.
- Protective Coatings: CVD is used to apply wear-resistant and corrosion-resistant coatings on tools and components.
- Nanomaterials: CVD is instrumental in the synthesis of carbon nanotubes, graphene, and other nanomaterials.
-
Advantages of CVD:
- High-Quality Films: CVD produces films with excellent density, uniformity, and coverage.
- Versatility: Capable of depositing a wide range of materials, including metals, semiconductors, and ceramics.
- Scalability: Suitable for both small-scale research and large-scale industrial production.
-
Challenges and Considerations:
- High Temperatures: Many CVD processes require high temperatures, which can limit the types of substrates that can be used.
- Complexity: The process involves precise control of multiple parameters, including temperature, pressure, and gas flow.
- Cost: The equipment and operational costs for CVD can be high, particularly for advanced variants like PECVD.
In summary, the vapor phase deposition process, particularly CVD, is a versatile and powerful technique for creating high-quality thin films and nanomaterials. Its applications span across various industries, from semiconductors to protective coatings, making it an essential technology in modern manufacturing and research.
Summary Table:
Aspect | Details |
---|---|
Definition | Process of depositing thin films via chemical reactions of gaseous precursors. |
Key Steps | Transport, adsorption, surface reactions, diffusion, nucleation, growth, desorption. |
Types of CVD | Thermal CVD, Plasma-Enhanced CVD (PECVD), Atomic Layer Deposition (ALD). |
Applications | Semiconductor manufacturing, protective coatings, nanomaterials. |
Advantages | High-quality films, versatility, scalability. |
Challenges | High temperatures, process complexity, equipment cost. |
Discover how CVD can revolutionize your manufacturing process—contact our experts today!