Sputtering is a physical vapor deposition (PVD) technique where atoms from a solid target material are ejected into a gas phase due to bombardment by high-energy ions. These ejected atoms then condense onto a substrate to form a thin film. DC sputtering, a specific type of sputtering, uses direct current to create a plasma that ionizes gas molecules, which then bombard the target material, causing atoms to be ejected and deposited onto the substrate. The voltage applied in DC sputtering typically ranges from a few hundred volts to several thousand volts, depending on the specific application, target material, and system configuration. This voltage is crucial for accelerating ions toward the target and maintaining the plasma necessary for the sputtering process.
Key Points Explained:
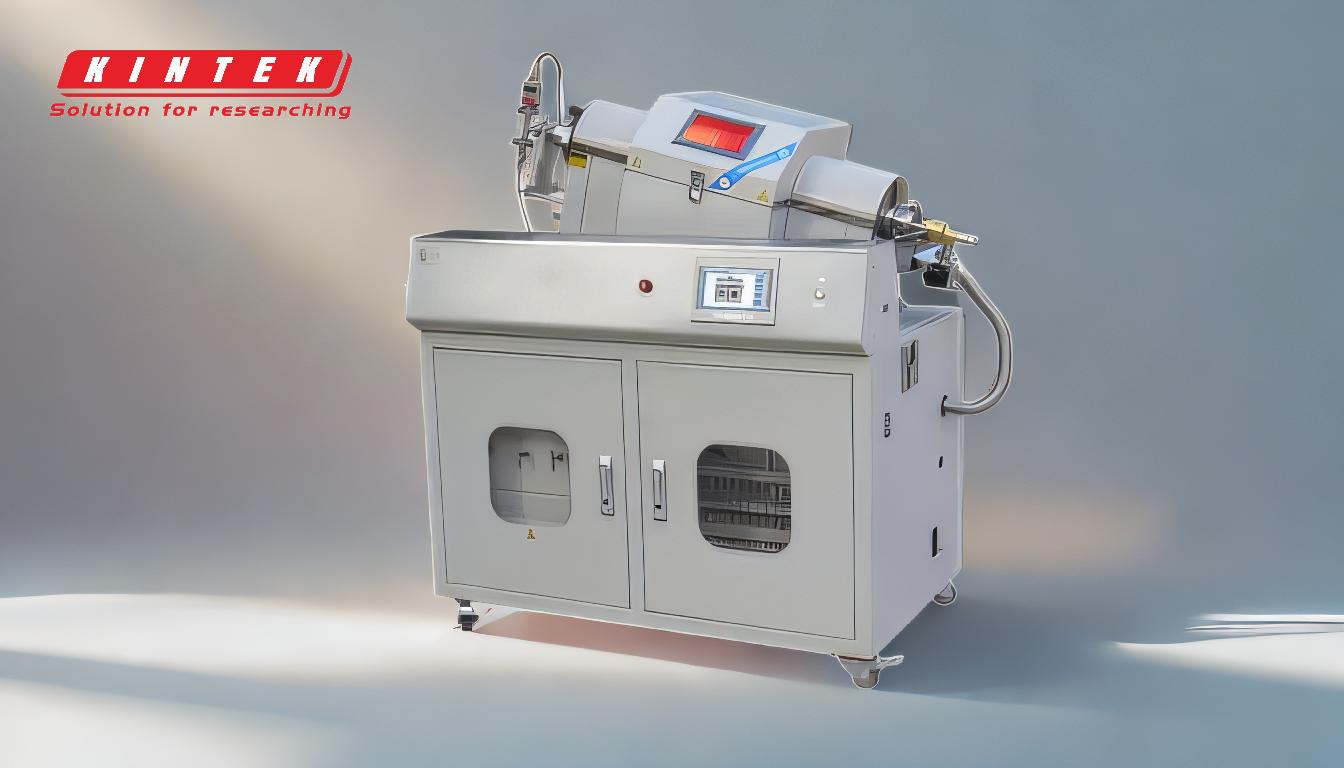
-
DC Sputtering Process:
- DC sputtering involves applying a direct current voltage to a target material within a vacuum chamber filled with an inert gas, such as argon.
- The applied voltage ionizes the gas, creating a plasma of positively charged ions and free electrons.
- These ions are accelerated toward the negatively charged target (cathode), where they collide with the target material, ejecting atoms into the gas phase.
- The ejected atoms then travel through the plasma and deposit onto the substrate, forming a thin film.
-
Voltage in DC Sputtering:
- The voltage used in DC sputtering typically ranges from 200 to 1000 volts, though it can vary depending on the target material, gas pressure, and system design.
- Higher voltages increase the energy of the ions, leading to more efficient sputtering and higher deposition rates. However, excessive voltage can damage the target material or substrate.
- The voltage must be carefully controlled to ensure a stable plasma and consistent thin-film deposition.
-
Role of Voltage in Plasma Formation:
- When a DC voltage is applied, free electrons are accelerated away from the negatively charged cathode.
- These electrons collide with neutral gas atoms, stripping them of their outer electrons and creating positively charged ions.
- The ions are then accelerated toward the cathode, striking it and ejecting material and additional free electrons.
- The free electrons can recombine with ions, releasing energy as photons, which causes the plasma to glow.
-
DC Magnetron Sputtering:
- In DC magnetron sputtering, magnets are placed behind the cathode to trap electrons near the target surface.
- This increases the efficiency of gas ionization and allows for higher deposition rates at lower gas pressures.
- The voltage in magnetron sputtering is often lower than in standard DC sputtering due to the enhanced ionization efficiency provided by the magnetic field.
-
Factors Influencing Voltage Requirements:
- Target Material: Different materials require different voltages due to variations in their sputtering yield (the number of atoms ejected per incident ion).
- Gas Pressure: Lower gas pressures typically require higher voltages to maintain the plasma.
- System Configuration: The design of the sputtering system, including the distance between the target and substrate, can influence the required voltage.
-
Applications of DC Sputtering:
- DC sputtering is widely used in industries such as semiconductor manufacturing, optics, and decorative coatings.
- It is particularly suitable for depositing conductive materials, such as metals, due to the direct current nature of the process.
In summary, the voltage in DC sputtering is a critical parameter that influences the efficiency and quality of the thin-film deposition process. It typically ranges from a few hundred to several thousand volts, depending on the specific application and system configuration. Proper control of the voltage ensures stable plasma formation, efficient sputtering, and consistent thin-film deposition.
Summary Table:
Key Aspect | Details |
---|---|
Voltage Range | 200 to 1000 volts, depending on target material, gas pressure, and system. |
Role of Voltage | Accelerates ions, maintains plasma, and ensures consistent thin-film deposition. |
Factors Influencing Voltage | Target material, gas pressure, and system configuration. |
Applications | Semiconductor manufacturing, optics, decorative coatings. |
Need help optimizing your DC sputtering process? Contact our experts today for tailored solutions!