Pelletizing machines, also known as agglomeration machines, work on the principle of gathering fine solid particles and clustering them into larger, more manageable forms such as spheres, bricks, or cylindrical pellets. This process is crucial in industries where handling fine powders or dust is challenging, as it reduces material loss by minimizing dust generation. The pelletizing process not only improves material efficiency but also enhances the handling, storage, and transportation of materials. Below, we delve into the key principles and benefits of pelletizing machines.
Key Points Explained:
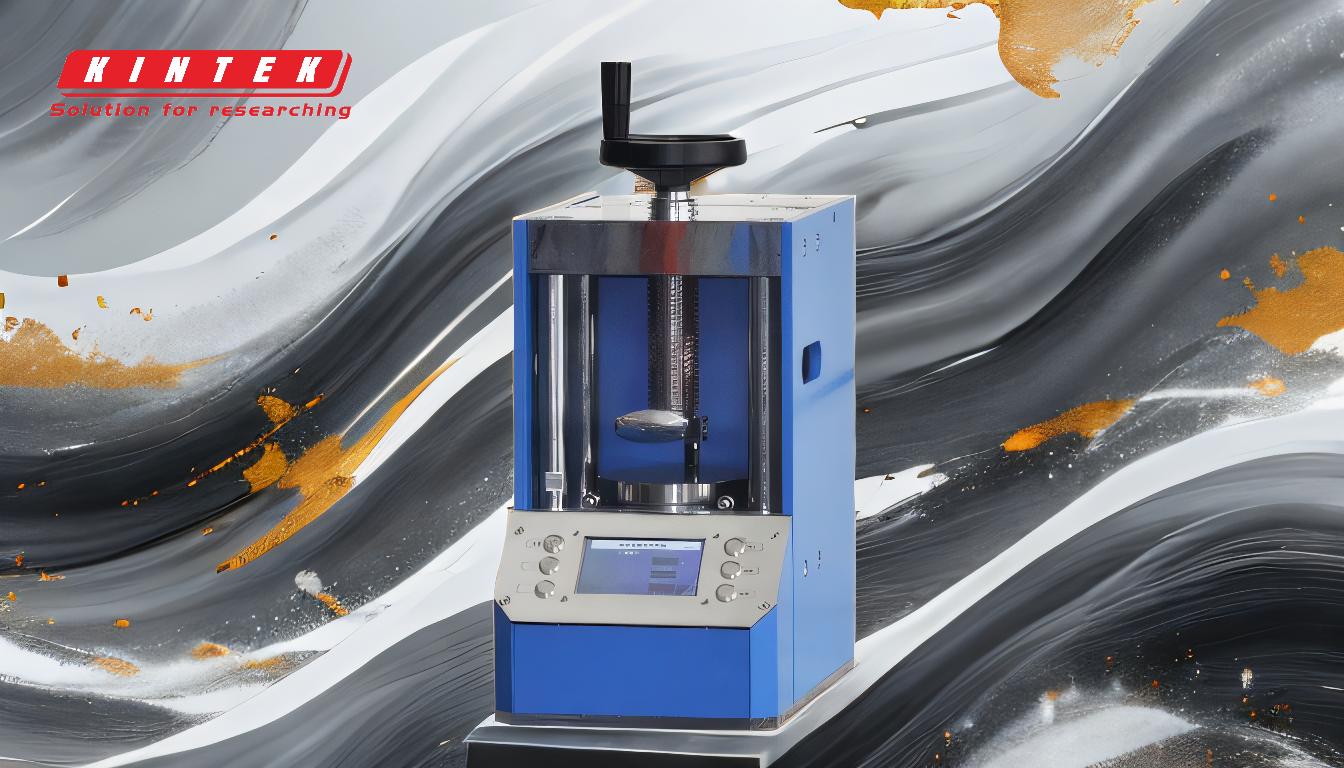
-
Principle of Agglomeration:
- Pelletizing machines operate on the principle of agglomeration, which involves the clustering of fine particles into larger, cohesive units. This is achieved through various mechanisms such as compression, rolling, or binding agents.
- The process is particularly useful for materials that are difficult to handle in their powdered form, such as minerals, chemicals, and food products.
-
Reduction of Dust Generation:
- One of the primary benefits of pelletizing is the significant reduction in dust generation. Fine particles are prone to becoming airborne, leading to material loss and potential health hazards.
- By forming larger pellets, the surface area of the material is reduced, thereby minimizing the amount of dust that can escape into the environment.
-
Improved Material Efficiency:
- Pelletizing reduces material loss by ensuring that more of the raw material is utilized effectively. This is particularly important in industries where raw materials are expensive or scarce.
- The process also allows for better control over the size and shape of the final product, which can be tailored to meet specific industrial requirements.
-
Enhanced Handling and Storage:
- Pellets are easier to handle, store, and transport compared to fine powders. They are less likely to spill or become airborne, making them safer and more convenient to work with.
- The uniform size and shape of pellets also facilitate automated handling systems, further improving operational efficiency.
-
Versatility in Applications:
- Pelletizing machines are used across a wide range of industries, including agriculture (for animal feed), pharmaceuticals (for tablet production), and metallurgy (for ore processing).
- The ability to customize the size, shape, and composition of pellets makes pelletizing machines highly versatile and adaptable to different industrial needs.
-
Environmental Benefits:
- By reducing dust and material loss, pelletizing contributes to a cleaner and safer working environment. This is particularly important in industries where dust can pose significant health risks.
- The process also supports sustainable practices by ensuring that more of the raw material is used efficiently, reducing waste and conserving resources.
In summary, pelletizing machines play a crucial role in various industries by transforming fine particles into larger, more manageable forms. The process not only improves material efficiency and handling but also offers significant environmental and safety benefits. Understanding the working principle of pelletizing machines is essential for optimizing their use and achieving the desired outcomes in different industrial applications.
Summary Table:
Aspect | Details |
---|---|
Principle of Agglomeration | Clustering fine particles into larger units via compression, rolling, or binding agents. |
Dust Reduction | Minimizes dust generation by reducing the surface area of fine particles. |
Material Efficiency | Reduces material loss and improves utilization of raw materials. |
Handling & Storage | Pellets are easier to handle, store, and transport compared to fine powders. |
Versatility | Used in agriculture, pharmaceuticals, metallurgy, and more. |
Environmental Benefits | Supports cleaner workplaces and sustainable practices. |
Discover how pelletizing machines can optimize your processes—contact us today for expert advice!