Thermal evaporation deposition is a widely used thin-film deposition technique in which a material is heated to its evaporation point in a vacuum environment, causing it to vaporize and condense onto a substrate, forming a thin, uniform layer. This method is highly versatile and is employed across industries such as optics, electronics, packaging, and aerospace for applications like anti-reflective coatings, OLEDs, solar cells, and decorative films. It offers advantages such as high deposition rates, material efficiency, and the ability to deposit pure metals or complex multi-component films. Advanced variations, such as reactive deposition and precursor gas methods, further enhance its capabilities for creating high-quality oxide or nitride coatings.
Key Points Explained:
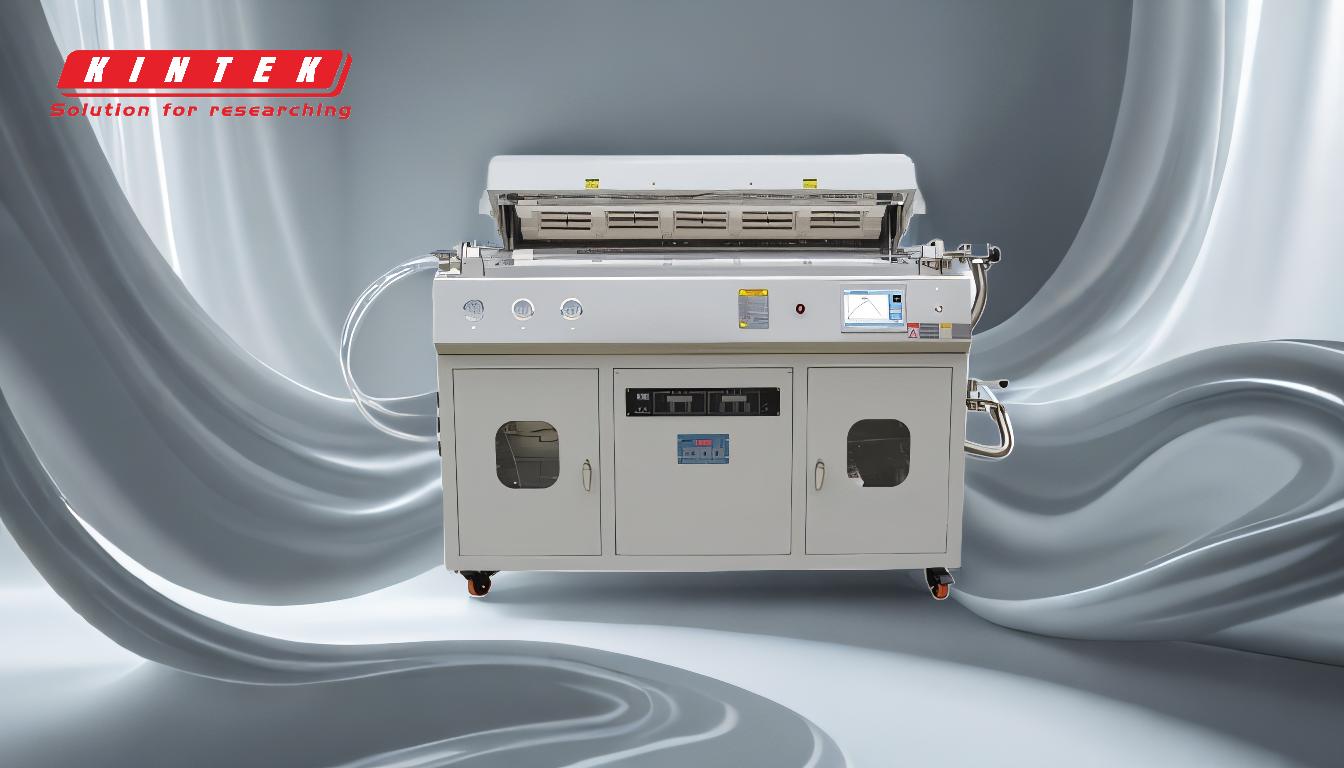
-
Principle of Thermal Evaporation Deposition:
- Thermal evaporation involves heating a material in a vacuum until it vaporizes. The vaporized material then travels through the vacuum chamber and condenses onto a substrate, forming a thin film.
- This process is ideal for depositing pure metals (e.g., silver, aluminum) and can be adapted for co-deposition of multiple materials by controlling the temperature of individual crucibles.
-
Applications Across Industries:
- Optics: Used for anti-reflective coatings, UV protection layers, and lens coatings.
- Electronics: Essential for ultra-thin metal plating in OLEDs, solar cells, and thin-film transistors.
- Packaging: Deposits aluminum films on plastic packaging for food preservation, insulation, and decorative purposes.
- Aerospace and Safety: Applied in NASA spacesuits, firefighter uniforms, emergency blankets, and anti-static or soundproof enclosures in aircraft.
-
Advantages of Thermal Evaporation:
- High Deposition Rate: Enables rapid formation of thin films, making it efficient for large-scale production.
- Material Utilization Efficiency: Minimizes waste by ensuring most of the vaporized material adheres to the substrate.
- Versatility: Suitable for a wide range of materials, including metals, alloys, and complex multi-component systems.
-
Advanced Techniques and Variations:
- Reactive Deposition: Combines metal source materials with high-purity gases (e.g., oxygen or nitrogen) to create oxide or nitride coatings, offering enhanced properties over direct deposition of base compounds.
- Precursor Gas Method: Involves using a metal-containing precursor gas that is activated and cyclically deposited with a reducing gas to form high-quality films. This method is particularly useful for creating precise, uniform coatings.
-
Comparison with Other Deposition Methods:
- Thermal evaporation is often compared to other physical vapor deposition (PVD) techniques, such as sputtering. While sputtering can handle a wider range of materials, thermal evaporation excels in applications requiring high-purity metal films and high deposition rates.
-
Challenges and Considerations:
- Material Limitations: Not all materials can be evaporated without decomposition, limiting its use for certain compounds.
- Uniformity and Adhesion: Achieving uniform film thickness and strong adhesion requires precise control of evaporation rates, substrate temperature, and vacuum conditions.
- Equipment Complexity: Advanced setups, such as E-Beam evaporation systems, are required for high-precision applications, increasing costs.
-
Future Trends and Innovations:
- The integration of thermal evaporation with other deposition methods, such as chemical vapor deposition (CVD), is expanding its capabilities for creating hybrid films with unique properties.
- Advances in automation and process control are improving the consistency and scalability of thermal evaporation for industrial applications.
Thermal evaporation deposition remains a cornerstone of thin-film technology due to its simplicity, efficiency, and adaptability. Its continued evolution, driven by advancements in materials science and process engineering, ensures its relevance in emerging applications across diverse industries.
Summary Table:
Aspect | Details |
---|---|
Principle | Heating materials in a vacuum to vaporize and condense into thin films. |
Applications | Optics, electronics, packaging, aerospace (e.g., OLEDs, solar cells). |
Advantages | High deposition rates, material efficiency, versatility. |
Advanced Techniques | Reactive deposition, precursor gas methods for oxide/nitride coatings. |
Challenges | Material limitations, uniformity, equipment complexity. |
Future Trends | Integration with CVD, automation for improved scalability. |
Discover how thermal evaporation deposition can transform your projects—contact our experts today!