Thermal evaporation of organic materials is a process used to deposit thin films of materials that remain stable in a vapor state. It involves heating a target material in a high vacuum environment until it evaporates, forming a vapor that then condenses onto a substrate to create a thin film. This technique is widely used in applications such as OLEDs, solar cells, thin film transistors, and even in specialized coatings for spacesuits and food packaging. The process relies on resistive heating or electron beam heating to achieve the necessary evaporation temperatures. Thermal evaporation is valued for its simplicity, ability to produce high-purity films, and strong adhesion to substrates.
Key Points Explained:
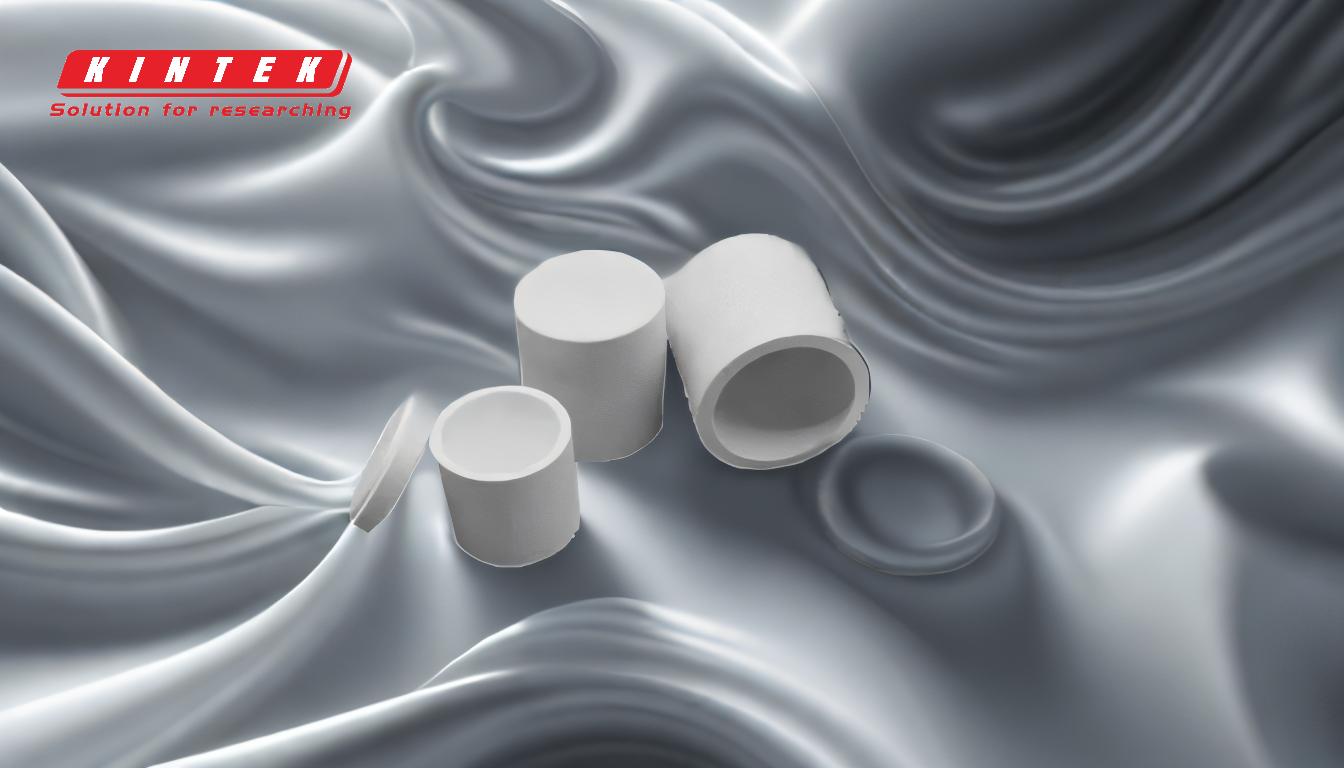
-
Definition and Basic Principle:
- Thermal evaporation is a physical vapor deposition (PVD) technique where a material is heated to its evaporation point in a vacuum environment.
- The material evaporates, forming a vapor that travels through the vacuum and condenses onto a substrate, creating a thin film.
-
Heating Mechanisms:
- Resistive Heating: A refractory metal element (such as a boat or coil) is heated by passing an electric current through it. The heat generated by electrical resistance melts and evaporates the target material.
- Electron Beam Heating: A focused beam of high-energy electrons directly heats the material, causing it to evaporate. This method is often used for materials with very high melting points.
-
Vacuum Environment:
- The process is carried out in a high vacuum to ensure that the evaporated material travels unimpeded to the substrate.
- The vacuum environment minimizes contamination and allows for the deposition of high-purity films.
-
Applications:
- Electronics: Used to deposit metals like silver and aluminum for OLEDs, solar cells, and thin film transistors.
- Packaging: Thin films of metals like aluminum are deposited on polymers for food packaging, providing barriers to moisture and gases.
- Specialized Coatings: Used in applications such as NASA spacesuits, firefighter uniforms, emergency blankets, and anti-static or soundproof enclosures in aircraft.
-
Process Details:
- The target material is placed in an evaporation source (such as a boat, coil, or basket) and heated until it evaporates.
- The vaporized molecules travel through the vacuum and condense on the substrate, forming a thin film.
- The process can be controlled to deposit single metals or co-deposit multiple components by carefully managing the temperature of individual crucibles.
-
Advantages:
- Simplicity: The process is relatively straightforward and easy to control.
- High Purity: The vacuum environment ensures that the deposited films are of high purity.
- Strong Adhesion: The films adhere well to the substrate, making them suitable for a wide range of applications.
-
Limitations:
- Material Limitations: Not all materials can be evaporated using this method, especially those with very high melting points or those that decompose before evaporating.
- Uniformity: Achieving uniform film thickness can be challenging, especially over large areas or complex geometries.
-
Historical Context:
- Thermal evaporation is one of the oldest vacuum coating technologies, with a long history of use in various industries.
- Despite the development of more advanced PVD techniques, thermal evaporation remains widely used due to its simplicity and effectiveness.
By understanding these key points, one can appreciate the versatility and importance of thermal evaporation in modern technology and industry. The process's ability to produce high-quality thin films makes it indispensable in fields ranging from electronics to specialized coatings.
Summary Table:
Aspect | Details |
---|---|
Definition | A PVD technique where materials are heated to evaporation in a vacuum. |
Heating Mechanisms | Resistive heating or electron beam heating. |
Vacuum Environment | Ensures high-purity films and minimal contamination. |
Applications | OLEDs, solar cells, thin film transistors, food packaging, and coatings. |
Advantages | Simplicity, high purity, and strong adhesion to substrates. |
Limitations | Material limitations and challenges in achieving uniform film thickness. |
Historical Context | One of the oldest vacuum coating technologies, still widely used today. |
Discover how thermal evaporation can enhance your project—contact our experts today!