Thermal evaporation is a widely used Physical Vapor Deposition (PVD) technique for creating thin films on substrates. It operates in a high-vacuum environment, where a source material is heated until it evaporates, forming a vapor stream that deposits onto a substrate. This method is particularly effective for depositing single metals like silver or aluminum, as well as more complex materials through co-deposition. The process involves key components such as a vacuum chamber, a vacuum pump, and an energy source (resistive or electron-beam heating). Thermal evaporation is essential in manufacturing electronic and optical devices, including solar cells, OLED displays, and MEMS.
Key Points Explained:
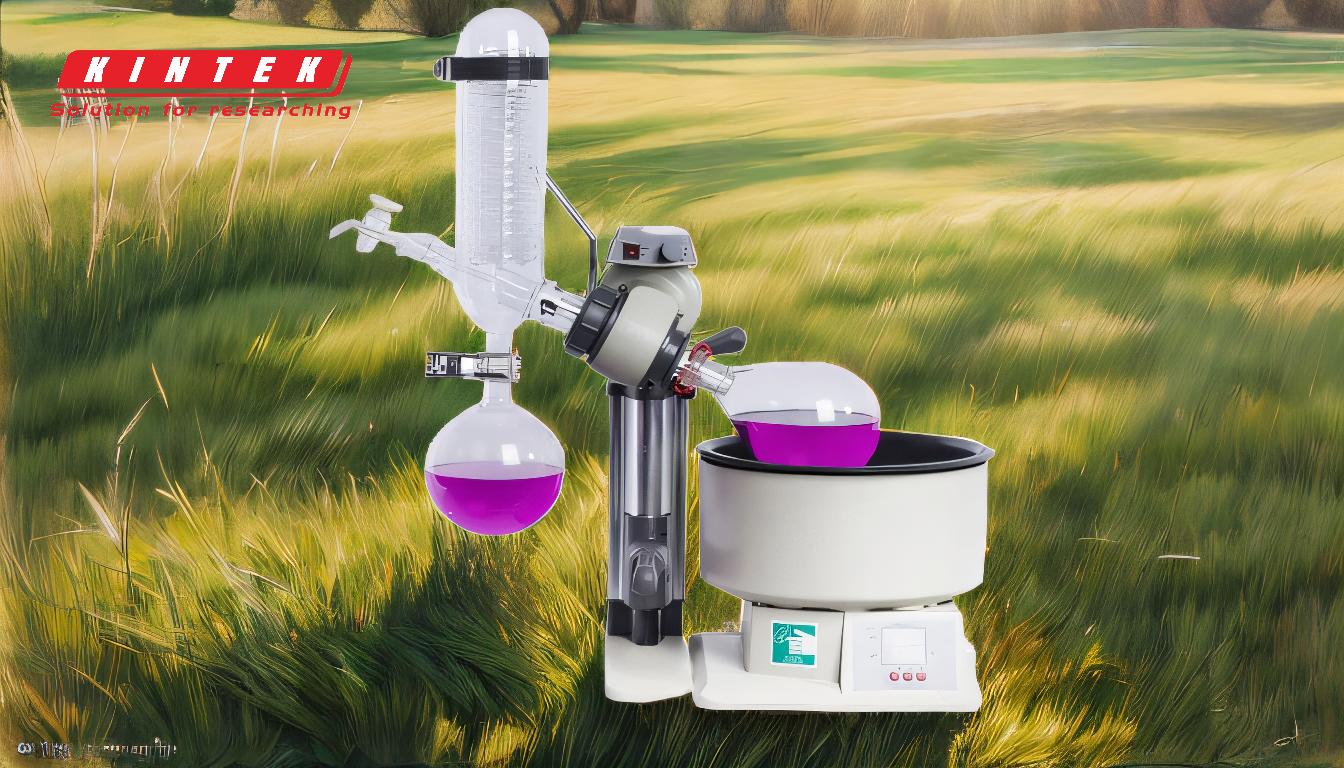
-
What is Thermal Evaporation?
- Thermal evaporation is a Physical Vapor Deposition (PVD) method used to deposit thin films of materials onto substrates. It involves heating a source material in a high-vacuum environment until it evaporates, forming a vapor stream that condenses onto the substrate.
-
Key Components of a Thermal Evaporation System:
- Vacuum Chamber: Houses the substrate and source material, ensuring a controlled environment for deposition.
- Vacuum Pump: Maintains the high-vacuum environment (10^(-6) to 10^(-5) mbar) necessary for the process.
- Energy Source: Provides heat to evaporate the source material. This can be resistive heating (using a refractory metal element) or electron-beam heating (using a focused beam of high-energy electrons).
- Crucible: Holds the target material and connects to the energy source.
- Substrate Fixtures: Hold the substrate in place, typically inverted at the top of the chamber.
-
How Thermal Evaporation Works:
- The source material is heated in a crucible, causing it to evaporate and form a vapor stream.
- The vapor stream travels through the vacuum chamber and deposits onto the substrate.
- The vacuum pump ensures a free path for the vapor particles, preventing contamination and enabling precise film formation.
-
Applications of Thermal Evaporation:
- Electronic Devices: Used for depositing electrical contacts, such as silver or aluminum layers.
- Optical Devices: Essential for creating thin films in OLED displays and solar cells.
- MEMS (Microelectromechanical Systems): Used for depositing thin films in micro-scale devices.
- Co-Deposition: Allows for the deposition of multiple materials by controlling the temperature of individual crucibles.
-
Advantages of Thermal Evaporation:
- Simplicity: One of the easiest PVD methods, making it accessible for various applications.
- High Purity: The high-vacuum environment ensures minimal contamination, resulting in high-quality thin films.
- Versatility: Suitable for depositing a wide range of materials, including metals, alloys, and compounds.
-
Comparison to Other PVD Methods:
- Resistive Thermal Evaporation: Uses resistive heating to evaporate the source material. It is simple and cost-effective but limited to materials with lower melting points.
- Electron-Beam Evaporation: Uses a focused beam of high-energy electrons to heat the source material. It is more versatile and can handle materials with higher melting points.
-
Process Parameters and Control:
- Vacuum Pressure: Typically maintained between 10^(-6) and 10^(-5) mbar to ensure a clean deposition environment.
- Temperature Control: Precise control of the crucible temperature is crucial for achieving the desired film properties.
- Deposition Rate: Controlled by adjusting the energy input and the distance between the source material and the substrate.
-
Challenges and Limitations:
- Material Limitations: Some materials may decompose or react at high temperatures, making them unsuitable for thermal evaporation.
- Uniformity: Achieving uniform film thickness can be challenging, especially for large substrates.
- Energy Efficiency: The process can be energy-intensive, particularly for electron-beam evaporation.
In summary, thermal evaporation is a versatile and widely used technique for depositing thin films in various industries. Its simplicity, high purity, and ability to handle a wide range of materials make it a preferred choice for applications in electronics, optics, and MEMS. By understanding the key components, process parameters, and applications, users can effectively leverage thermal evaporation systems for their specific needs.
Summary Table:
Aspect | Details |
---|---|
Definition | A Physical Vapor Deposition (PVD) technique for depositing thin films. |
Key Components | Vacuum chamber, vacuum pump, energy source, crucible, substrate fixtures. |
How It Works | Source material is heated, evaporates, and deposits onto a substrate. |
Applications | Solar cells, OLED displays, MEMS, electronic contacts. |
Advantages | Simplicity, high purity, versatility for various materials. |
Limitations | Material constraints, uniformity challenges, energy-intensive processes. |
Discover how a thermal evaporation system can enhance your manufacturing process—contact us today!