Thermal evaporation is a physical vapor deposition (PVD) technique used to deposit thin films on substrates. It involves heating a solid material in a high vacuum chamber until it evaporates, creating a vapor stream that travels through the chamber and adheres to the substrate as a coating or thin film. This method is widely used in applications such as creating OLEDs, thin-film transistors, and other electronic devices. The process relies on thermal energy, typically from an electric resistance heater or an electron beam, to vaporize the target material. The vacuum environment ensures that the vapor stream travels without reacting or scattering, allowing for precise and uniform deposition.
Key Points Explained:
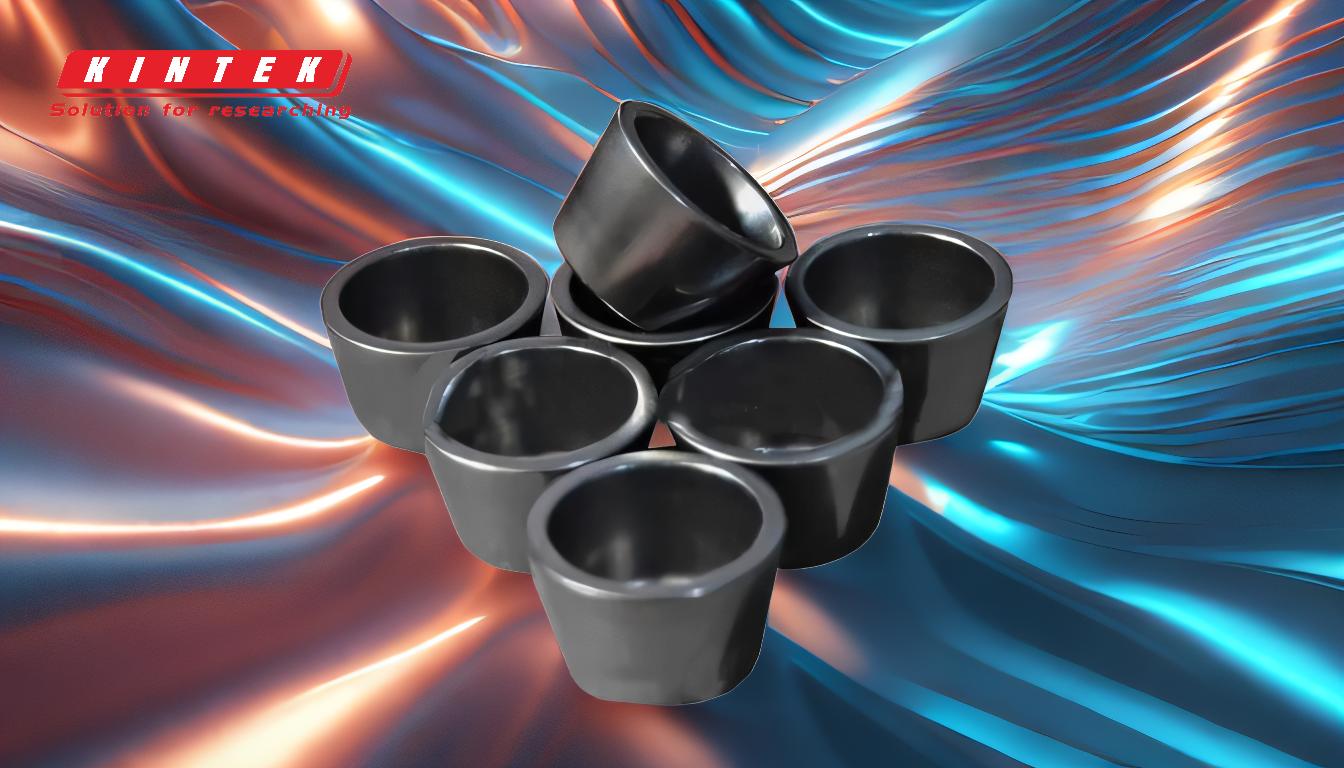
-
Principle of Thermal Evaporation:
- Thermal evaporation is based on the principle of heating a solid material until it reaches its vaporization point, producing a vapor pressure.
- In a high vacuum chamber, even a low vapor pressure is sufficient to create a vapor cloud.
- The vaporized material forms a stream that travels through the chamber and deposits onto the substrate, forming a thin film.
-
Components of the Thermal Evaporation System:
- Vacuum Chamber: A high vacuum environment is essential to prevent the vaporized material from reacting with air molecules and to ensure a clean deposition process.
- Heating Source: The material is heated using either an electric resistance heater (such as a tungsten filament or boat) or an electron beam evaporator.
- Substrate: The surface onto which the vaporized material is deposited. The substrate is typically placed opposite the evaporation source within the chamber.
-
Heating Methods:
- Resistive Heating: A common method where an electric current is passed through a resistive element (like a tungsten boat or filament) to heat the material to its melting and evaporation point.
- Electron Beam Evaporation: An alternative method where a focused electron beam is used to heat and vaporize the target material. This method is particularly useful for materials with high melting points.
-
Process Steps:
- Material Loading: The target material is placed in the evaporation source (boat or crucible) within the vacuum chamber.
- Vacuum Creation: The chamber is evacuated to create a high vacuum environment, typically in the range of 10^-6 to 10^-7 Torr.
- Heating and Evaporation: The material is heated until it evaporates, forming a vapor cloud.
- Vapor Transport: The vaporized material travels through the vacuum chamber in a straight-line path due to the absence of air molecules.
- Deposition: The vapor condenses on the substrate, forming a thin film.
-
Advantages of Thermal Evaporation:
- Simplicity: The process is relatively straightforward and easy to control.
- High Purity: The vacuum environment minimizes contamination, resulting in high-purity films.
- Versatility: Suitable for a wide range of materials, including metals, semiconductors, and insulators.
- Uniformity: Capable of producing uniform thin films over large areas.
-
Applications:
- OLEDs (Organic Light-Emitting Diodes): Thermal evaporation is widely used to deposit organic layers in OLED displays.
- Thin-Film Transistors: The technique is used to create thin-film transistors for electronic devices.
- Optical Coatings: Used in the production of anti-reflective coatings, mirrors, and other optical components.
- Decorative Coatings: Applied in the deposition of metallic coatings for decorative purposes.
-
Limitations:
- Material Constraints: Some materials may decompose or react before reaching their evaporation temperature.
- High Energy Consumption: The process requires significant energy to maintain the high vacuum and heating conditions.
- Limited Control Over Film Properties: Compared to other deposition techniques, thermal evaporation offers less control over film microstructure and stress.
-
Comparison with Other Deposition Techniques:
- Sputtering: Unlike thermal evaporation, sputtering involves bombarding a target material with ions to eject atoms, which then deposit on the substrate. Sputtering can achieve better adhesion and is suitable for a wider range of materials.
- Chemical Vapor Deposition (CVD): CVD involves chemical reactions to form a thin film on the substrate. It offers better control over film composition and properties but is more complex and expensive.
In summary, thermal evaporation is a versatile and widely used technique for depositing thin films in various applications. Its simplicity, ability to produce high-purity films, and compatibility with a range of materials make it a valuable tool in the fabrication of electronic and optical devices. However, it is essential to consider its limitations and compare it with other deposition methods to determine the best approach for specific applications.
Summary Table:
Aspect | Details |
---|---|
Principle | Heating a solid material to vaporize it, forming a thin film on a substrate. |
Components | Vacuum chamber, heating source (resistive or electron beam), substrate. |
Heating Methods | Resistive heating or electron beam evaporation. |
Process Steps | Material loading, vacuum creation, heating, vapor transport, deposition. |
Advantages | Simplicity, high purity, versatility, uniformity. |
Applications | OLEDs, thin-film transistors, optical coatings, decorative coatings. |
Limitations | Material constraints, high energy consumption, limited control over film. |
Comparison | Sputtering: better adhesion; CVD: better control but more complex. |
Ready to explore thermal evaporation for your project? Contact our experts today for tailored solutions!