Thermal evaporation is a widely used technique in various industries for depositing thin films of materials onto substrates. It is particularly valued for its ability to produce highly directional and precise coatings, making it essential in micro and nano-fabrication, electronics, optics, packaging, and even protective clothing. The process involves heating a material in a vacuum until it vaporizes, allowing the vapor to travel in a straight line and condense on a substrate, forming a thin film. This method is used for creating electrical contacts, decorative coatings, protective layers, and functional components in devices like OLEDs, solar cells, and thin-film transistors. Additionally, it finds applications in industries such as aerospace, automotive, and consumer goods, where precise material deposition is critical.
Key Points Explained:
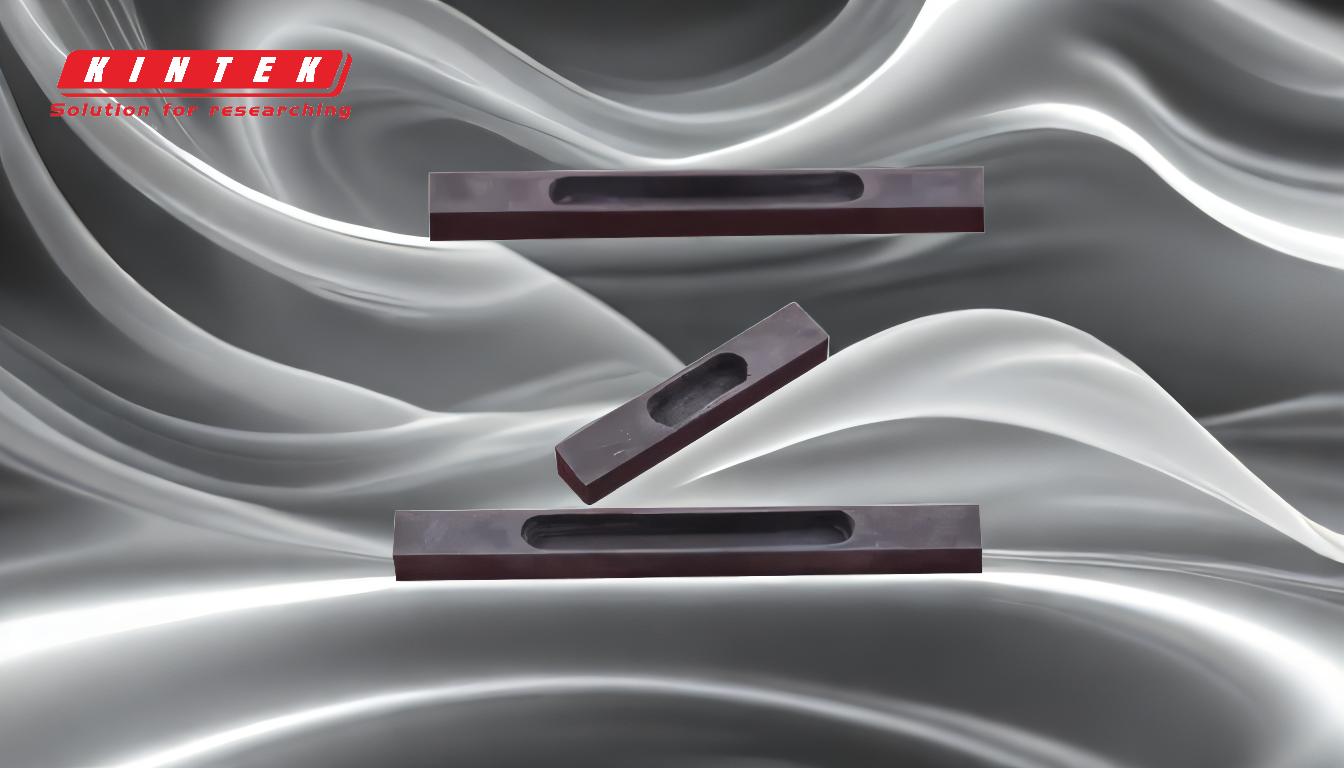
-
Micro and Nano-Fabrication:
- Thermal evaporation is crucial in micro and nano-fabrication systems, especially for processes like lift-off.
- The technique ensures highly directional deposition, where vaporized molecules travel in a straight line from the source to the substrate.
- This precision is vital for creating thin films with exact thickness and uniformity, which are essential for advanced electronic and optical devices.
-
Electronics and Optoelectronics:
- Thermal evaporation is extensively used in the fabrication of electronic devices such as OLEDs (Organic Light-Emitting Diodes), solar cells, and thin-film transistors.
- It is employed to create metal bonding layers and ultra-thin metal plating, which are critical for the performance and durability of these devices.
- The method is also used in optics for applications like lens coatings, anti-reflective layers, and UV protection, enhancing the functionality and longevity of optical components.
-
Consumer Packaging and Decorative Applications:
- In the consumer packaging industry, thermal evaporation is used to deposit thin films of metals like aluminum onto polymers.
- These metal films are used for food packaging, providing barrier properties that protect against moisture, oxygen, and contaminants.
- The technique is also used for decorative purposes, such as cosmetic closures and sporting goods, where aesthetic thin-film coatings are applied to enhance the visual appeal of products.
-
Protective and Functional Coatings:
- Thermal evaporation is employed to create protective coatings for various applications, including NASA spacesuits, firefighter uniforms, and emergency blankets.
- These coatings provide thermal insulation, soundproofing, and anti-static properties, making them essential for safety and performance in extreme environments.
- The method is also used in the automotive, medical, and aerospace industries for applications like EMI/RFI shielding and light reflectors, which are critical for the functionality and safety of these systems.
-
Complex Applications and Co-Deposition:
- Thermal evaporation can be used for more complex applications, such as the co-deposition of several components.
- By carefully controlling the temperature of individual crucibles, multiple materials can be deposited simultaneously, allowing for the creation of multi-layered or composite thin films.
- This capability is particularly useful in advanced manufacturing processes where precise material combinations are required for specific functional properties.
-
Versatility Across Industries:
- The versatility of thermal evaporation makes it applicable across a wide range of industries, from electronics and optics to packaging and protective clothing.
- Its ability to deposit a variety of materials, including metals, polymers, and composites, with high precision and uniformity, makes it a preferred choice for many fabrication processes.
- The technique’s adaptability to different substrates and its compatibility with other fabrication methods further enhance its utility in diverse applications.
In summary, thermal evaporation is a fundamental technique in modern fabrication processes, offering precision, versatility, and reliability. Its applications span across multiple industries, from creating advanced electronic components to enhancing the functionality and aesthetics of consumer products. The method’s ability to produce highly directional and uniform thin films makes it indispensable in both high-tech and everyday applications.
Summary Table:
Key Applications | Industries |
---|---|
Micro and Nano-Fabrication | Electronics, Optics |
Electronics and Optoelectronics | OLEDs, Solar Cells, Thin-Film Transistors |
Consumer Packaging | Food Packaging, Decorative Coatings |
Protective Coatings | Aerospace, Automotive, Medical, Protective Clothing |
Complex Applications | Multi-Layered Films, Co-Deposition |
Versatility | Across Industries: Electronics, Optics, Packaging, Aerospace, and More |
Ready to leverage thermal evaporation for your next project? Contact our experts today!