Thermally activated Chemical Vapor Deposition (CVD) is a process used to deposit thin films of materials onto a substrate through chemical reactions in the vapor phase. This process involves three main steps: evaporation of a volatile compound, thermal decomposition or chemical reaction of the vapor, and deposition of nonvolatile reaction products on the substrate. The thermal activation aspect refers to the use of heat to drive these chemical reactions, enabling the formation of high-quality films with precise control over thickness and composition. This method is widely used in industries such as semiconductors, optics, and coatings due to its ability to produce uniform and high-purity films.
Key Points Explained:
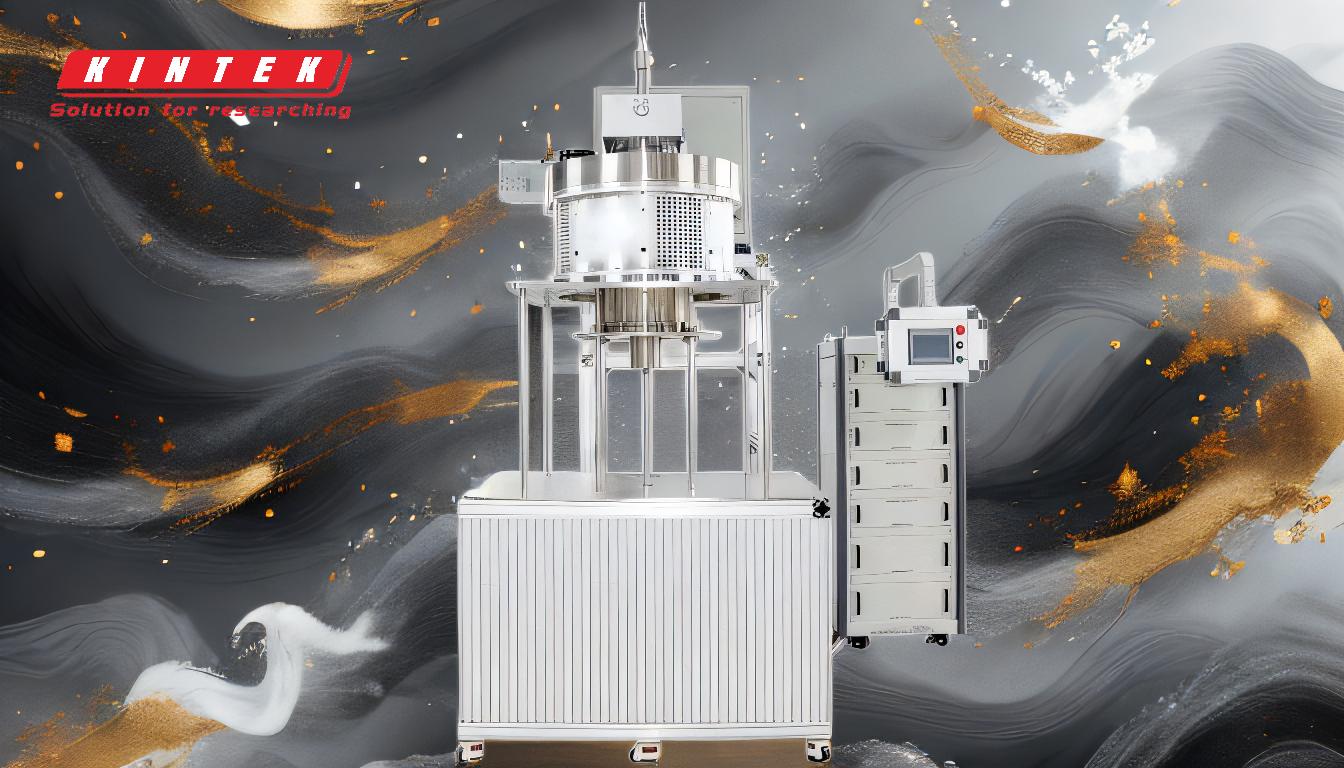
-
Definition of Thermally Activated CVD:
- Thermally activated CVD is a process where heat is used to initiate and sustain chemical reactions in the vapor phase, leading to the deposition of thin films on a substrate. This method is particularly useful for creating high-quality, uniform coatings with controlled properties.
-
Steps Involved in Thermally Activated CVD:
- Evaporation: A volatile compound of the substance to be deposited is evaporated. This step ensures that the material is in the vapor phase, ready for the next stages.
- Thermal Decomposition/Chemical Reaction: The vapor undergoes thermal decomposition or reacts with other gases, liquids, or vapors at the substrate. This step is crucial for breaking down the vapor into reactive species that can form the desired film.
- Deposition: The nonvolatile reaction products are deposited onto the substrate, forming a thin film. This step determines the final properties of the coating, such as thickness, uniformity, and adhesion.
-
Applications of Thermally Activated CVD:
- Semiconductors: Used to deposit thin films of silicon, silicon dioxide, and other materials essential for semiconductor devices.
- Optics: Applied in the production of anti-reflective coatings, mirrors, and other optical components.
- Coatings: Utilized for creating wear-resistant, corrosion-resistant, and decorative coatings on various substrates.
-
Advantages of Thermally Activated CVD:
- High Purity: The process can produce films with very high purity levels, essential for applications in electronics and optics.
- Uniformity: Thermally activated CVD allows for the deposition of uniform films over large areas, which is critical for industrial applications.
- Control over Film Properties: The process offers precise control over the thickness, composition, and microstructure of the deposited films.
-
Comparison with Other Deposition Methods:
- Physical Vapor Deposition (PVD): Unlike PVD, which relies on physical processes like sputtering or evaporation, CVD involves chemical reactions, allowing for better control over film composition and properties.
- Plasma-Enhanced CVD (PECVD): While PECVD uses plasma to activate the chemical reactions, thermally activated CVD relies solely on heat, making it simpler but potentially less effective for certain materials.
-
Role of Short Path Vacuum Distillation in CVD:
- Short path vacuum distillation is often used in conjunction with CVD processes to purify the precursors or to recover valuable by-products. The vacuum environment reduces the boiling points of the substances, allowing for the distillation of heat-sensitive materials without degradation. This is particularly important in CVD, where the purity of the precursors directly affects the quality of the deposited films.
-
Future Trends in Thermally Activated CVD:
- Low-Temperature CVD: Research is ongoing to develop CVD processes that can operate at lower temperatures, expanding the range of substrates and materials that can be used.
- Nanostructured Films: Advances in CVD technology are enabling the deposition of nanostructured films with unique properties, such as enhanced electrical conductivity or catalytic activity.
- Sustainability: Efforts are being made to make CVD processes more environmentally friendly by reducing the use of hazardous chemicals and improving energy efficiency.
In summary, thermally activated CVD is a versatile and powerful technique for depositing thin films with high precision and control. Its applications span a wide range of industries, and ongoing research continues to expand its capabilities and improve its efficiency. The integration of techniques like short path vacuum distillation further enhances the process by ensuring the purity of the precursors and by-products, ultimately leading to higher-quality films and more sustainable manufacturing practices.
Summary Table:
Aspect | Details |
---|---|
Definition | Heat-driven chemical reactions in vapor phase to deposit thin films. |
Key Steps | Evaporation, thermal decomposition/chemical reaction, deposition. |
Applications | Semiconductors, optics, coatings. |
Advantages | High purity, uniformity, precise control over film properties. |
Comparison with PVD | CVD uses chemical reactions; PVD relies on physical processes. |
Future Trends | Low-temperature CVD, nanostructured films, sustainability improvements. |
Learn more about how thermally activated CVD can benefit your industry—contact us today!