Thin film deposition by magnetron sputtering is a highly controlled and efficient physical vapor deposition (PVD) technique used to create thin, uniform coatings on substrates. It involves the use of a magnetic field to enhance the sputtering process, where atoms are ejected from a target material and deposited onto a substrate. This method is widely used in industries such as semiconductors, optics, and coatings due to its ability to produce high-quality, durable, and precise thin films with tailored properties. The process operates in a high-vacuum environment, utilizing ionized gas (typically argon) to bombard the target material, causing atoms to be ejected and deposited onto the substrate. The magnetic field confines electrons near the target, increasing plasma density and deposition rates while minimizing substrate damage.
Key Points Explained:
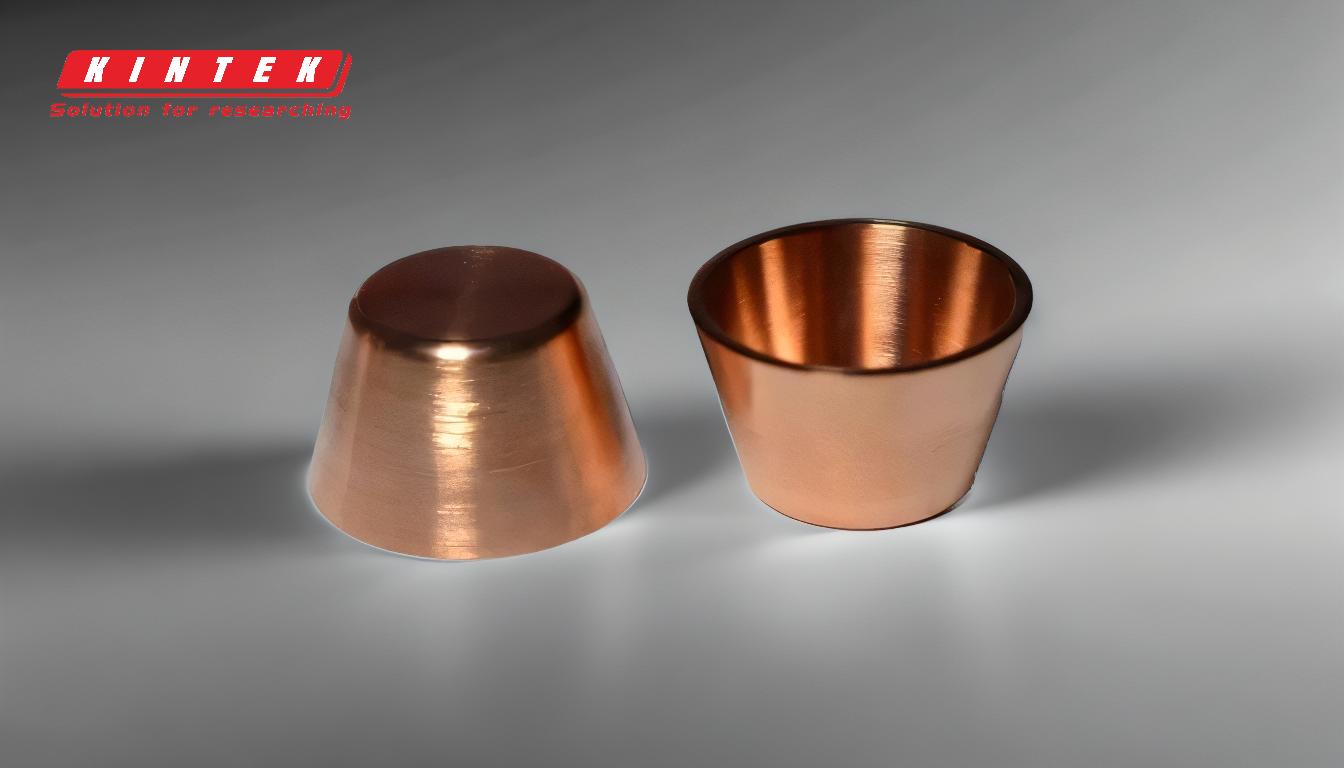
-
What is Thin Film Deposition?
- Thin film deposition is the process of applying a thin layer of material (ranging from nanometers to micrometers) onto a substrate to modify its surface properties.
- It is used to enhance characteristics such as conductivity, wear resistance, corrosion resistance, hardness, and optical or electrical properties.
- The process can be categorized into two main types: chemical deposition (involving chemical reactions) and physical deposition (involving mechanical or thermodynamic means).
-
Overview of Magnetron Sputtering:
- Magnetron sputtering is a physical vapor deposition (PVD) technique that uses a magnetic field to control the behavior of charged particles during the deposition process.
- It is performed in a high-vacuum chamber to create a low-pressure environment, ensuring minimal contamination and precise control over the deposition process.
- The process involves ionizing a gas (typically argon) to create a plasma, which bombards a target material, causing atoms to be ejected and deposited onto a substrate.
-
How Magnetron Sputtering Works:
- Vacuum Chamber Setup: The substrate and target material are placed inside a high-vacuum chamber.
- Gas Introduction: An inert gas (usually argon) is introduced into the chamber and ionized to form a plasma.
- Ion Bombardment: A high negative voltage is applied to the target (cathode), attracting positively charged argon ions from the plasma. These ions collide with the target, ejecting atoms from its surface.
- Magnetic Field Confinement: A strong magnetic field is applied near the target surface, confining electrons and increasing plasma density. This enhances the deposition rate and reduces substrate damage from ion bombardment.
- Film Formation: The ejected target atoms travel through the vacuum and deposit onto the substrate, forming a thin, uniform film.
-
Advantages of Magnetron Sputtering:
- High-Quality Films: Produces dense, uniform, and adherent thin films with excellent surface finish.
- Material Versatility: Can deposit a wide range of materials, including metals, oxides, and compounds.
- Controlled Deposition: Allows precise control over film thickness, composition, and properties.
- Low Substrate Damage: The magnetic field minimizes ion bombardment damage to the substrate.
- Scalability: Suitable for both small-scale research and large-scale industrial applications.
-
Applications of Magnetron Sputtering:
- Semiconductors: Used to deposit conductive and insulating layers in integrated circuits and microelectronics.
- Optics: Enhances optical properties of glass, such as anti-reflective and reflective coatings.
- Coatings: Improves wear resistance, corrosion resistance, and hardness of engineering components.
- Energy: Applied in solar cells, fuel cells, and battery technologies to enhance performance.
- Decorative Coatings: Used for aesthetic finishes on consumer products.
-
Comparison with Other Thin Film Deposition Techniques:
- Thermal Evaporation: Involves heating the target material until it evaporates and deposits onto the substrate. Less precise and versatile compared to magnetron sputtering.
- Chemical Vapor Deposition (CVD): Involves chemical reactions to form thin films. Suitable for high-temperature applications but less material-efficient than sputtering.
- Ion Beam Deposition: Uses an ion beam to sputter target material. Offers high precision but is slower and more complex than magnetron sputtering.
-
Key Considerations for Equipment and Consumable Purchasers:
- Target Material Selection: Choose high-purity targets compatible with the desired film properties.
- Vacuum System Quality: Ensure the vacuum chamber and pumps can achieve and maintain the required low-pressure environment.
- Magnetic Field Configuration: Optimize the magnetic field strength and geometry for efficient plasma confinement.
- Substrate Compatibility: Verify that the substrate material can withstand the deposition process without degradation.
- Cost and Throughput: Balance equipment cost, deposition rate, and film quality to meet production needs.
By understanding the principles and applications of magnetron sputtering, purchasers can make informed decisions about equipment and consumables to achieve optimal thin film deposition results.
Summary Table:
Key Aspect | Details |
---|---|
Process Type | Physical Vapor Deposition (PVD) |
Key Mechanism | Magnetic field enhances sputtering, ejecting target atoms onto substrates. |
Environment | High-vacuum chamber with ionized gas (argon). |
Advantages | High-quality, uniform films; material versatility; low substrate damage. |
Applications | Semiconductors, optics, coatings, energy, and decorative finishes. |
Comparison | More precise and versatile than thermal evaporation and CVD. |
Ready to optimize your thin film deposition process? Contact our experts today to learn more!