Thin film deposition via thermal evaporation is a widely used physical vapor deposition (PVD) technique in which a solid material is heated in a high vacuum chamber until it evaporates, forming a vapor stream. This vapor travels through the vacuum and condenses onto a substrate, forming a thin film. The process is simple, efficient, and particularly useful for applications such as OLEDs and thin-film transistors. It relies on creating a high vacuum environment to minimize atomic scattering and ensure the material adheres uniformly to the substrate. Thermal energy is typically supplied by resistive heating or electron beams, depending on the material's properties and the desired film characteristics.
Key Points Explained:
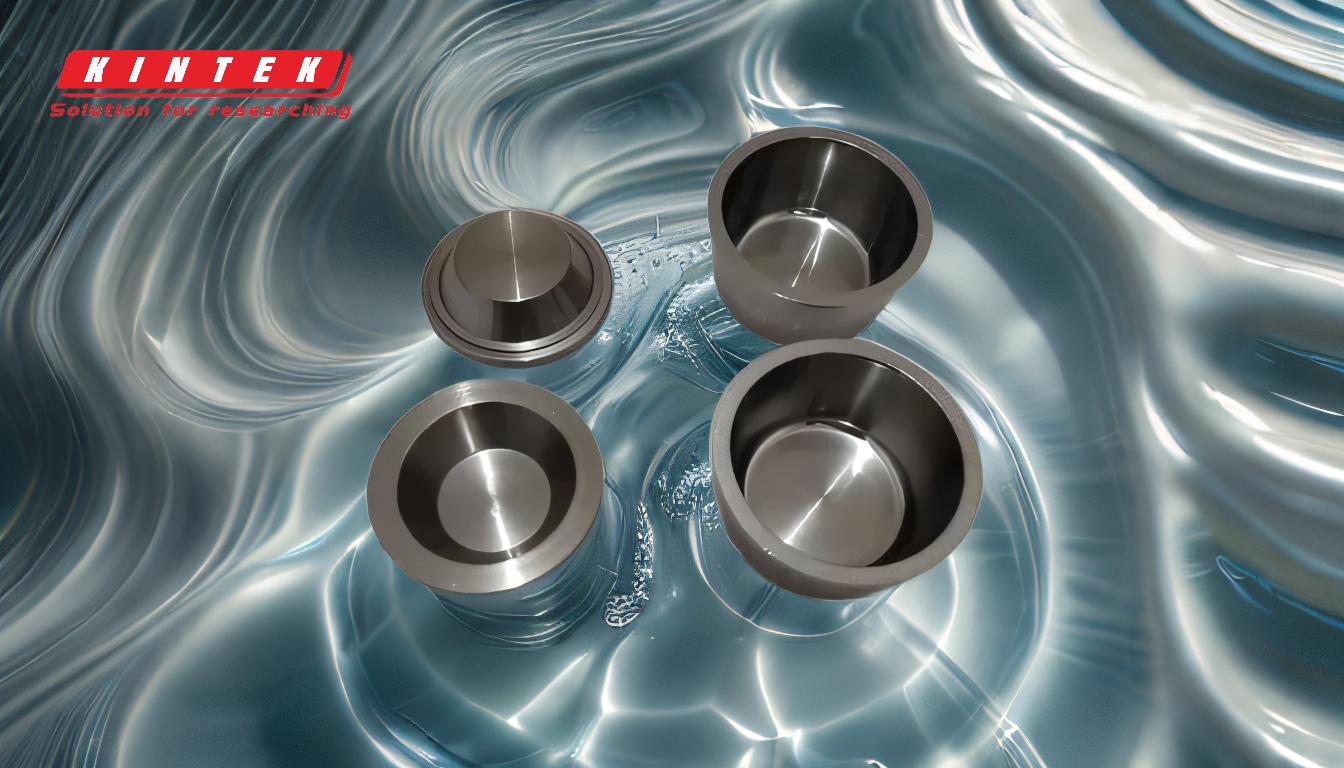
-
Definition and Purpose of Thermal Evaporation:
- Thermal evaporation is a physical vapor deposition (PVD) method used to deposit thin films on substrates.
- It involves heating a solid material in a high vacuum chamber until it evaporates, forming a vapor stream that condenses onto a substrate.
- This technique is widely used in industries such as electronics, optics, and coatings, particularly for creating OLEDs and thin-film transistors.
-
How Thermal Evaporation Works:
- Heating the Material: The target material is heated using a resistive heater (e.g., tungsten filament) or an electron beam. The heat causes the material to melt and eventually evaporate.
- Vacuum Environment: The process occurs in a high vacuum chamber to minimize interactions between vaporized atoms and other particles, ensuring a clean and uniform deposition.
- Vapor Stream Formation: The evaporated material forms a vapor cloud, which travels through the vacuum and deposits onto the substrate.
- Film Formation: The vapor condenses on the substrate, forming a thin, uniform film.
-
Key Components of the System:
- Vacuum Chamber: A high vacuum environment is essential to reduce atomic scattering and contamination, ensuring the vapor stream travels unimpeded to the substrate.
- Heating Source: Depending on the material, a resistive heater (e.g., tungsten filament) or an electron beam is used to vaporize the target material.
- Evaporation Boat or Crucible: A container that holds the material and withstands high temperatures during evaporation.
- Substrate Holder: Holds the substrate in place and ensures proper alignment for uniform deposition.
-
Advantages of Thermal Evaporation:
- Simplicity: The process is straightforward and easy to implement compared to other deposition techniques.
- High Purity: The high vacuum environment minimizes contamination, resulting in high-purity films.
- Material Versatility: It can deposit a wide range of materials, including metals, semiconductors, and dielectrics.
- Uniformity: The process allows for the deposition of uniform and thin films, which is critical for applications like OLEDs and thin-film transistors.
-
Limitations of Thermal Evaporation:
- Material Compatibility: Not all materials can be evaporated due to differences in melting points and vapor pressures.
- Stress in Films: The rapid cooling of vaporized material on the substrate can lead to internal stresses in the film.
- Limited Control: Compared to more advanced techniques like sputtering, thermal evaporation offers less control over film composition and structure.
-
Applications of Thermal Evaporation:
- OLEDs (Organic Light-Emitting Diodes): Thermal evaporation is commonly used to deposit organic layers in OLED displays.
- Thin-Film Transistors: It is used to create conductive and semiconductive layers in electronic devices.
- Optical Coatings: The technique is employed to deposit anti-reflective and reflective coatings on lenses and mirrors.
- Metallization: It is widely used to deposit metal layers in microelectronics and solar cells.
-
Comparison with Other Deposition Techniques:
- Sputtering: Sputtering uses energetic ions to eject atoms from a target, offering better control over film composition but requiring more complex equipment.
- Chemical Vapor Deposition (CVD): CVD involves chemical reactions to deposit films, enabling the creation of complex structures but requiring higher temperatures and more complex setups.
- Thermal Evaporation: Simpler and more cost-effective than sputtering and CVD, but with limitations in material compatibility and film control.
-
Process Optimization:
- Vacuum Quality: Maintaining a high vacuum is critical to ensure minimal contamination and uniform deposition.
- Temperature Control: Precise control of the heating source is necessary to achieve consistent evaporation rates.
- Substrate Preparation: Proper cleaning and alignment of the substrate are essential for achieving high-quality films.
In summary, thermal evaporation is a versatile and widely used technique for thin film deposition, offering simplicity, high purity, and material versatility. However, it has limitations in material compatibility and film control, making it suitable for specific applications like OLEDs and thin-film transistors. Understanding the process, components, and optimization strategies is crucial for achieving high-quality thin films.
Summary Table:
Aspect | Details |
---|---|
Definition | A PVD technique where a solid material is heated in a vacuum to form a thin film. |
Key Components | Vacuum chamber, heating source, evaporation boat/crucible, substrate holder. |
Advantages | Simplicity, high purity, material versatility, uniform deposition. |
Limitations | Material compatibility issues, film stress, limited control over film properties. |
Applications | OLEDs, thin-film transistors, optical coatings, metallization. |
Comparison | Simpler and cost-effective compared to sputtering and CVD. |
Optimization | High vacuum, precise temperature control, proper substrate preparation. |
Discover how thermal evaporation can enhance your thin film processes—contact our experts today!