Inert atmospheres are crucial in the pharmaceutical industry to maintain the stability, quality, and shelf life of sensitive products. These atmospheres prevent unwanted chemical reactions, such as oxidation, by replacing reactive gases like oxygen with inert gases. The most commonly used inert gases in pharmaceuticals include nitrogen, argon, and helium, with nitrogen being the most prevalent due to its cost-effectiveness and availability. These gases are used in various stages of pharmaceutical manufacturing, packaging, and storage to ensure product integrity.
Key Points Explained:
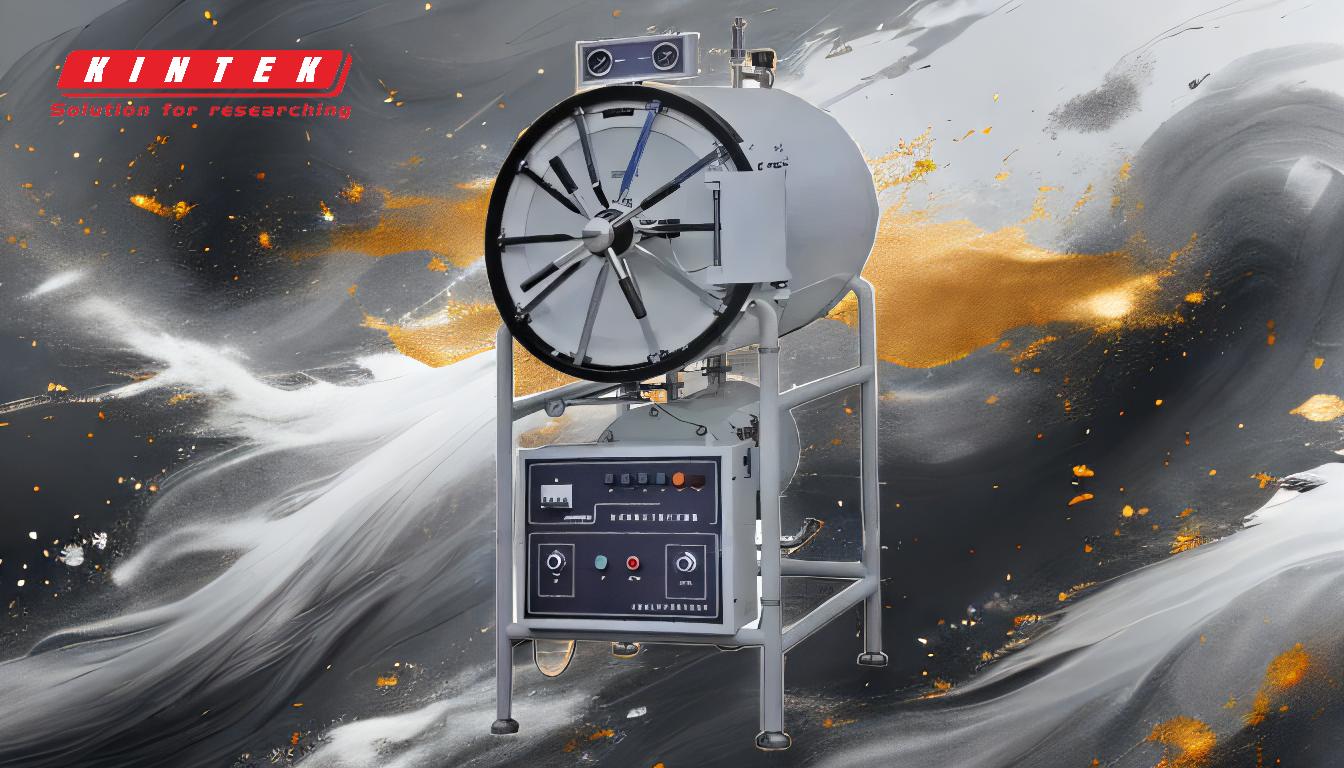
-
Purpose of Inert Atmospheres in Pharmaceuticals
- Inert atmospheres are used to create a chemically inactive environment that prevents degradation or contamination of pharmaceutical products.
- They are particularly important for oxygen-sensitive drugs, vaccines, and biologics, where exposure to oxygen can lead to oxidation, loss of potency, or spoilage.
- Inert atmospheres are also used during manufacturing processes to protect raw materials and intermediates from reacting with atmospheric gases.
-
Common Inert Gases Used
- Nitrogen: The most widely used inert gas in pharmaceuticals due to its availability, low cost, and effectiveness in displacing oxygen. It is often used in packaging to extend shelf life and maintain product quality.
- Argon: A heavier gas than nitrogen, argon is used in specific applications where its density provides better protection, such as in the storage of highly sensitive materials.
- Helium: While less commonly used due to its high cost, helium is employed in specialized applications where its low molecular weight and inert properties are advantageous.
-
Applications in Pharmaceutical Processes
- Packaging: Inert gases like nitrogen are flushed into the packaging of medications to displace oxygen and create a protective environment. This is especially important for injectable drugs, vaccines, and biologics.
- Storage: Inert atmospheres are maintained in storage facilities to protect bulk pharmaceutical ingredients and finished products from degradation.
- Manufacturing: During processes like lyophilization (freeze-drying) or tablet coating, inert gases are used to prevent oxidation and ensure product stability.
-
Benefits of Using Inert Atmospheres
- Extended Shelf Life: By preventing oxidation and other chemical reactions, inert atmospheres help extend the shelf life of pharmaceutical products.
- Enhanced Product Quality: Maintaining an inert environment ensures that the active pharmaceutical ingredients (APIs) remain stable and effective.
- Regulatory Compliance: Many pharmaceutical products require an inert atmosphere to meet stringent regulatory standards for safety and efficacy.
-
Considerations for Selecting Inert Gases
- Cost: Nitrogen is often preferred due to its affordability, while argon and helium are reserved for specialized applications.
- Gas Properties: The choice of gas depends on factors like density, solubility, and reactivity with the pharmaceutical product.
- Safety: While inert gases are generally safe, proper handling and monitoring are essential to prevent asphyxiation risks in enclosed spaces.
In summary, inert atmospheres play a vital role in the pharmaceutical industry by protecting sensitive products from degradation. Nitrogen is the most commonly used inert gas due to its cost-effectiveness and availability, while argon and helium are used in specialized applications. These gases are essential for ensuring product quality, extending shelf life, and meeting regulatory requirements.
Summary Table:
Inert Gas | Key Properties | Applications |
---|---|---|
Nitrogen | Cost-effective, widely available | Packaging, storage, manufacturing |
Argon | Heavy, better protection for sensitive materials | Specialized storage |
Helium | Low molecular weight, inert | Specialized applications |
Ensure your pharmaceutical products remain stable and effective—contact our experts today to learn more about inert atmospheres!