Plasma-enhanced chemical vapor deposition (PECVD) is a versatile technique used to deposit a wide range of materials, particularly thin films, on substrates. The process involves the use of plasma to activate chemical reactions in gaseous precursors, enabling the deposition of materials at relatively low temperatures compared to traditional CVD. PECVD is widely used in industries such as semiconductors, optics, and coatings due to its ability to deposit high-quality, uniform films. The materials deposited via PECVD include silicon-based compounds (e.g., silicon nitride, silicon oxide), carbon-based materials (e.g., diamond-like carbon), and other functional materials like amorphous silicon and polycrystalline silicon.
Key Points Explained:
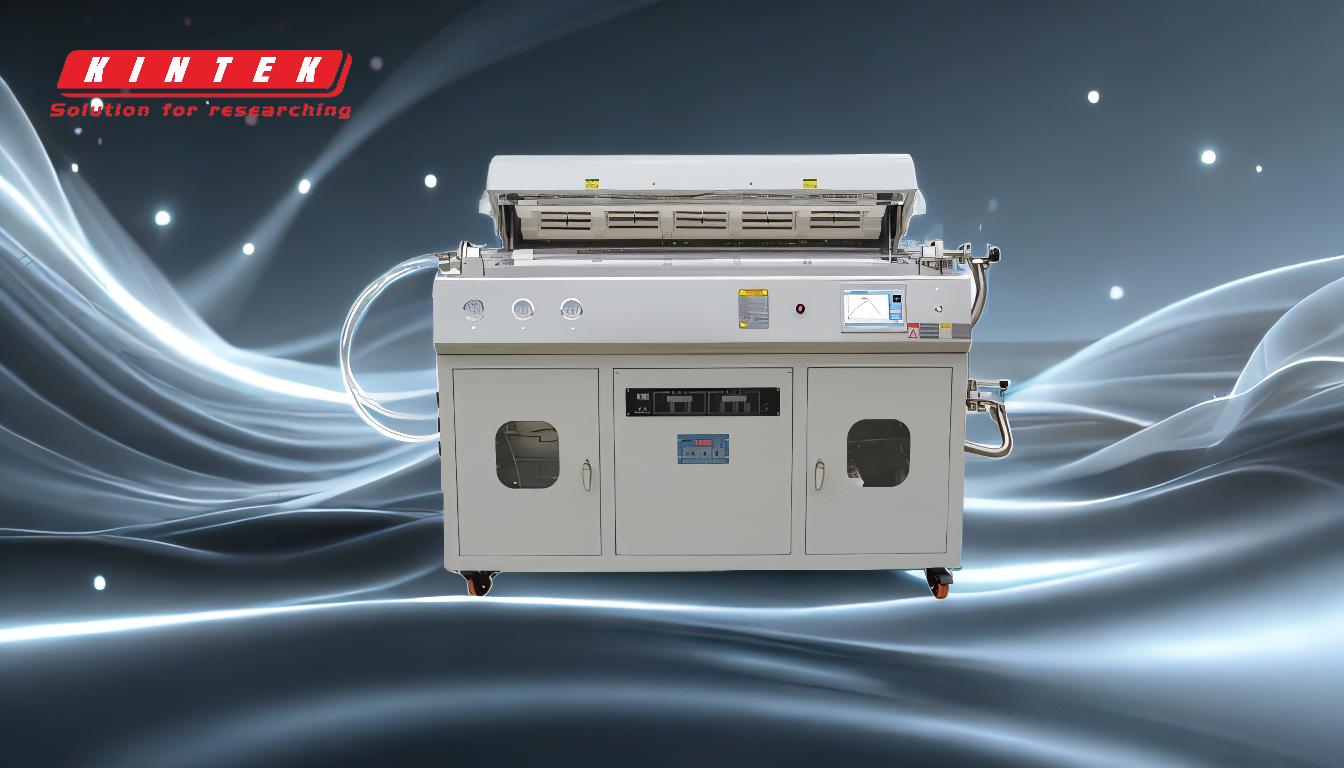
-
Silicon-Based Compounds:
- PECVD is commonly used to deposit silicon-based materials, which are critical in semiconductor and microelectronics industries. These include:
- Silicon Nitride (Si₃N₄): Used as a dielectric layer, passivation layer, and barrier material due to its excellent insulating properties and resistance to oxidation.
- Silicon Oxide (SiO₂): A key material for gate oxides, interlayer dielectrics, and protective coatings.
- Silicon OxyNitride (SiON): Combines the properties of silicon oxide and nitride, often used in anti-reflective coatings and optical applications.
- PECVD is commonly used to deposit silicon-based materials, which are critical in semiconductor and microelectronics industries. These include:
-
Carbon-Based Materials:
- PECVD can deposit carbon-based materials with unique properties:
- Diamond-Like Carbon (DLC): Known for its hardness, low friction, and chemical inertness, DLC is used in wear-resistant coatings and biomedical applications.
- Amorphous Carbon: Used in protective coatings and as a precursor for graphene synthesis.
- PECVD can deposit carbon-based materials with unique properties:
-
Amorphous and Polycrystalline Silicon:
- Amorphous Silicon (a-Si): Widely used in thin-film solar cells, flat-panel displays, and sensors due to its low-temperature deposition and tunable electronic properties.
- Polycrystalline Silicon (Poly-Si): Used in microelectronics for gate electrodes and interconnects due to its high conductivity and compatibility with CMOS processes.
-
Other Functional Materials:
- PECVD can deposit high-K dielectrics (e.g., hafnium oxide) for advanced semiconductor devices, as well as fluorocarbon co-monomers for hydrophobic coatings and anti-fouling applications.
-
Advantages of PECVD:
- Low-temperature deposition: Suitable for temperature-sensitive substrates.
- High deposition rates: Enables efficient production of thin films.
- Versatility: Can deposit a wide range of materials with tailored properties.
-
Applications:
- Semiconductor Industry: Deposition of dielectric layers, passivation layers, and interconnects.
- Optics: Anti-reflective coatings, optical filters, and waveguides.
- Coatings: Wear-resistant, hydrophobic, and protective coatings.
PECVD's ability to deposit a variety of materials with precise control over composition and properties makes it a cornerstone technology in modern manufacturing and research.
Summary Table:
Material Type | Examples | Key Applications |
---|---|---|
Silicon-Based Compounds | Silicon Nitride (Si₃N₄), Silicon Oxide (SiO₂), Silicon OxyNitride (SiON) | Dielectric layers, passivation layers, gate oxides, anti-reflective coatings |
Carbon-Based Materials | Diamond-Like Carbon (DLC), Amorphous Carbon | Wear-resistant coatings, biomedical applications, graphene synthesis |
Amorphous & Polycrystalline Silicon | Amorphous Silicon (a-Si), Polycrystalline Silicon (Poly-Si) | Thin-film solar cells, flat-panel displays, microelectronics |
Other Functional Materials | Hafnium Oxide, Fluorocarbon Co-monomers | High-K dielectrics, hydrophobic coatings, anti-fouling applications |
Interested in leveraging PECVD for your next project? Contact our experts today to learn more!