PVD (Physical Vapor Deposition) coatings are known for their thin, durable, and high-performance properties. The size or thickness of PVD coatings typically ranges between 0.25 microns and 5 microns, depending on the application and material. This thinness ensures that the coatings do not alter the specifications of engineered parts while providing excellent hardness, corrosion resistance, and durability. PVD coatings are widely used in industries such as jewelry, electronics, and manufacturing due to their superior performance compared to traditional coating methods like electroplating. Factors such as substrate material, coating thickness, and application conditions influence the longevity and effectiveness of PVD coatings.
Key Points Explained:
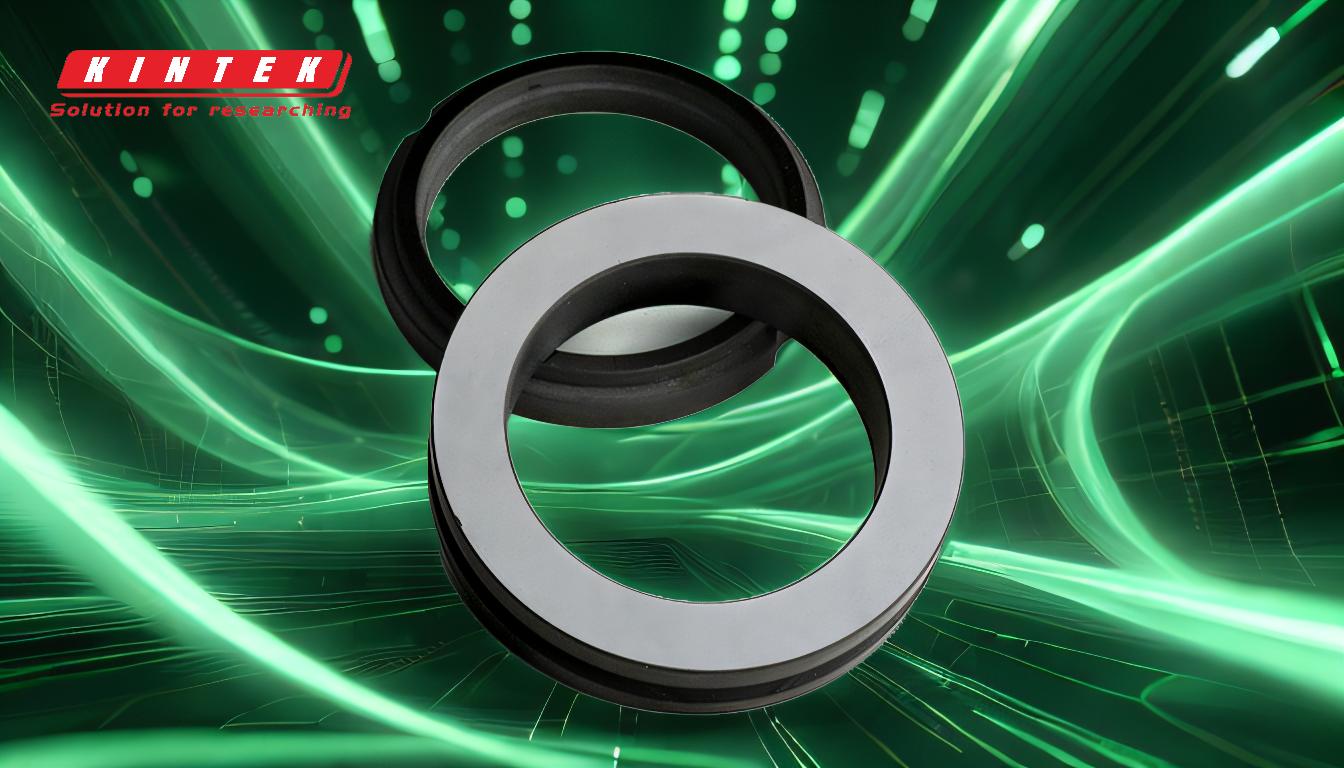
-
Typical Thickness Range of PVD Coatings:
- PVD coatings are generally very thin, ranging from 0.25 microns to 5 microns. This range is significantly thinner than the diameter of a human hair, which is about 70 microns. The thinness ensures that the coating does not alter the dimensions or specifications of the underlying material, making it ideal for precision applications.
-
Applications and Thickness Variations:
- The thickness of PVD coatings can vary depending on the application. For example:
- In jewelry, the coating thickness typically ranges from 0.25 microns to 5 microns, providing a durable and aesthetically pleasing finish.
- In industrial applications, such as coating wafers, thicknesses can be as low as 3 nanometers, as seen in the example of a Gold/Palladium coating applied to a 6-inch wafer using a sputter coater.
- The thickness of PVD coatings can vary depending on the application. For example:
-
Comparison with Other Coating Methods:
- PVD coatings are thinner than those produced by Chemical Vapor Deposition (CVD), which typically range between 5-10 microns. Despite their thinness, PVD coatings are harder, more corrosion-resistant, and more environmentally friendly than traditional methods like electroplating and painting.
-
Durability and Longevity:
- PVD coatings are known for their durability, lasting anywhere from 10 years to hundreds of years depending on factors such as:
- The substrate material being coated.
- The thickness of the coating.
- The application conditions, such as exposure to high temperatures or corrosive environments.
- PVD coatings are known for their durability, lasting anywhere from 10 years to hundreds of years depending on factors such as:
-
Advantages of PVD Coatings:
- Hardness and Corrosion Resistance: PVD coatings are harder and more resistant to corrosion than electroplated coatings.
- High-Temperature Performance: They can withstand high temperatures and have good impact strength.
- Abrasion Resistance: With an additional clear abrasion-resistant top coat, PVD coatings achieve excellent resistance to wear and tear.
- Environmental Friendliness: PVD is a more sustainable and eco-friendly process compared to traditional coating methods.
-
Production Process:
- PVD coatings are produced by the condensation of vapors of materials such as metals, carbon, ceramics, glass, or polymers on a suitable surface. The two most widely used PVD coating technologies are:
- Evaporation: Involves heating the coating material until it vaporizes and then depositing it onto the substrate.
- Sputtering: Uses a plasma to eject atoms from a target material, which then deposit onto the substrate.
- PVD coatings are produced by the condensation of vapors of materials such as metals, carbon, ceramics, glass, or polymers on a suitable surface. The two most widely used PVD coating technologies are:
-
Importance of Thinness:
- The thinness of PVD coatings (0.5 microns to 5 microns) ensures that they do not alter the specifications of engineered parts. This is particularly important in industries where precision and dimensional accuracy are critical, such as in electronics and aerospace.
By understanding the size and properties of PVD coatings, purchasers can make informed decisions about their suitability for specific applications, ensuring optimal performance and longevity.
Summary Table:
Key Aspect | Details |
---|---|
Typical Thickness Range | 0.25 microns to 5 microns |
Applications | Jewelry (0.25-5 microns), Industrial (as low as 3 nanometers) |
Comparison with CVD | Thinner (5-10 microns for CVD), harder, and more corrosion-resistant |
Durability | 10 years to hundreds of years, depending on substrate and conditions |
Advantages | High hardness, corrosion resistance, high-temperature performance |
Production Process | Evaporation and sputtering |
Importance of Thinness | Maintains part specifications, ideal for precision applications |
Ready to enhance your applications with PVD coatings? Contact us today to learn more!