Plasma deposition is a complex process where temperature plays a critical role in determining the quality and properties of the deposited thin film. The process involves the use of high-energy charged particles in a plasma to liberate atoms from a target material, which then deposit onto a substrate. The temperature at which plasma deposition occurs can vary widely depending on the specific method and materials involved. For instance, in chemical vapor deposition (CVD) of diamond films, the tungsten wire must be heated to 2000–2200°C to activate and crack gas into atomic hydrogen hydrocarbon groups, while the substrate temperature must not exceed 1200°C to prevent graphitization. The plasma itself is ignited by electrical discharge (100 – 300 eV), creating a glowing sheath around the substrate that contributes to thermal energy driving the chemical reactions. Higher gas flow rates and operating temperatures can yield higher deposition rates and control properties such as thickness, hardness, or refractive index of the deposited films. The process temperature significantly affects the characteristics of the film, and the application can impose limits on the temperature that can be used, as higher temperatures may alter the film's properties.
Key Points Explained:
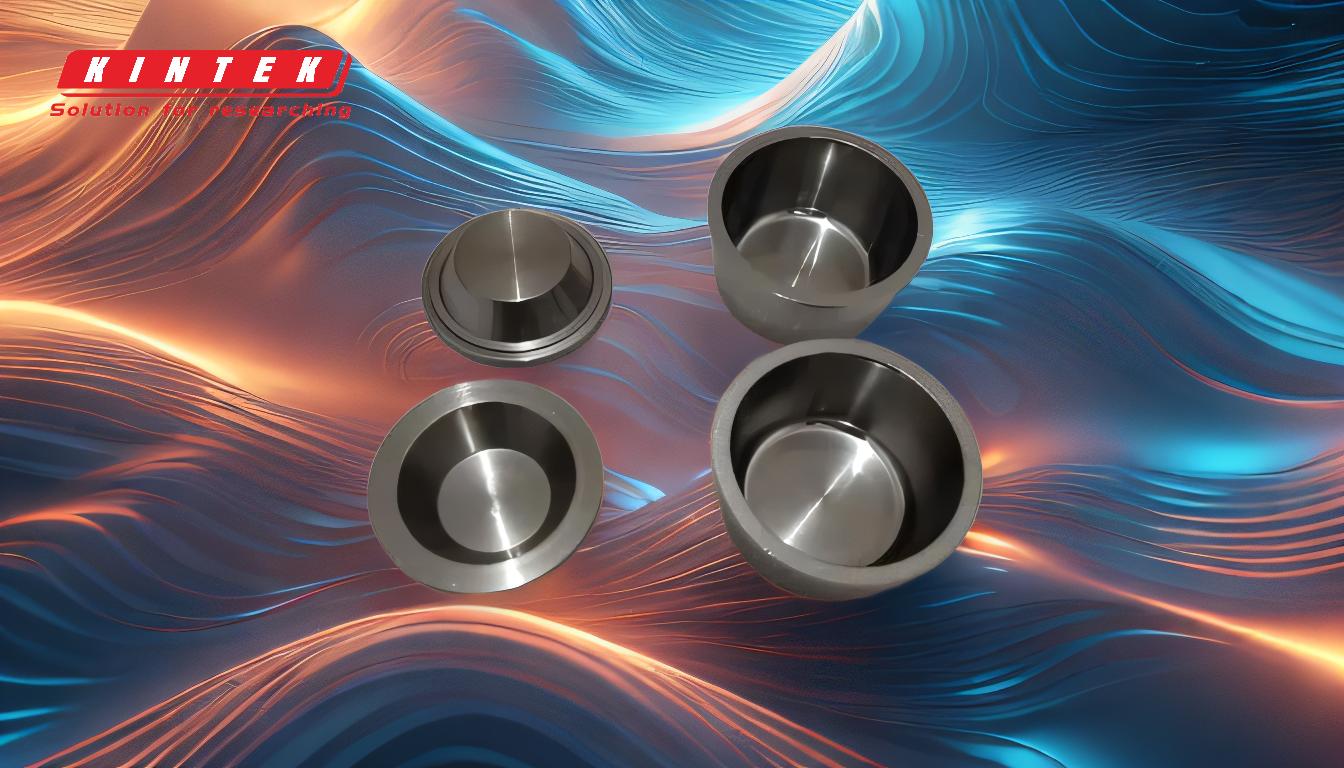
-
Temperature Range in Plasma Deposition:
- Tungsten Wire Temperature: In chemical vapor deposition (CVD) of diamond films, the tungsten wire must be heated to a high temperature range of 2000–2200°C. This high temperature is necessary to activate and crack the gas into atomic hydrogen hydrocarbon groups, which are essential for diamond film formation.
- Substrate Temperature: The substrate temperature, controlled by tungsten wire radiation and cooling water, must not exceed 1200°C. This limit is crucial to prevent graphitization, which can degrade the quality of the diamond film.
-
Plasma Ignition and Thermal Energy:
- Electrical Discharge: Plasma is ignited by an electrical discharge with energies ranging from 100 to 300 eV. This discharge creates a glowing sheath around the substrate, contributing to the thermal energy that drives the chemical reactions necessary for deposition.
- Thermal Equilibrium: In plasma-enhanced chemical vapor deposition (PECVD), using an electrode that can operate at high temperatures reduces the need for high plasma power. Thermal equilibrium on the substrate surface aids in creating good crystal quality in the deposited film.
-
Influence of Gas Flow Rates and Operating Temperatures:
- Deposition Rates: Higher gas flow rates can yield higher deposition rates. Along with operating temperatures, these factors control properties such as thickness, hardness, or refractive index of the deposited films.
- Film Properties: The process temperature significantly affects the characteristics of the film in thin film deposition. The application can impose limits on the temperature that can be used, as higher temperatures may alter the film's properties.
-
Plasma Characteristics and Elemental Composition:
- Plasma Temperature, Composition, and Density: The plasma deposition process is strongly influenced by the characteristics of the plasma, such as temperature, composition, and density. These factors must be carefully controlled to ensure the desired material composition and to check for contamination.
- Elemental Composition Monitoring: Monitoring the elemental composition in the chamber is crucial to ensure the desired material composition is correct and to check for contamination, which can affect the quality of the deposited film.
-
Application-Specific Temperature Limits:
- Temperature Constraints: Different applications may impose specific temperature limits on the plasma deposition process. For example, in the deposition of diamond films, the substrate temperature must be carefully controlled to prevent graphitization, while in other applications, higher temperatures may be required to achieve the desired film properties.
- Thermal Management: Effective thermal management is essential to maintain the desired temperature range and ensure the quality of the deposited film. This may involve the use of cooling systems, such as cooling water, to control the substrate temperature.
In summary, the temperature at which plasma deposition occurs is a critical factor that influences the quality and properties of the deposited thin film. The process involves a complex interplay of high temperatures, plasma characteristics, and thermal management to achieve the desired outcomes. Understanding and controlling these factors is essential for successful plasma deposition in various applications.
Summary Table:
Key Factor | Details |
---|---|
Tungsten Wire Temperature | 2000–2200°C for CVD diamond films, activates gas for atomic hydrogen groups. |
Substrate Temperature | ≤1200°C to prevent graphitization in diamond film deposition. |
Plasma Ignition | 100–300 eV electrical discharge creates thermal energy for reactions. |
Deposition Rates | Higher gas flow rates and temperatures increase deposition rates. |
Film Properties | Temperature affects thickness, hardness, and refractive index of films. |
Thermal Management | Cooling systems like water are used to control substrate temperature. |
Optimize your plasma deposition process with expert guidance—contact us today!