Crushing and grinding processes, while essential for sample preparation, can introduce various forms of contamination and compositional changes. These issues arise from factors such as tool wear, loss of volatile compounds, moisture changes, nonuniform grinding due to material hardness variations, and atmospheric reactions. Understanding these potential issues is critical for ensuring the accuracy and reliability of analytical results, particularly in fields like material science, geology, and chemistry.
Key Points Explained:
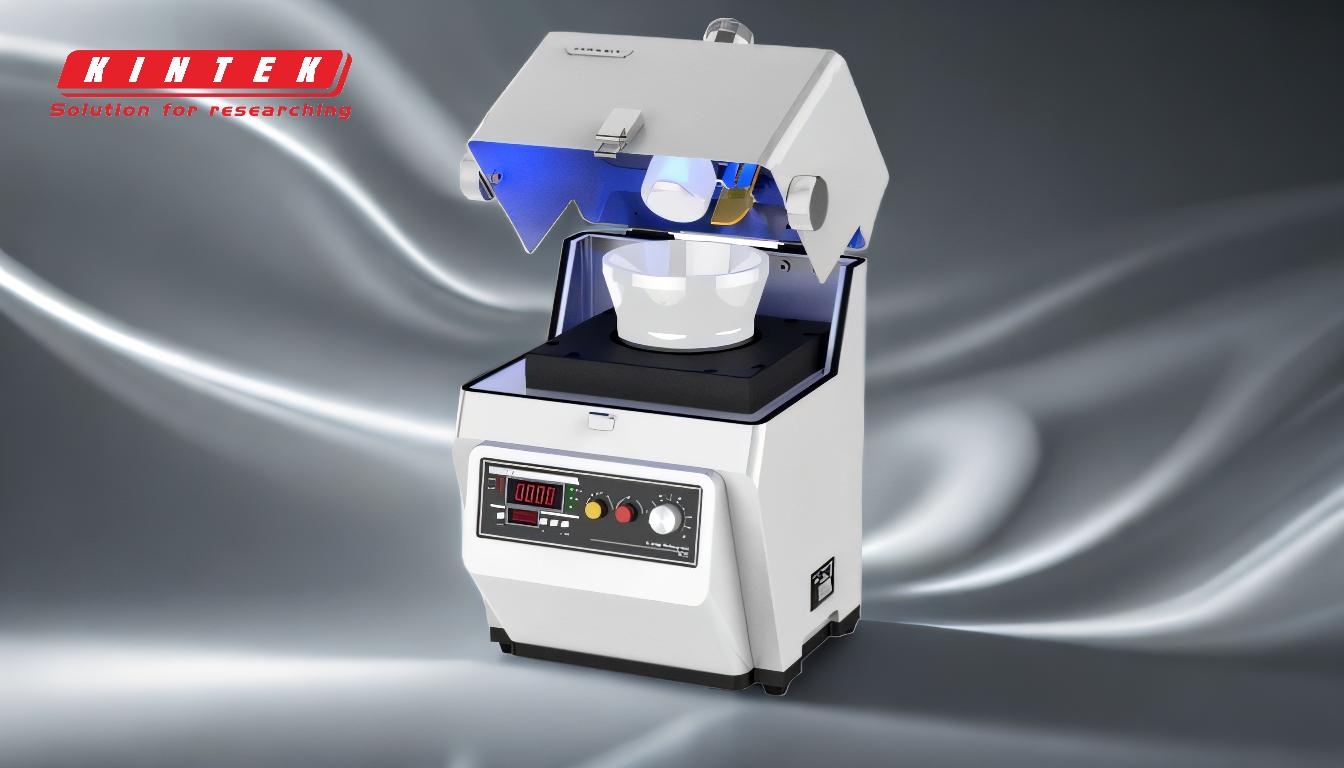
-
Contamination from Grinding Tools
- Mechanism: During grinding, the tools (e.g., mortars, mills, or grinding balls) can lose material due to wear and abrasion. This material can mix with the sample, leading to contamination.
- Impact: The introduction of foreign materials can alter the sample's composition, leading to inaccurate analytical results. For example, if a steel grinding tool is used, iron particles might contaminate the sample, affecting trace element analysis.
- Mitigation: Using grinding tools made of materials that match the sample's composition or are inert (e.g., agate or zirconia) can minimize contamination. Regular tool maintenance and cleaning are also essential.
-
Loss of Volatile Compounds
- Mechanism: Crushing and grinding can generate heat, causing volatile compounds (e.g., organic solvents, water, or gases) to evaporate or decompose.
- Impact: The loss of volatile components can significantly alter the sample's chemical composition, particularly in organic or hydrated materials. For example, grinding a hydrated mineral might lead to the loss of water, affecting its structural and chemical properties.
- Mitigation: Performing grinding at lower temperatures or under controlled atmospheres can help preserve volatile compounds. Cryogenic grinding (using liquid nitrogen) is often employed for heat-sensitive materials.
-
Moisture Changes (Loss or Gain of Water)
- Mechanism: The grinding process can expose the sample to ambient conditions, leading to either the loss of water (dehydration) or the absorption of moisture (hydration).
- Impact: Changes in moisture content can affect the sample's weight, chemical reactivity, and structural integrity. For instance, some minerals may undergo phase transitions or structural collapse upon dehydration.
- Mitigation: Grinding in a controlled humidity environment or using airtight containers can help maintain consistent moisture levels.
-
Nonuniform Grinding Due to Variable Hardness
- Mechanism: Samples with components of varying hardness (e.g., a mixture of soft and hard minerals) may grind unevenly, leading to a nonrepresentative particle size distribution.
- Impact: Nonuniform grinding can result in biased analytical results, as softer components may be overrepresented in the finer fraction, while harder components remain in larger particles.
- Mitigation: Pre-crushing or sieving the sample to ensure uniformity before grinding can help achieve a more representative particle size distribution. Using grinding tools with adjustable settings can also improve consistency.
-
Atmospheric Reactions
- Mechanism: Exposure to air during grinding can lead to oxidation, carbonation, or other chemical reactions, especially in reactive materials like metals or sulfides.
- Impact: Atmospheric reactions can alter the sample's chemical composition, leading to inaccurate results. For example, iron-containing samples might oxidize, forming iron oxides that were not originally present.
- Mitigation: Grinding under inert atmospheres (e.g., nitrogen or argon) can prevent unwanted reactions. Sealed grinding chambers or glove boxes are often used for sensitive materials.
By addressing these potential issues through careful selection of grinding tools, controlled environmental conditions, and appropriate grinding techniques, the integrity of the sample can be preserved, ensuring accurate and reliable analytical outcomes.
Summary Table:
Issue | Mechanism | Impact | Mitigation |
---|---|---|---|
Contamination from Grinding Tools | Tool wear introduces foreign materials into the sample. | Alters sample composition, leading to inaccurate results. | Use inert tools (e.g., agate, zirconia) and maintain/clean tools regularly. |
Loss of Volatile Compounds | Heat generated during grinding causes evaporation or decomposition. | Changes chemical composition, especially in organic/hydrated materials. | Grind at lower temperatures or under controlled atmospheres; use cryogenic grinding. |
Moisture Changes | Exposure to ambient conditions leads to dehydration or hydration. | Affects weight, reactivity, and structural integrity. | Grind in controlled humidity or airtight containers. |
Nonuniform Grinding | Variable hardness causes uneven particle size distribution. | Biases analytical results due to overrepresentation of softer components. | Pre-crush or sieve samples; use adjustable grinding tools. |
Atmospheric Reactions | Exposure to air causes oxidation, carbonation, or other reactions. | Alters chemical composition, leading to inaccurate results. | Grind under inert atmospheres (e.g., nitrogen, argon) or use sealed chambers. |
Ensure your sample preparation is contamination-free and accurate—contact our experts today for tailored solutions!