Fluidized bed reactors (FBRs) are versatile and widely used across various industries due to their efficiency, scalability, and ability to handle diverse materials. They are employed in the production of fuels, chemicals, and polymers, as well as in energy generation, waste treatment, and environmental applications. Their unique design, which involves suspending solid particles in a gas or liquid stream, enables rapid heat and mass transfer, making them ideal for processes requiring high reaction rates and uniform temperature distribution. Key applications include fuel production, polymer manufacturing, coal gasification, nuclear power, and water/waste treatment.
Key Points Explained:
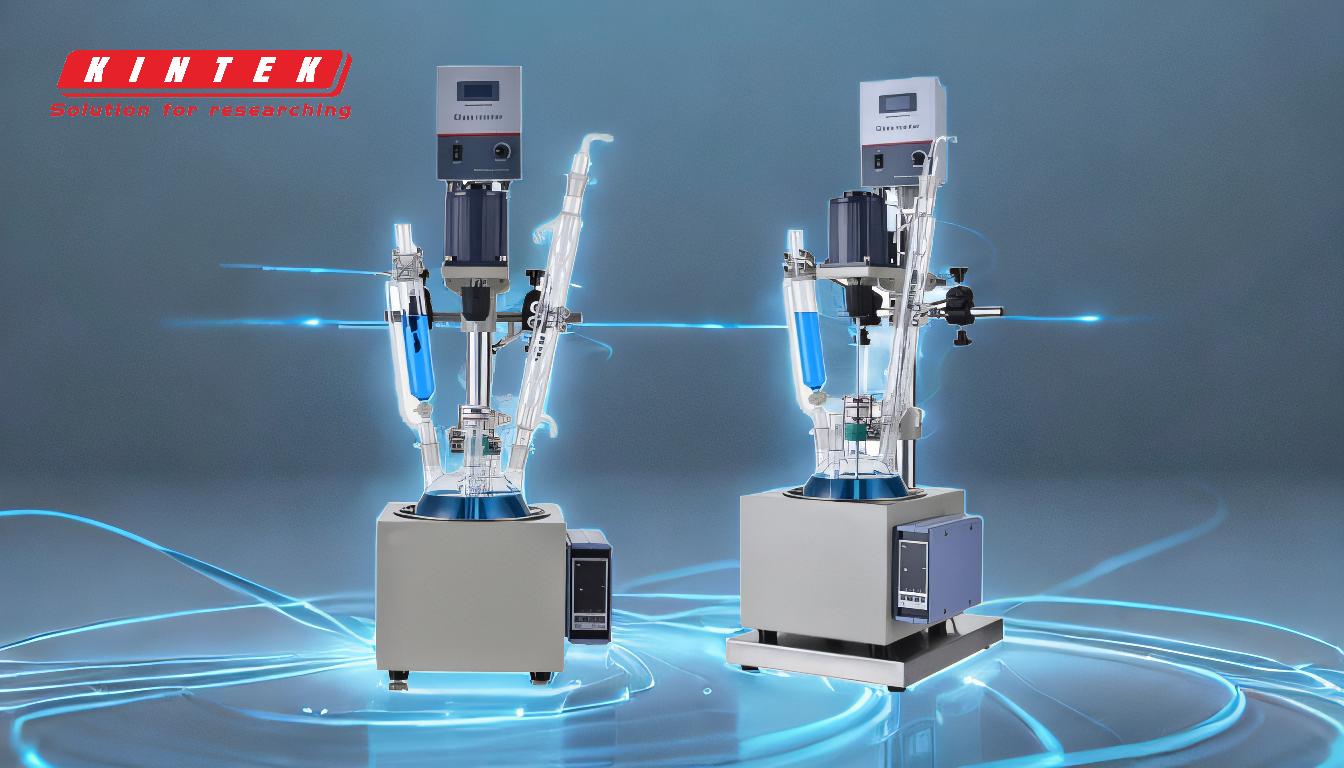
-
Fuel Production:
- Fluidized bed reactors are extensively used in the production of gasoline and other fuels. Their ability to handle a wide range of feedstocks, including heavy oils and biomass, makes them suitable for processes like fluid catalytic cracking (FCC) and pyrolysis.
- Example: Circulating Fluidized Bed (CFB) reactors are employed in co-processing biomass and petroleum feedstocks to produce biofuels and synthetic fuels.
-
Chemical Manufacturing:
- FBRs play a critical role in the production of various chemicals, including polymers like polyethylene, polypropylene, and vinyl chloride. These reactors provide efficient mixing and heat transfer, which are essential for polymerization processes.
- Example: The production of styrenes and rubber often utilizes fluidized bed reactors to achieve high yields and consistent product quality.
-
Polymer Production:
- Industrially important polymers, such as polyethylene and polypropylene, are manufactured using fluidized bed reactors. The reactors' design ensures uniform temperature distribution and efficient catalyst utilization, which are crucial for polymerization reactions.
- Example: The production of polypropylene in FBRs involves the use of catalysts suspended in a fluidized bed, enabling precise control over polymer properties.
-
Coal Gasification:
- Fluidized bed reactors are employed in coal gasification processes to convert coal into synthetic gas (syngas), which can be used for power generation or as a feedstock for chemical production. The reactors' ability to handle solid fuels like coal makes them ideal for this application.
- Example: Circulating Fluidized Bed (CFB) gasifiers are used to produce syngas for integrated gasification combined cycle (IGCC) power plants.
-
Nuclear Power Plants:
- In nuclear power generation, fluidized bed reactors are used for processes such as fuel reprocessing and waste management. Their ability to handle high temperatures and radioactive materials makes them suitable for these applications.
- Example: FBRs are used in the treatment of nuclear waste, where they help immobilize radioactive materials in a stable matrix.
-
Water and Waste Treatment:
- Fluidized bed reactors are employed in water and waste treatment processes to remove contaminants and recover valuable resources. Their high efficiency and ability to handle large volumes make them ideal for environmental applications.
- Example: FBRs are used in wastewater treatment plants to remove organic pollutants and nutrients through biological processes.
-
Biomass and Renewable Energy:
- FBRs are used in the pyrolysis and gasification of biomass to produce bio-oil, syngas, and other renewable energy products. Their ability to handle a variety of feedstocks and provide rapid heating makes them suitable for biomass conversion.
- Example: Circulating Fluidized Bed (CFB) reactors are used in biomass gasification to produce renewable fuels and chemicals.
-
Catalyst and Feedstock Evaluation:
- Fluidized bed reactors are used for testing and evaluating catalysts and feedstocks in various industrial processes. Their design allows for precise control over reaction conditions, making them ideal for research and development.
- Example: FBRs are used in fluid catalytic cracking (FCC) analog processes to test new catalysts and optimize production conditions.
-
Advantages of Fluidized Bed Reactors:
- Rapid reaction and heat transfer: FBRs provide efficient heat and mass transfer, enabling faster reactions and higher productivity.
- Wide contact area: The fluidized bed ensures a large contact area between the fluid and solid phases, enhancing reaction efficiency.
- Scalability: FBRs can be easily scaled up for industrial applications, making them suitable for large-scale production.
- Environmental benefits: FBRs offer cleaner and more efficient processes compared to traditional reactor technologies, reducing emissions and waste.
In summary, fluidized bed reactors are indispensable in modern industrial processes due to their versatility, efficiency, and ability to handle a wide range of materials and applications. From fuel production to environmental remediation, FBRs continue to play a crucial role in advancing technology and sustainability.
Summary Table:
Application | Key Use Cases |
---|---|
Fuel Production | Gasoline, biofuels, synthetic fuels via fluid catalytic cracking (FCC) & pyrolysis |
Chemical Manufacturing | Production of polyethylene, polypropylene, styrenes, and rubber |
Polymer Production | Polyethylene & polypropylene with uniform temperature distribution |
Coal Gasification | Conversion of coal to syngas for power generation & chemical production |
Nuclear Power Plants | Fuel reprocessing & nuclear waste treatment |
Water & Waste Treatment | Removal of contaminants & resource recovery in wastewater treatment |
Biomass & Renewable Energy | Pyrolysis & gasification of biomass for bio-oil & syngas production |
Catalyst Evaluation | Testing & optimizing catalysts for industrial processes |
Discover how fluidized bed reactors can revolutionize your industrial processes—contact our experts today!